Diverse Experience.
Proven Approach.
VECA’s extensive experience in multiple markets creates confidence in our ability to execute successful projects of any size, scope, and complexity for public and private clients.
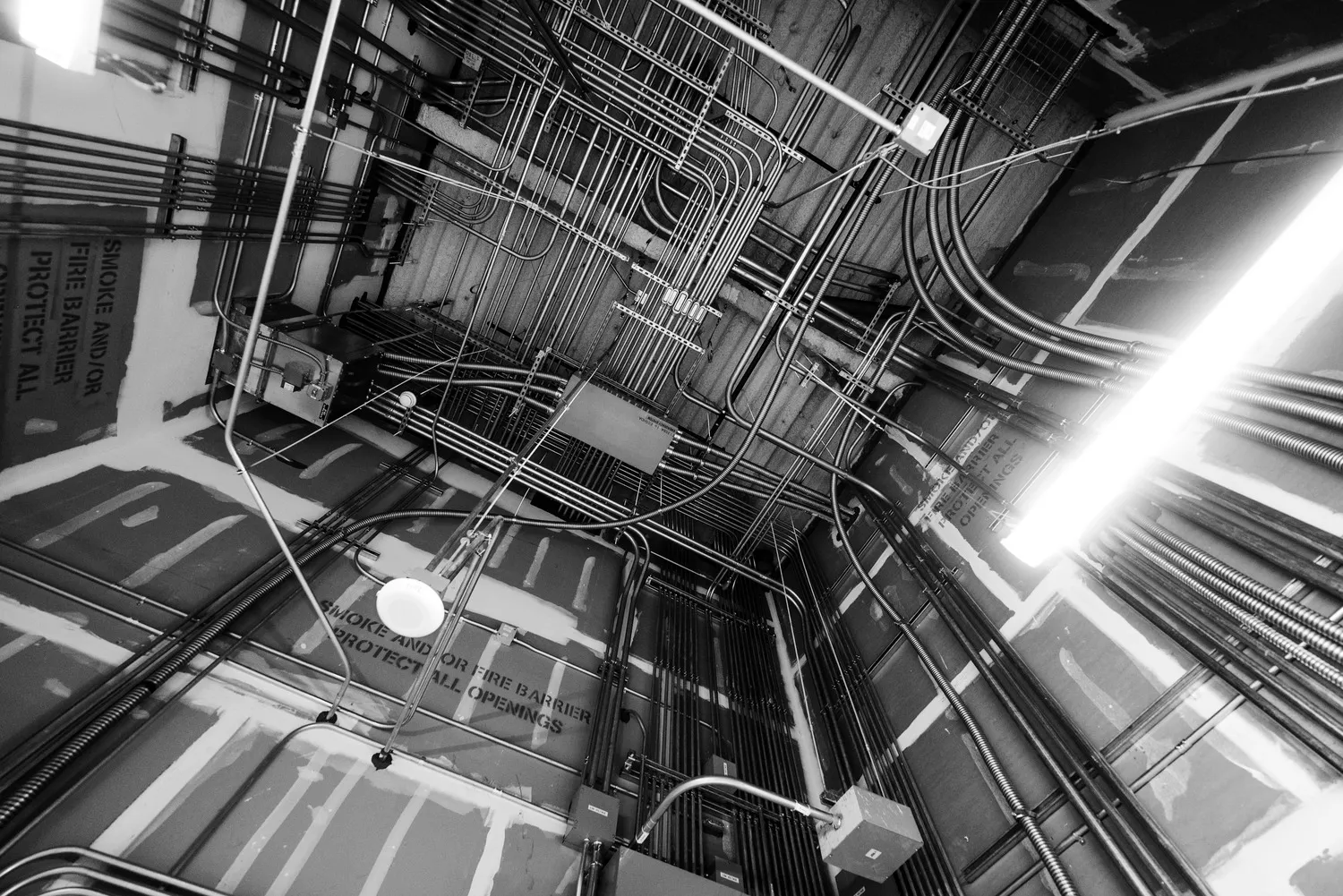
Thank you! Your submission has been received!
Oops! Something went wrong while submitting the form.
No results available for selected parameters
Select “VIEW ALL” or remove filters to view more projects.
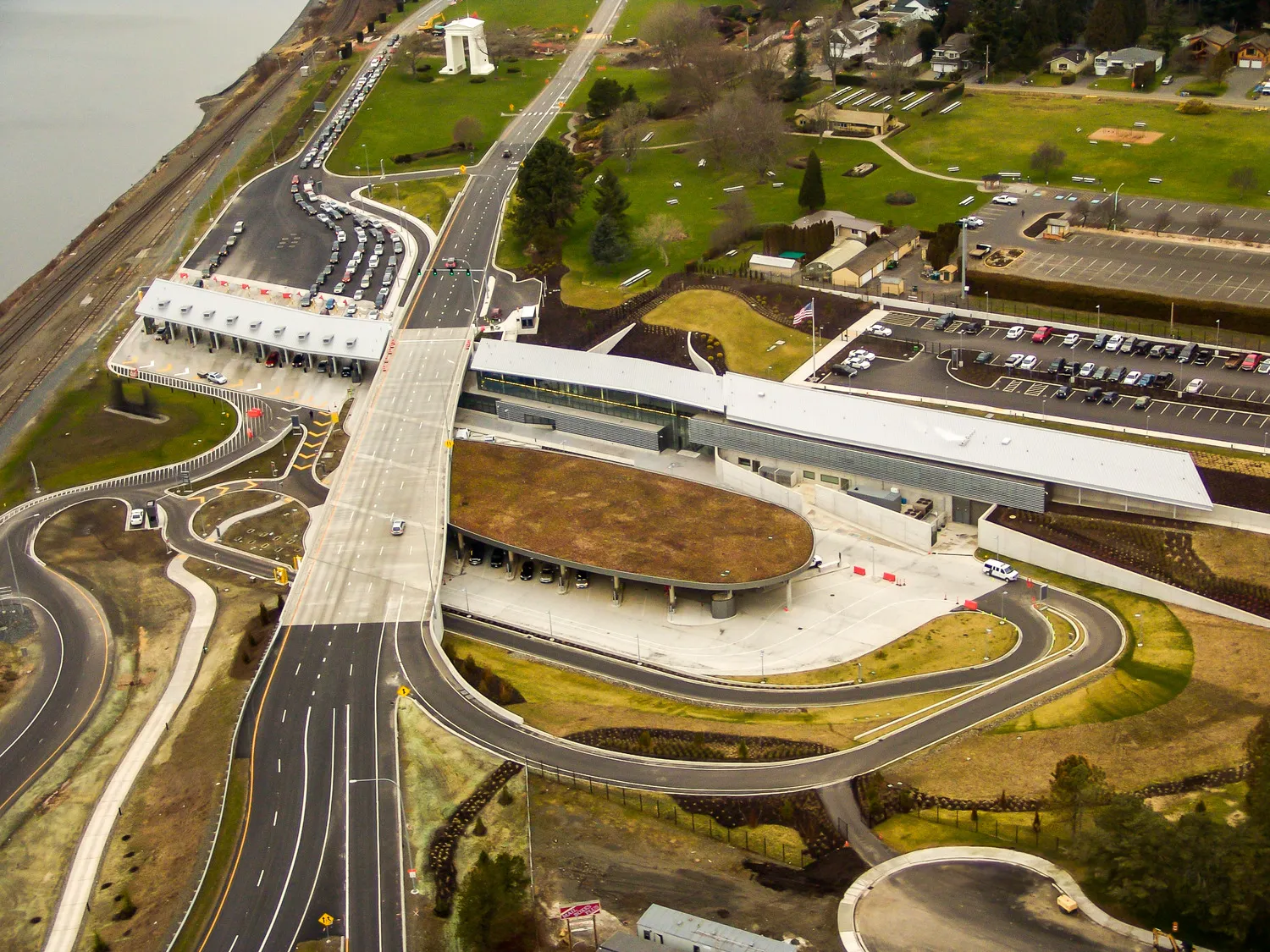
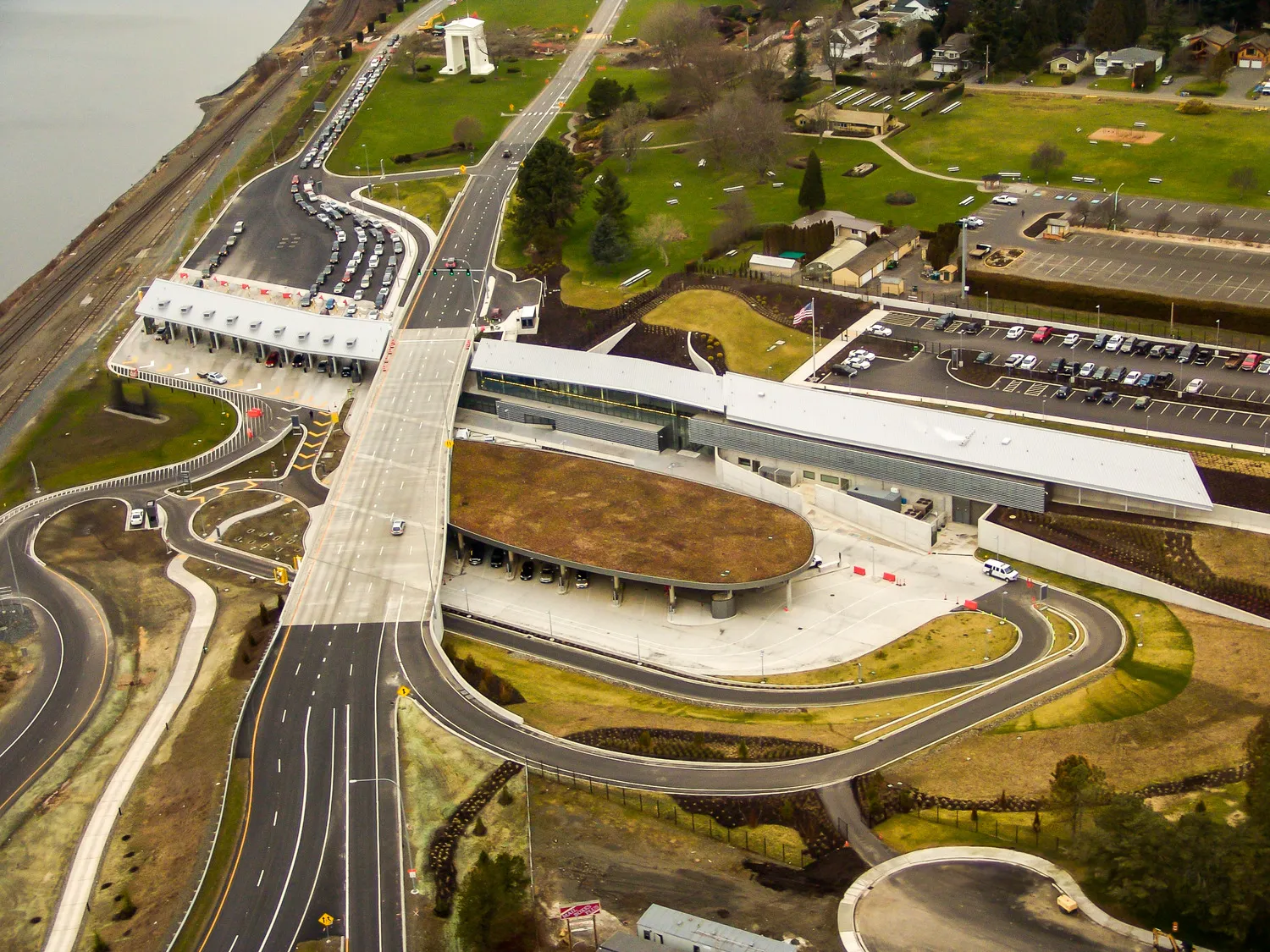
Peace Arch U.S. Port of Entry Facility
Government
Peace Arch U.S. Port of Entry Facility
Government
Government
Electrical
Sustainability
Bellingham
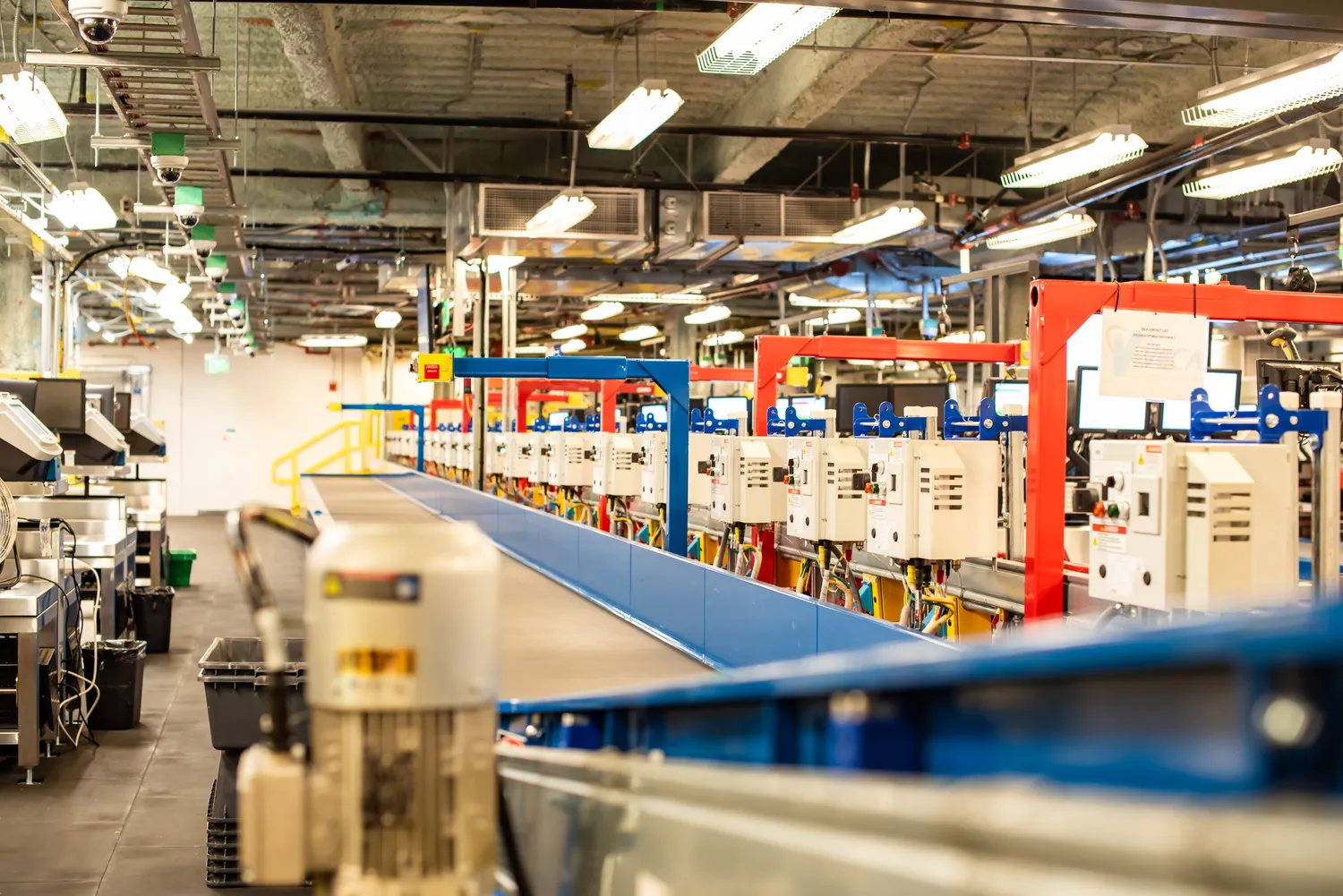
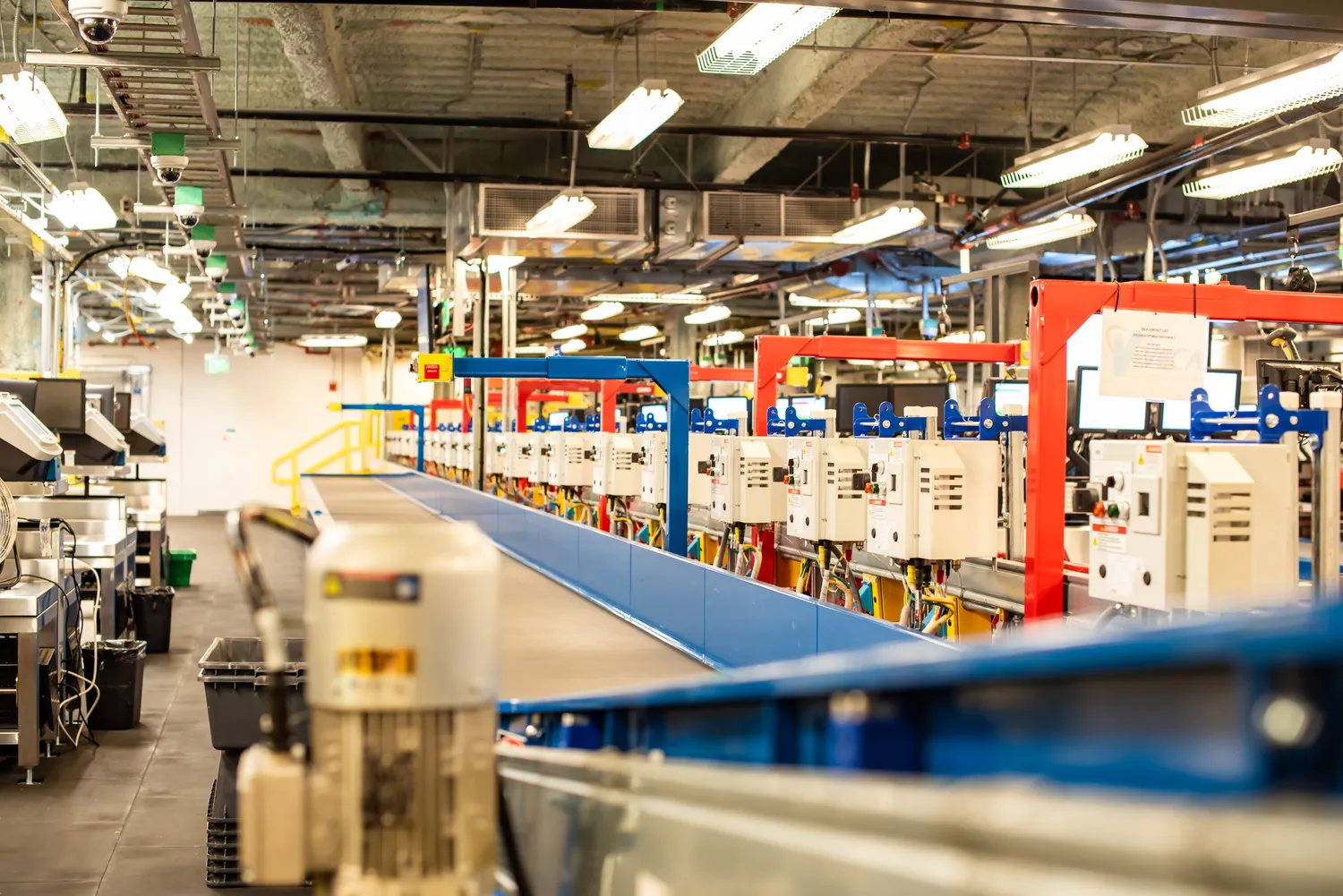
SEA - Baggage Optimization Project - Phase 2
Transportation Infrastructure
SEA - Baggage Optimization Project - Phase 2
Transportation Infrastructure
Transportation Infrastructure
Electrical, Technologies
Diversity, Fabrication, VDC
Seattle
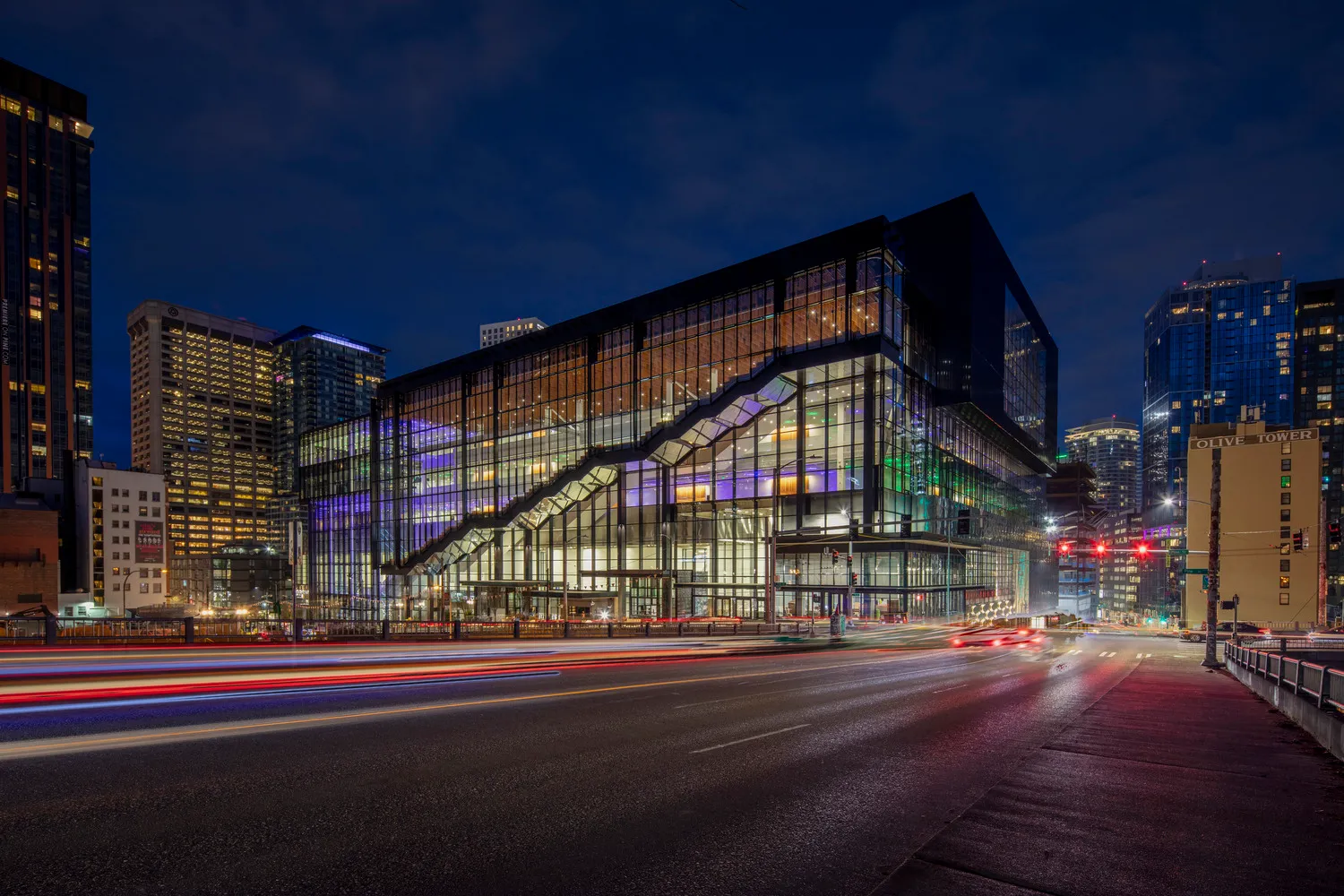
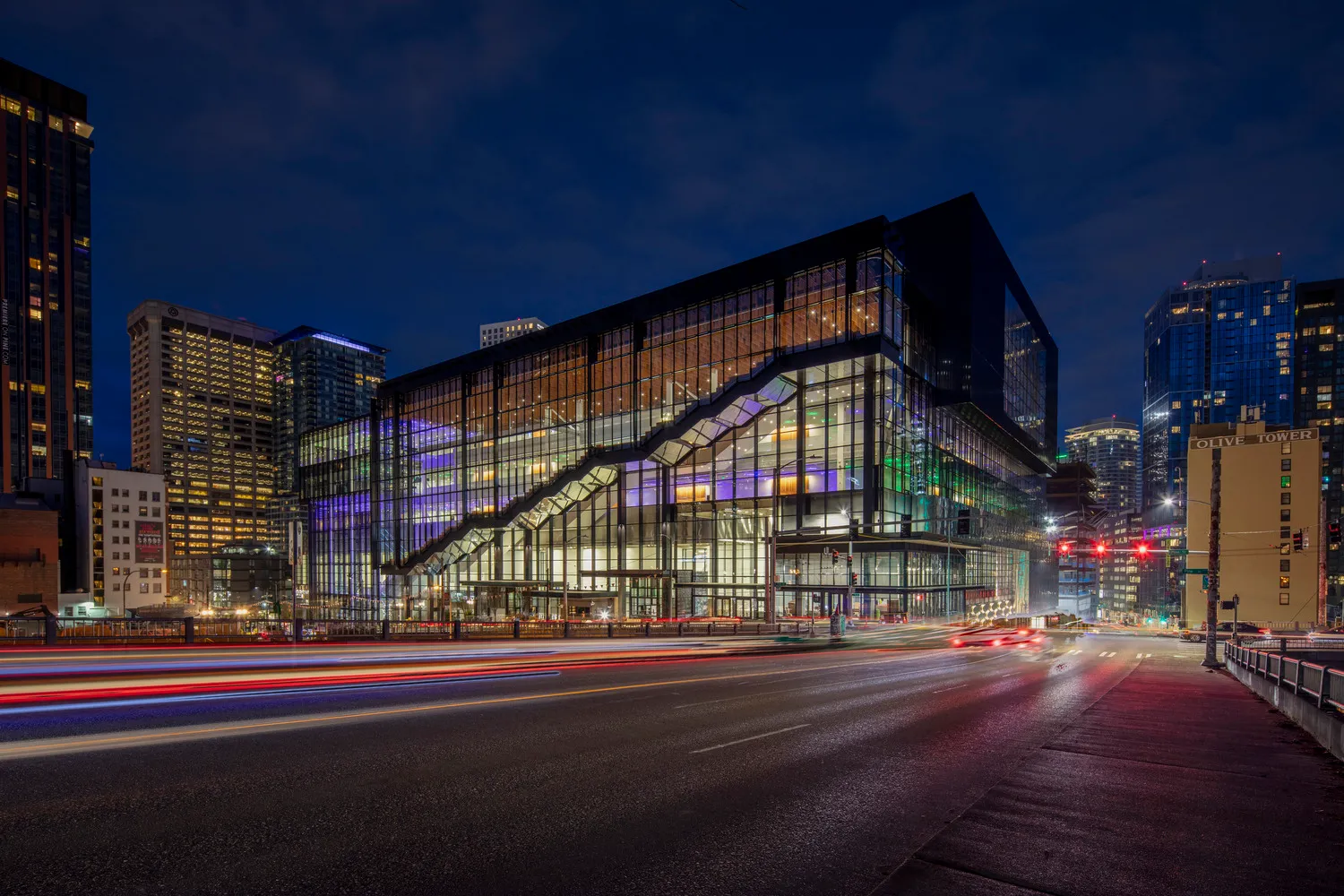
Summit – Washington State Convention Center Addition
Commercial
Summit – Washington State Convention Center Addition
Commercial
Commercial
Electrical
VDC, Fabrication, Sustainability, Alternative Delivery, Diversity
Seattle
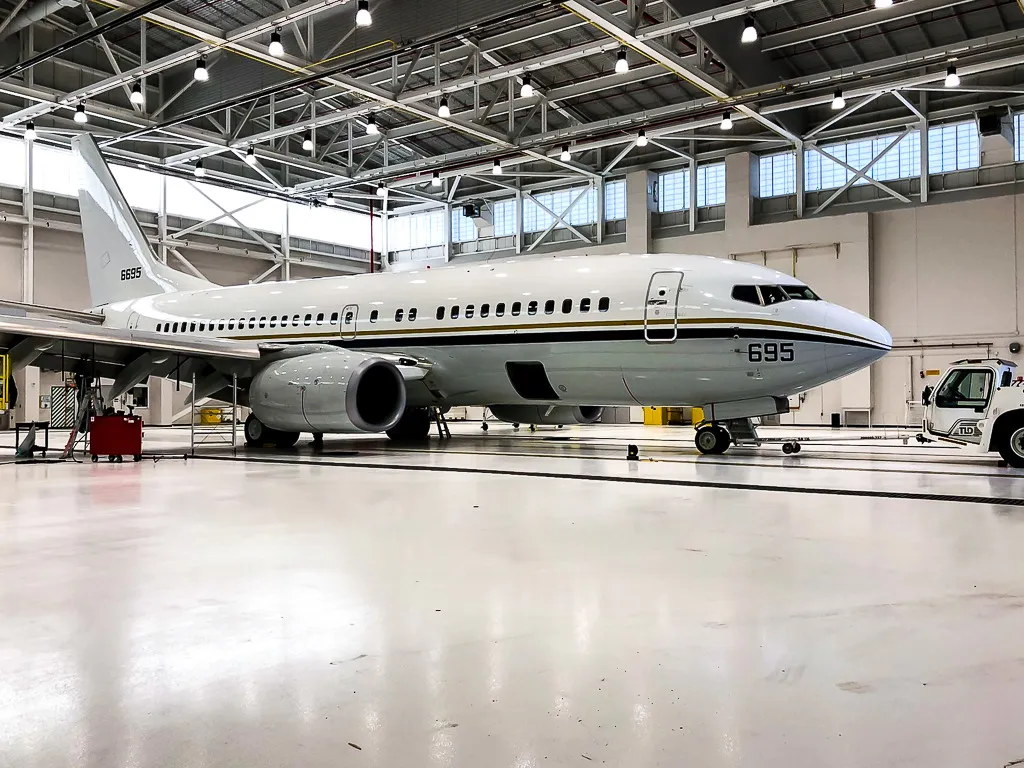
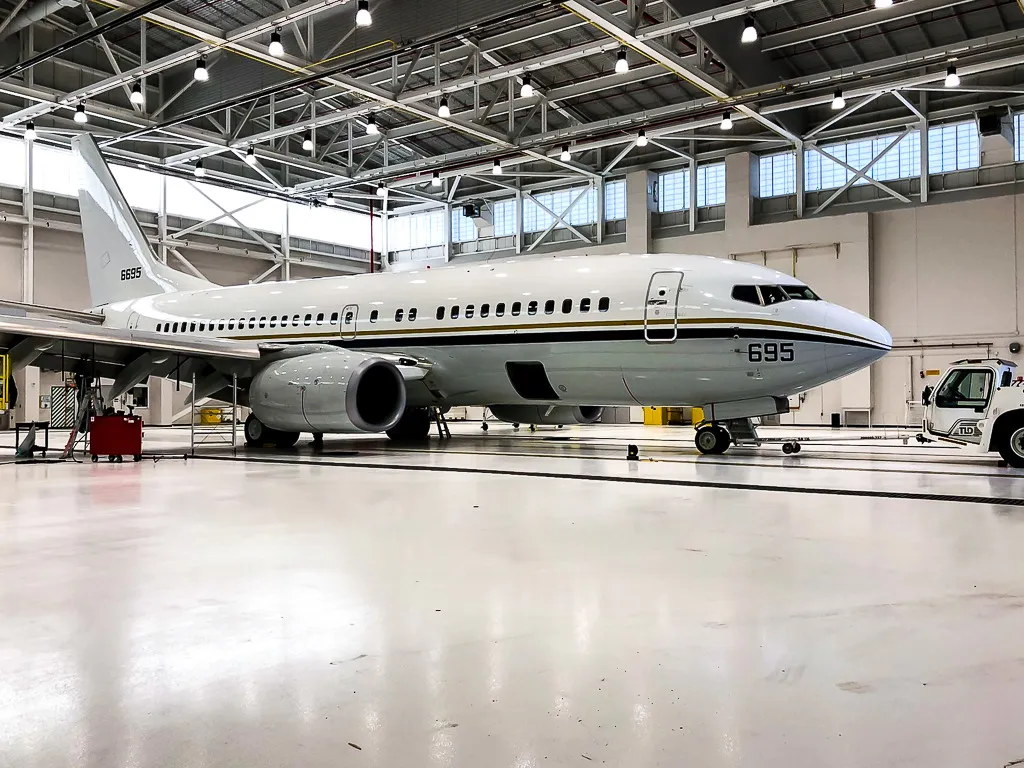
P234 C-40 Aircraft Maintenance Hangar
Government
P234 C-40 Aircraft Maintenance Hangar
Government
Government
Electrical
Sustainability
Bellingham
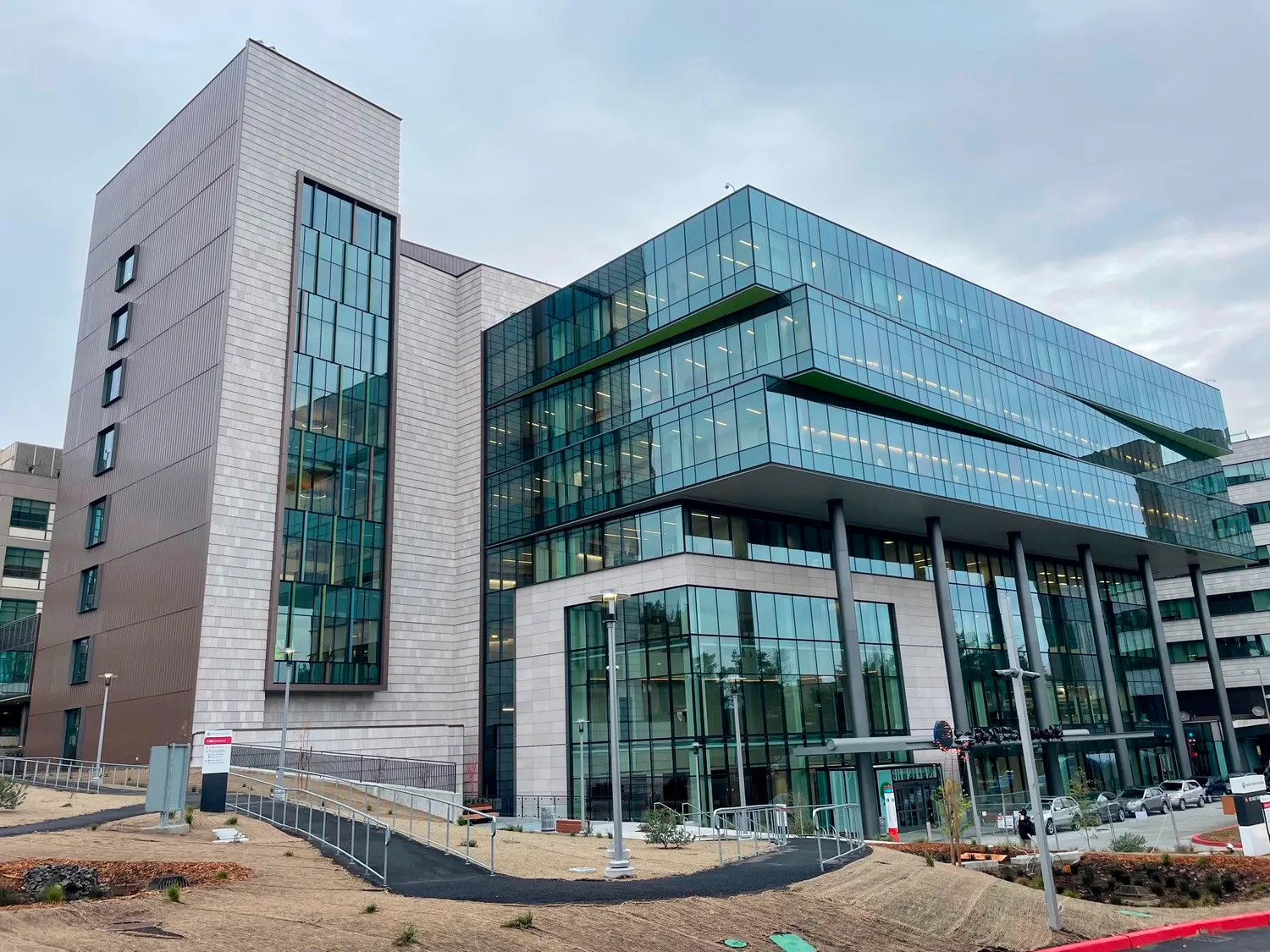
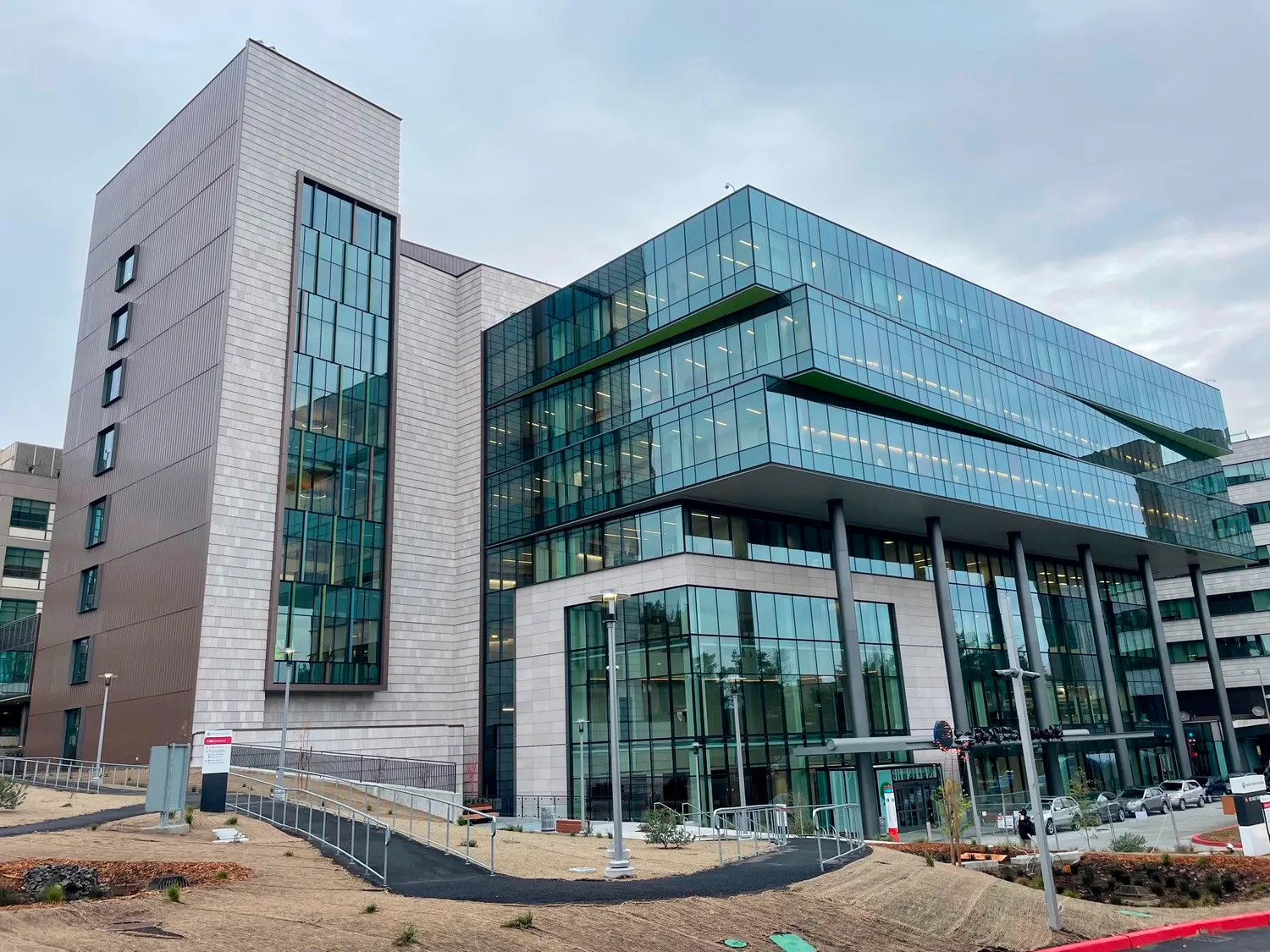
Seattle Children's Hospital - Forest B
Healthcare
Seattle Children's Hospital - Forest B
Healthcare
Healthcare
Electrical, Technologies
Fabrication, Diversity
Seattle
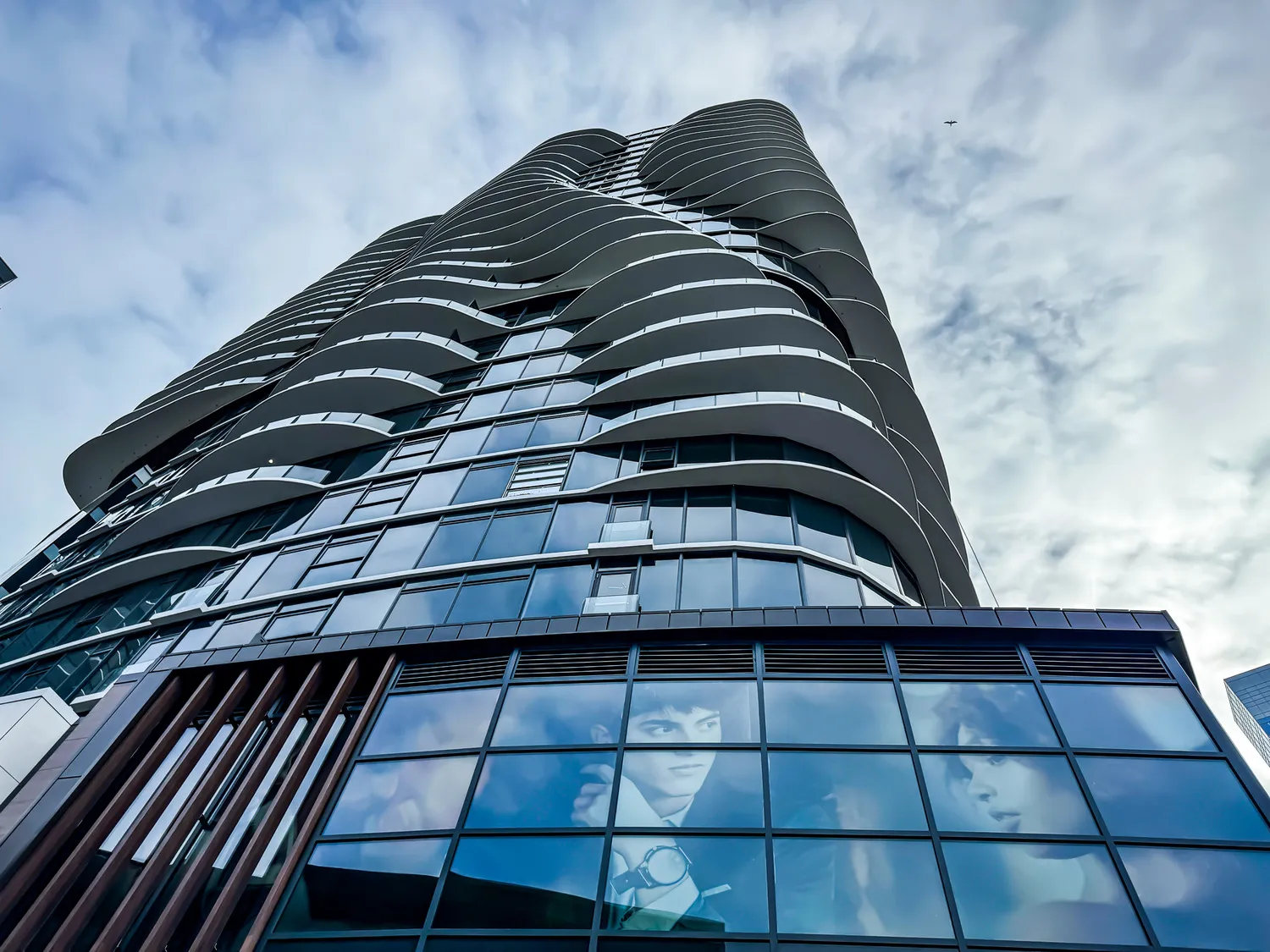
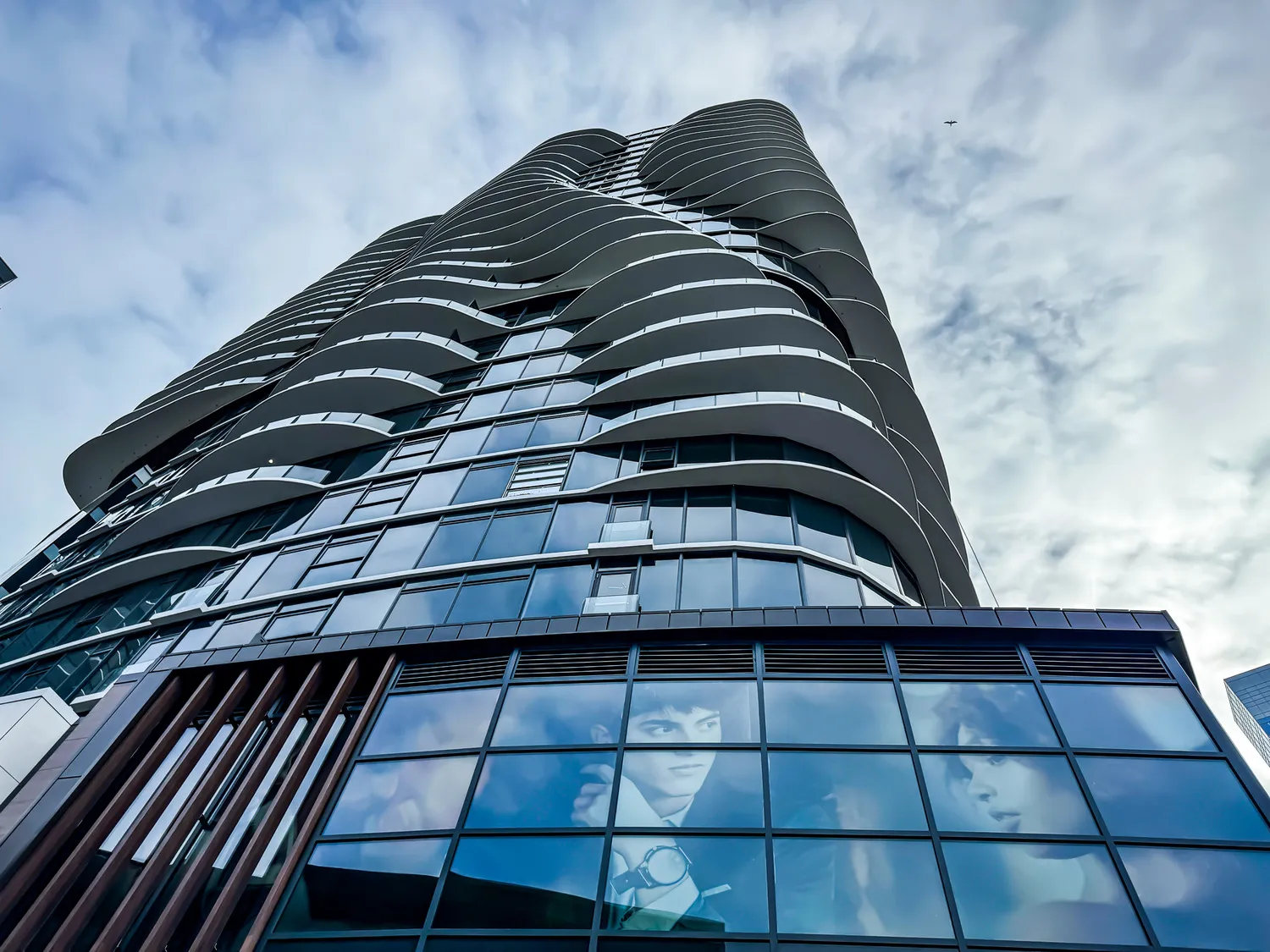
Avenue Bellevue
Commercial
Avenue Bellevue
Commercial
Commercial
Electrical, Technologies
Fabrication, VDC
Seattle
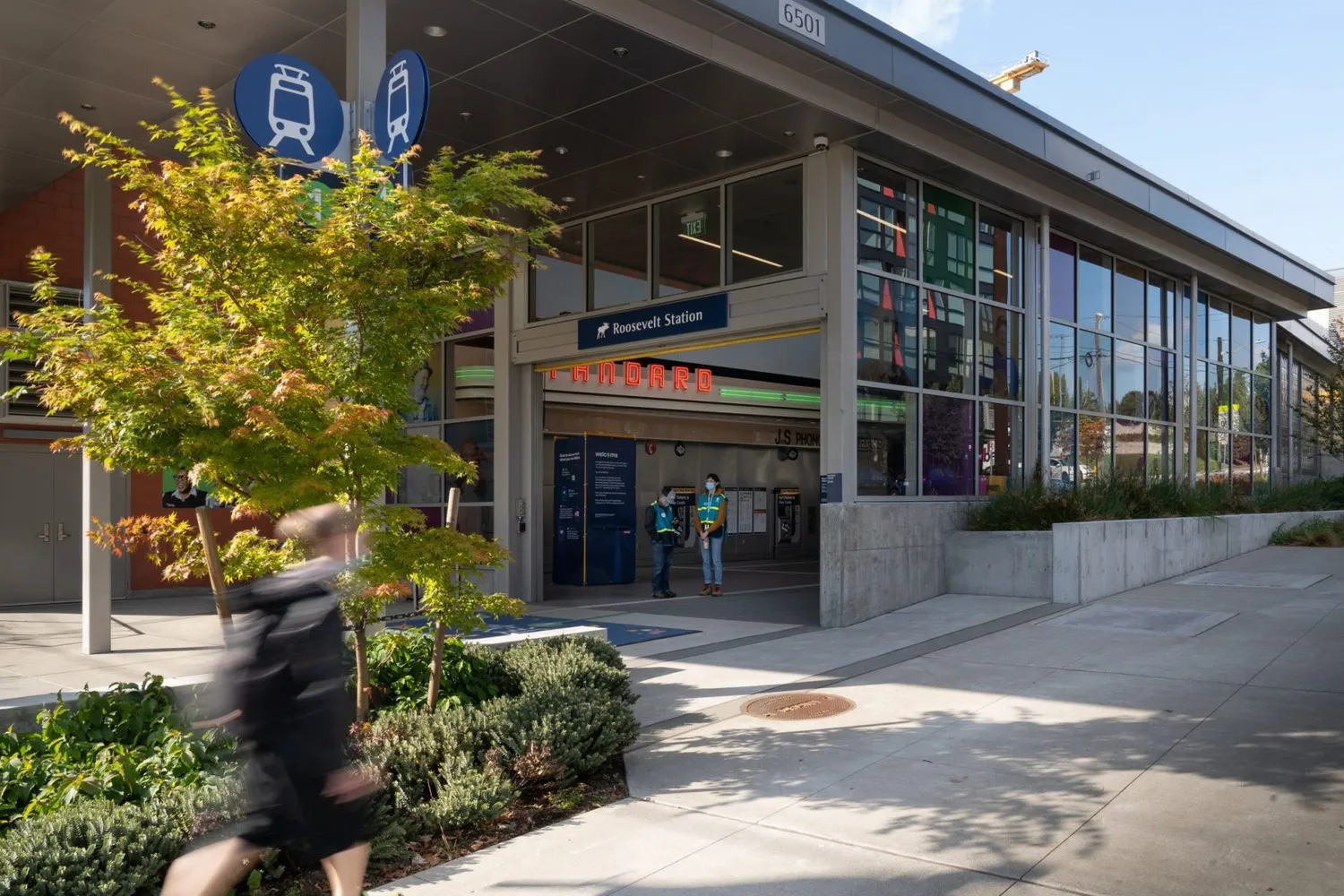
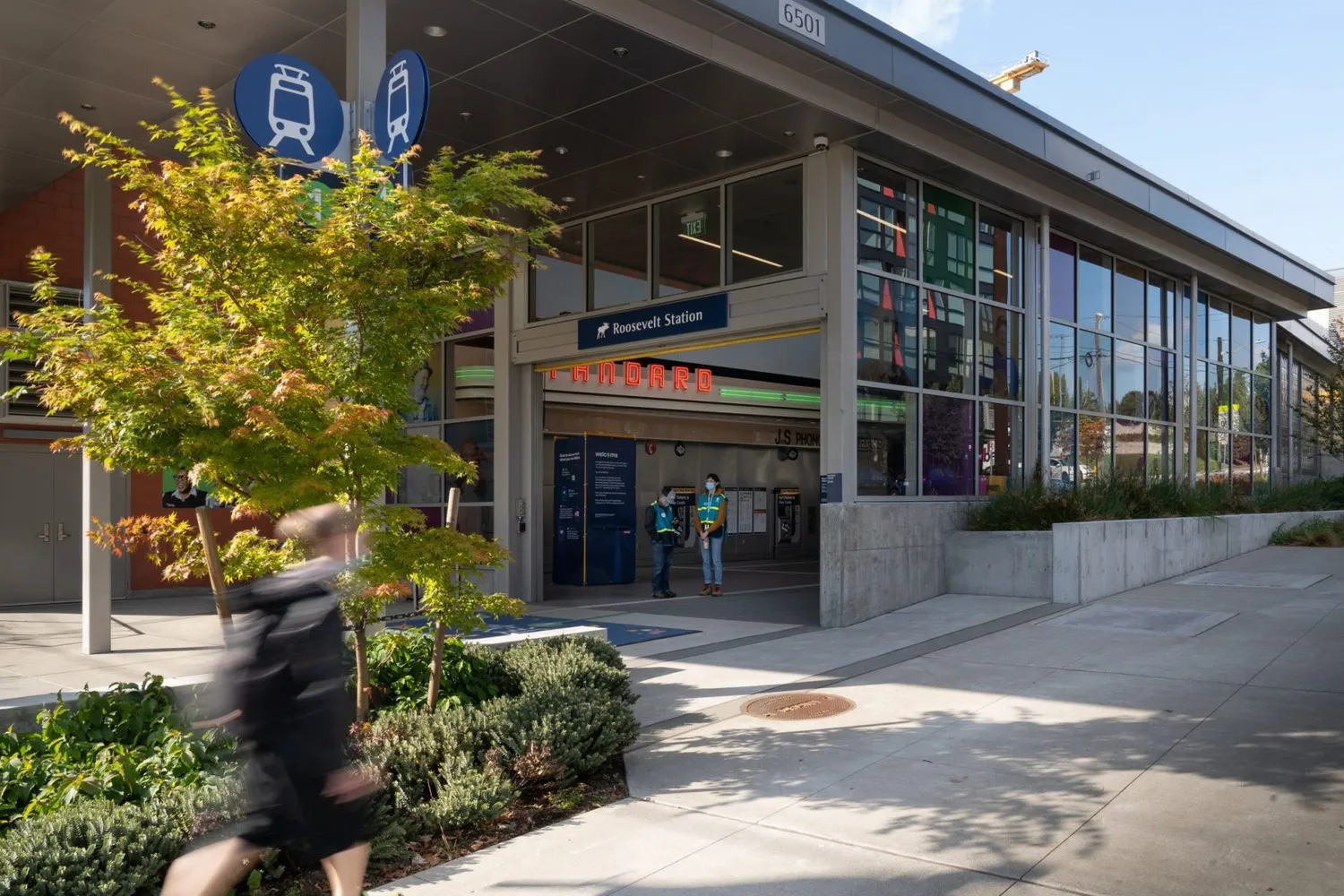
Sound Transit - N150 Roosevelt Station
Transportation Infrastructure
Sound Transit - N150 Roosevelt Station
Transportation Infrastructure
Transportation Infrastructure
Electrical
VDC, Preconstruction, Fabrication, Diversity
Seattle
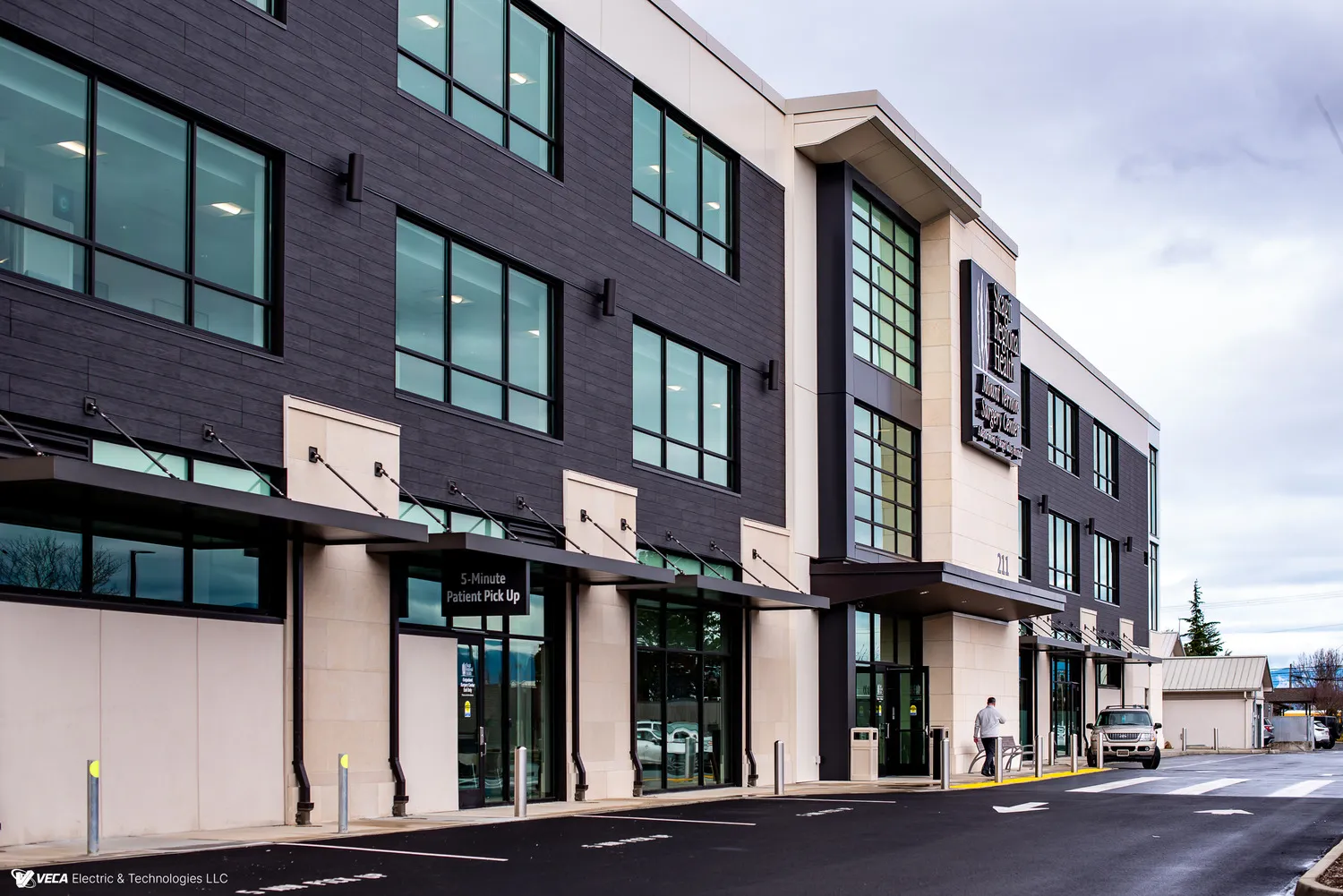
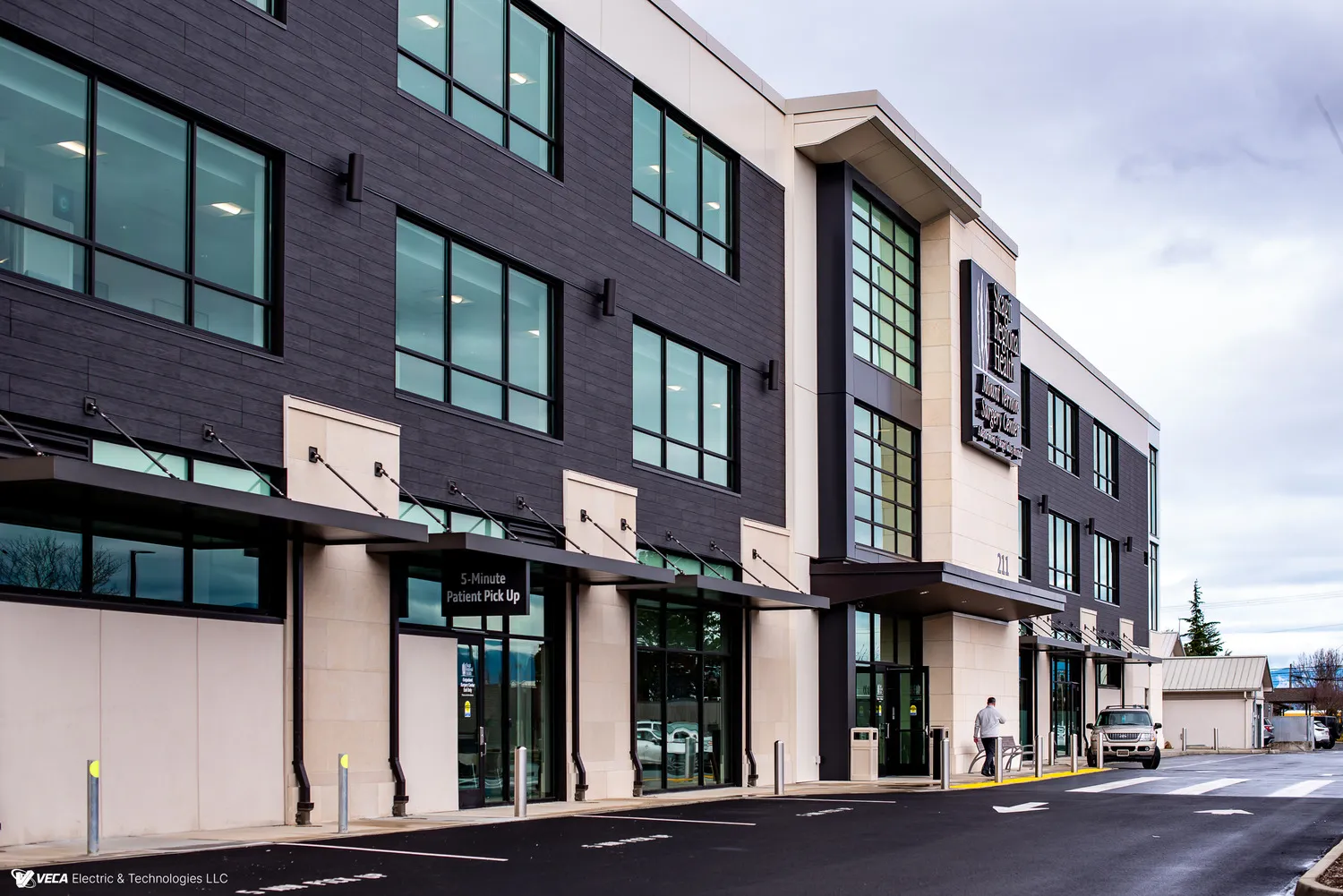
Skagit Outpatient Surgery Center
Healthcare
Skagit Outpatient Surgery Center
Healthcare
Healthcare
Electrical
Fabrication
Seattle
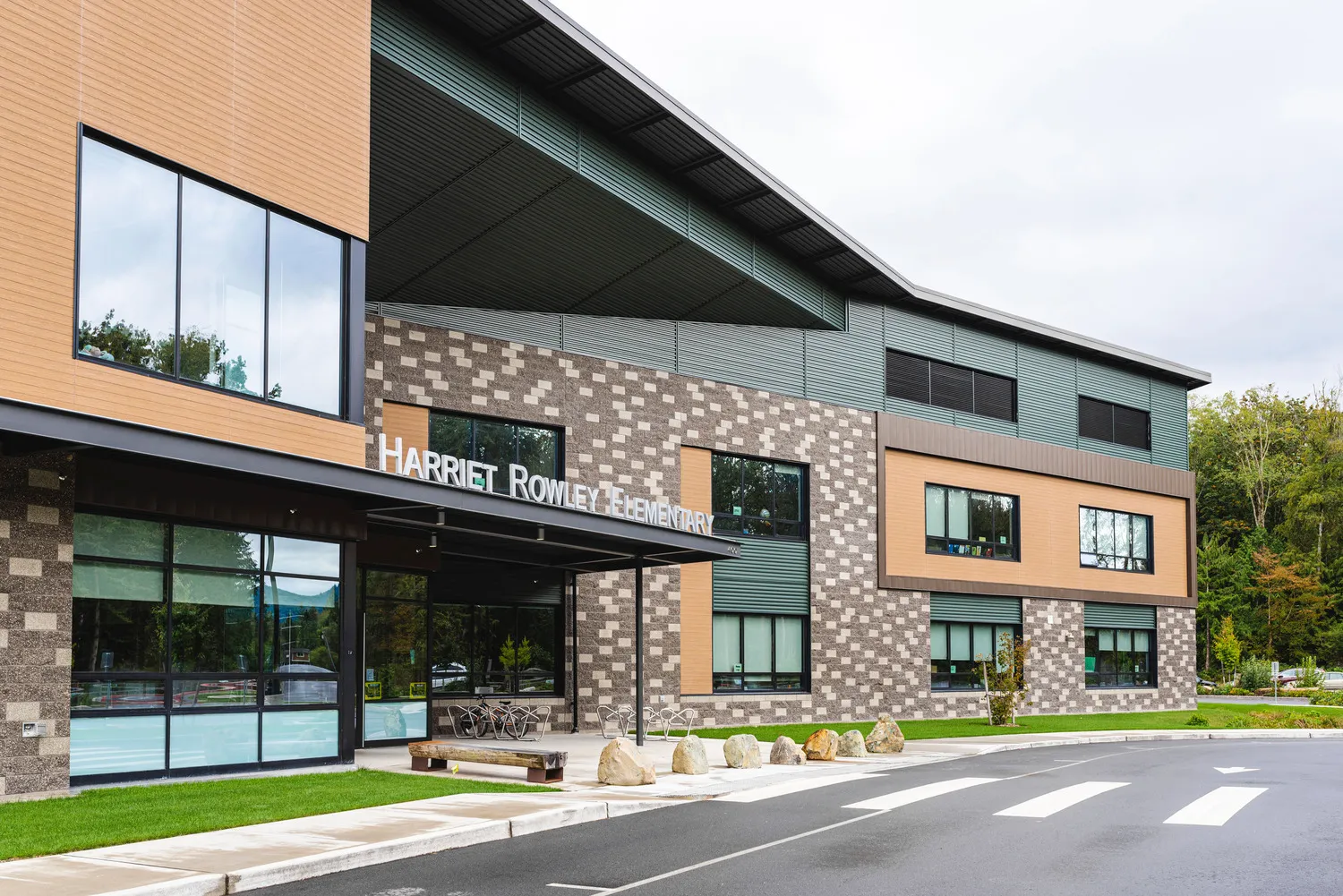
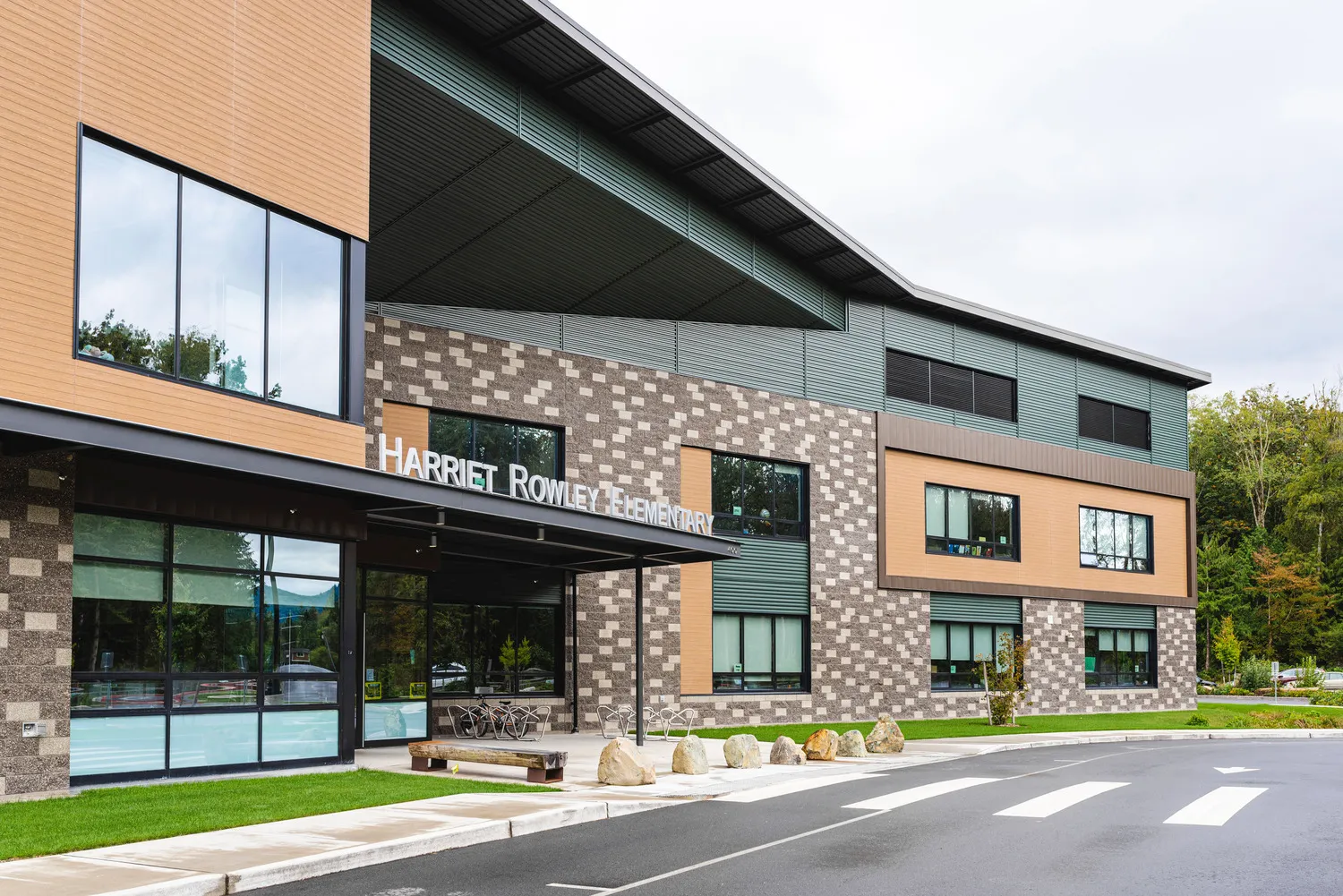
Harriet Rowley Elementary School
Education
Harriet Rowley Elementary School
Education
Education
Electrical
Preconstruction
Bellingham
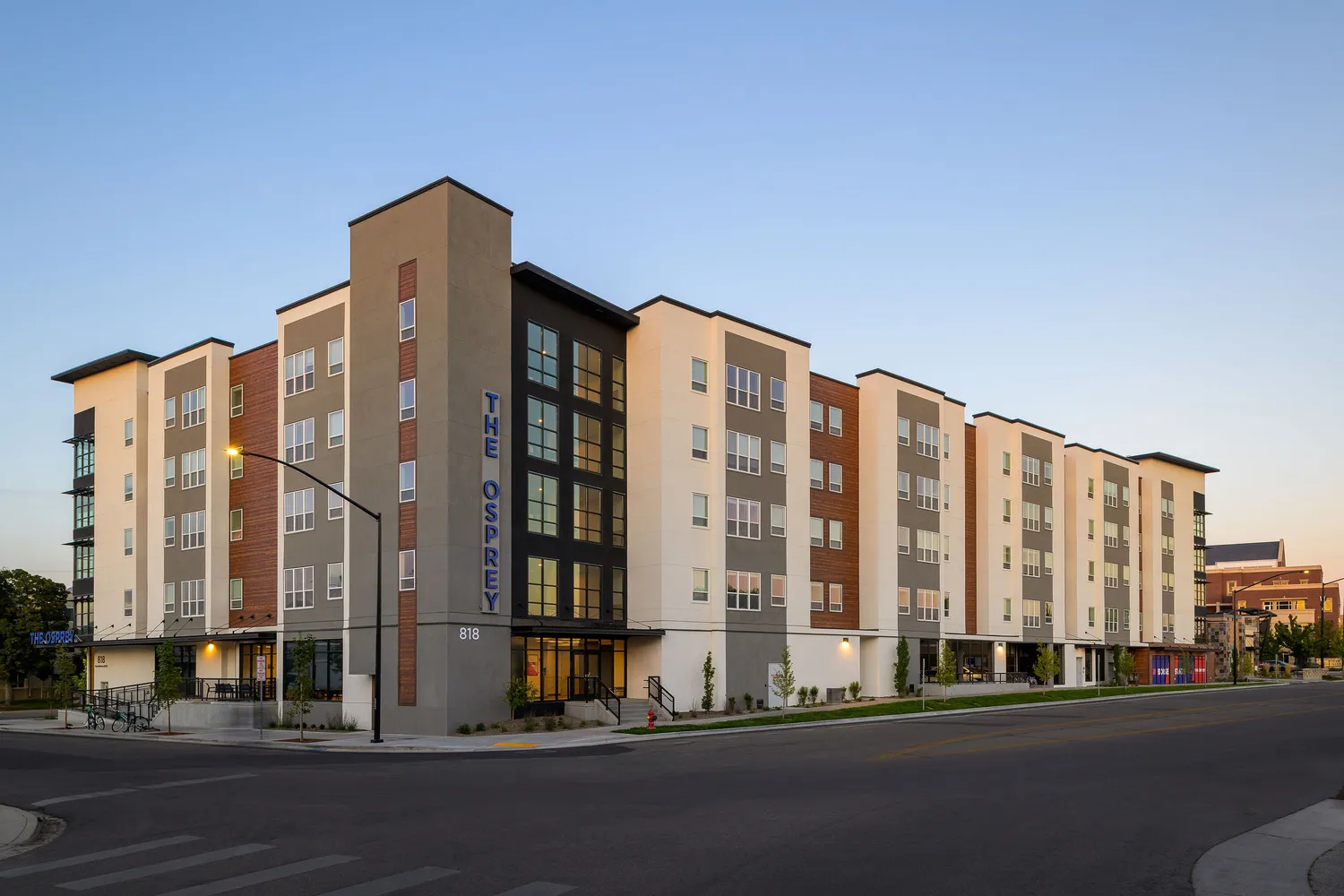
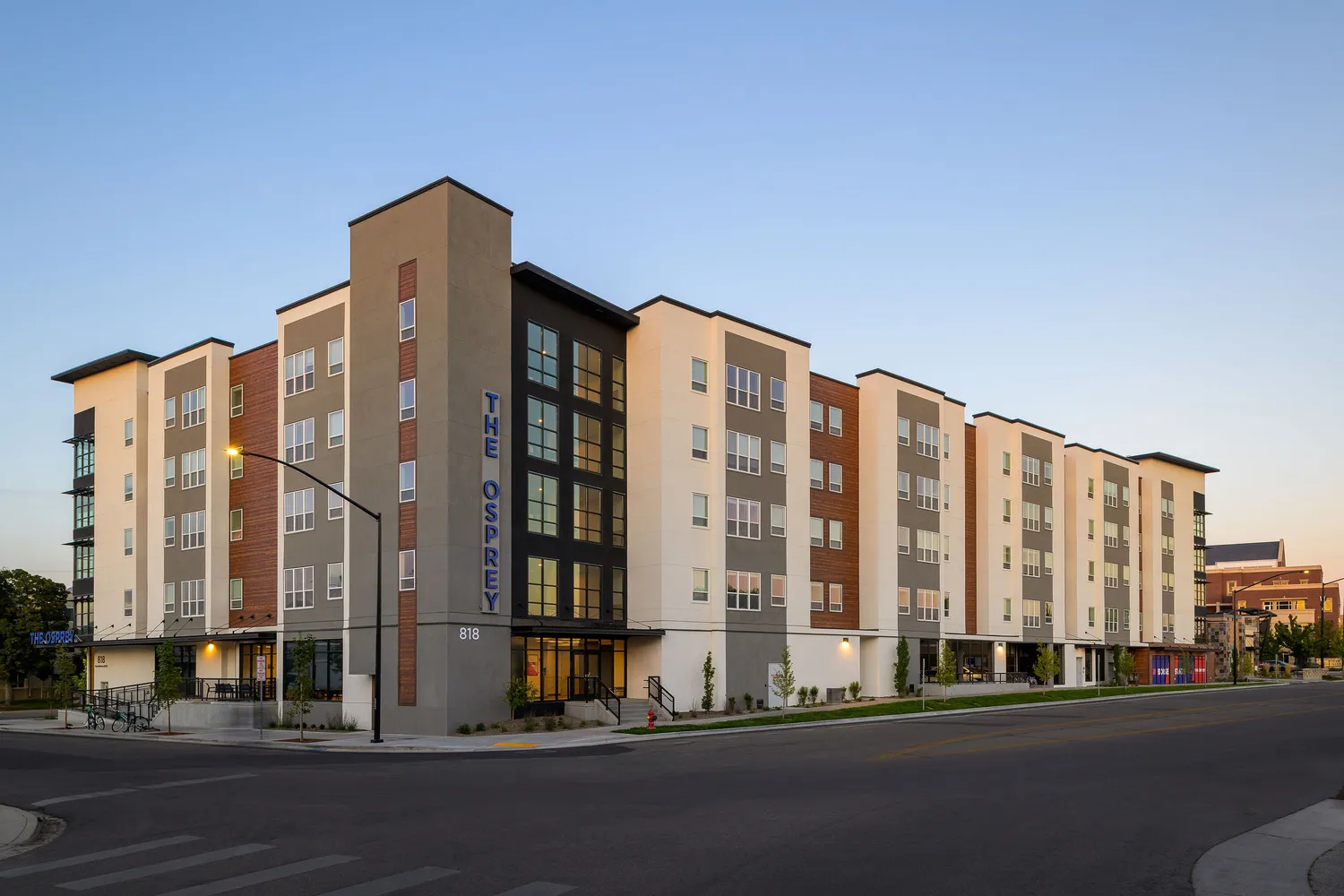
The Osprey Student Housing
Commercial
The Osprey Student Housing
Commercial
Education, Commercial
Electrical
VDC
Boise
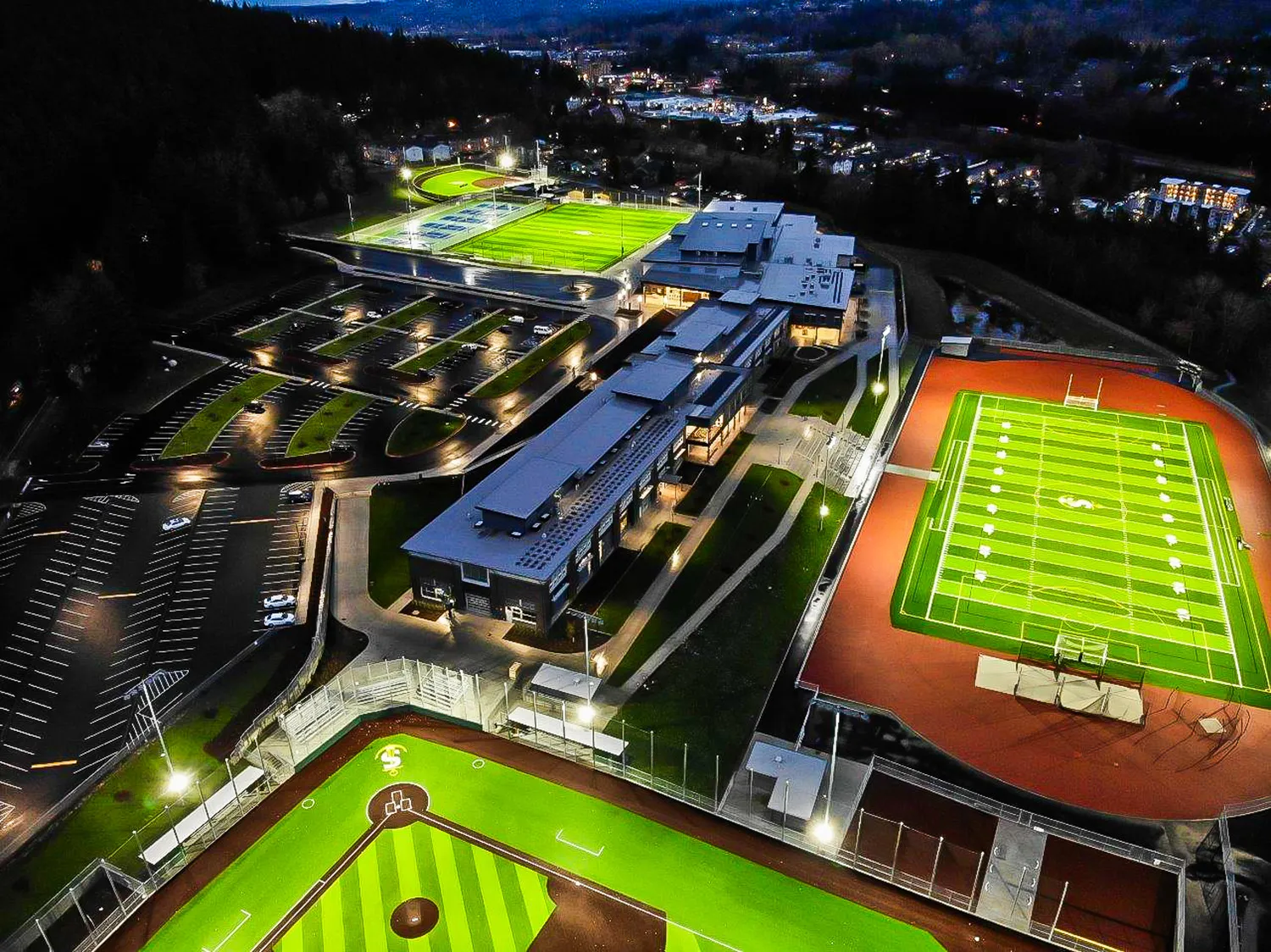
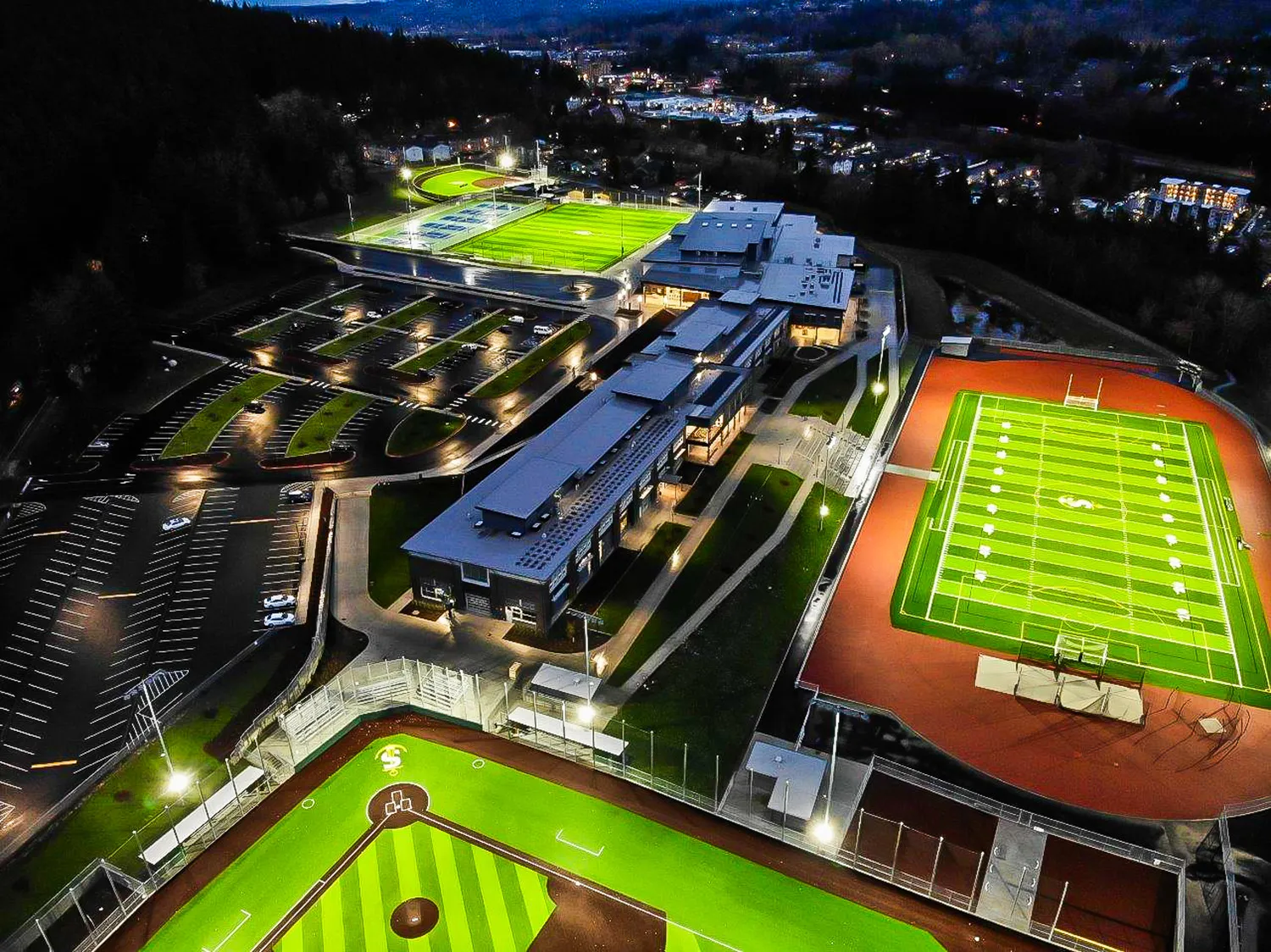
Sehome High School
Education
Sehome High School
Education
Education
Electrical
Preconstruction, VDC, Sustainability
Bellingham
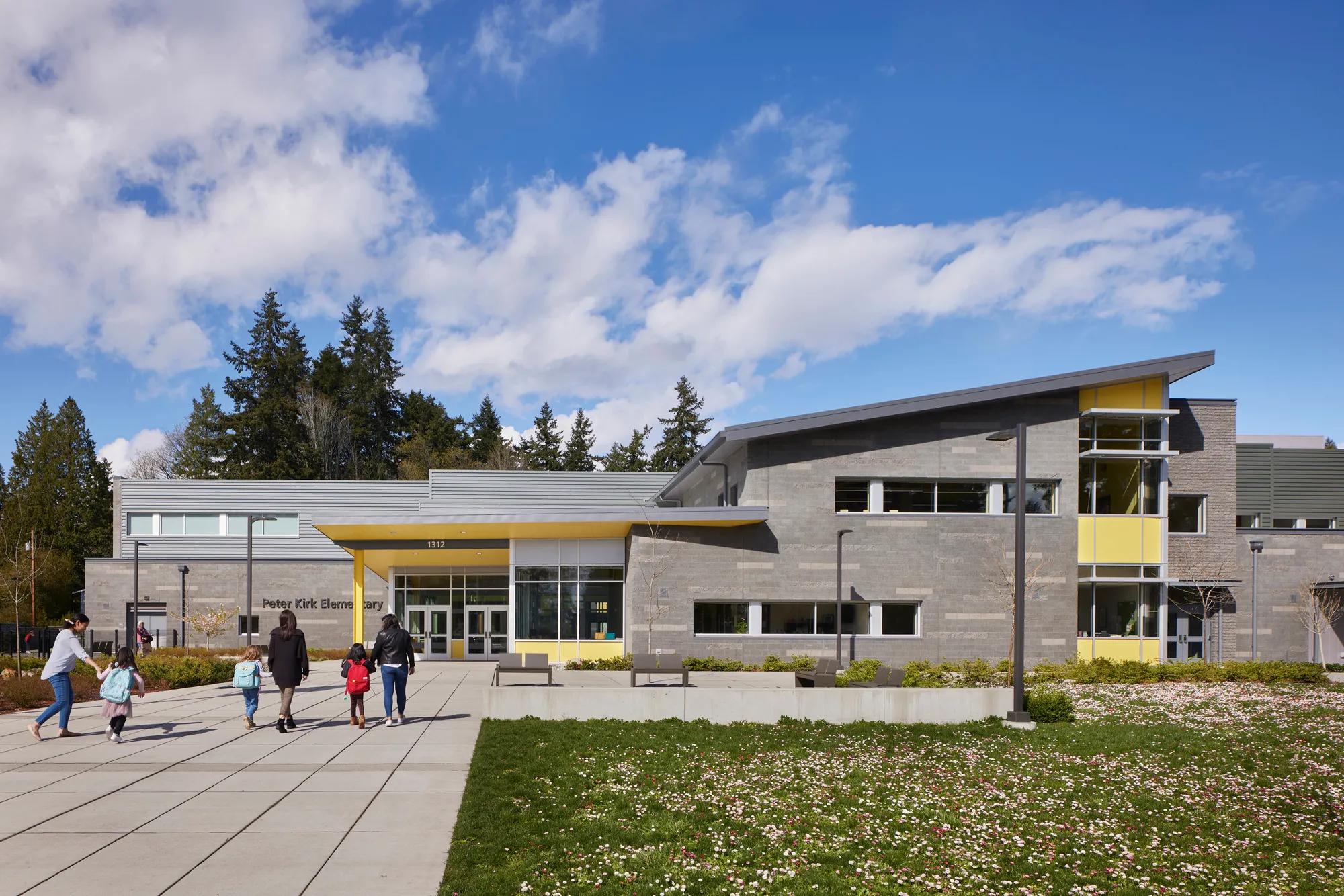
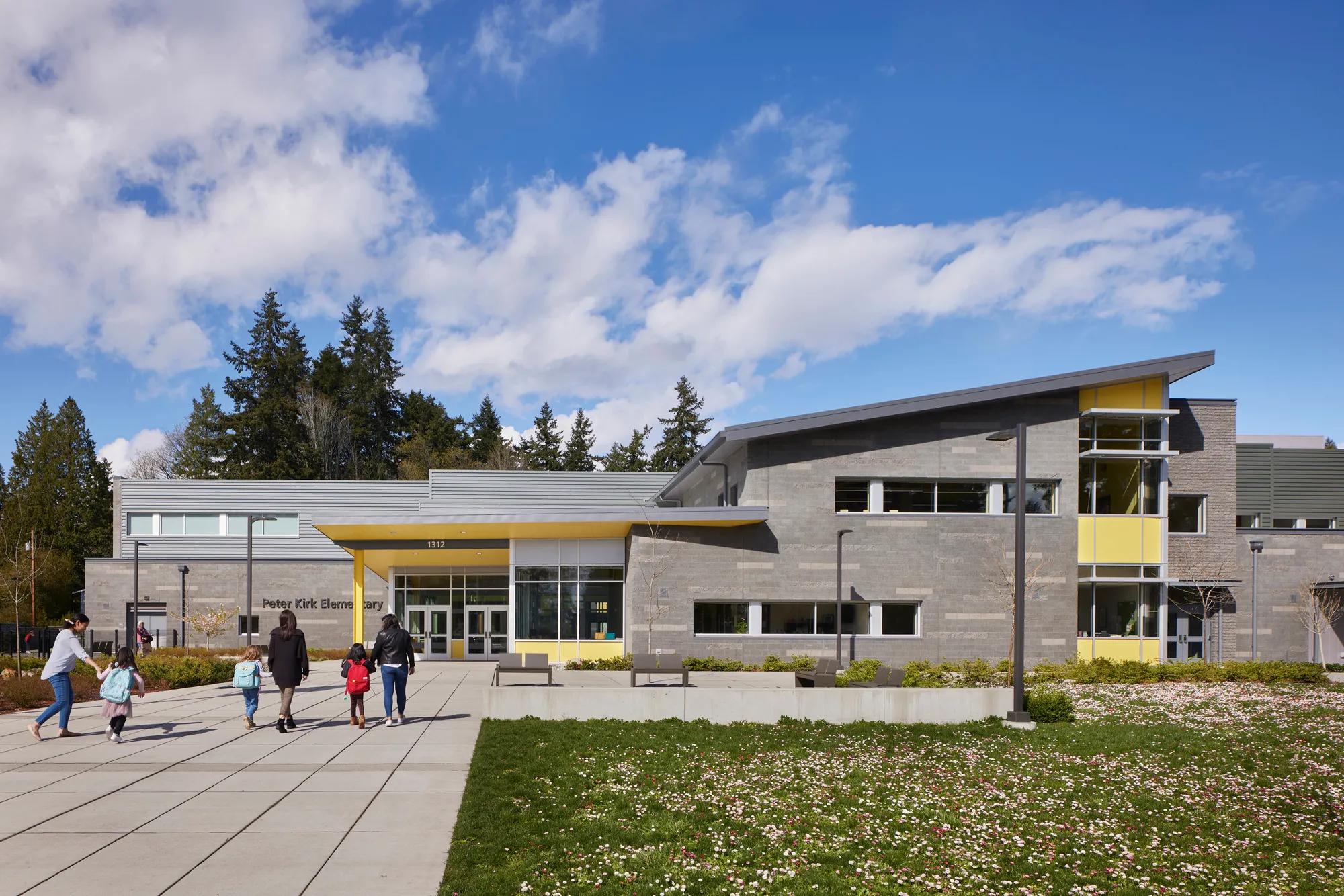
Peter Kirk Elementary School
Education
Peter Kirk Elementary School
Education
Education
Electrical
Preconstruction, VDC, Fabrication
Seattle
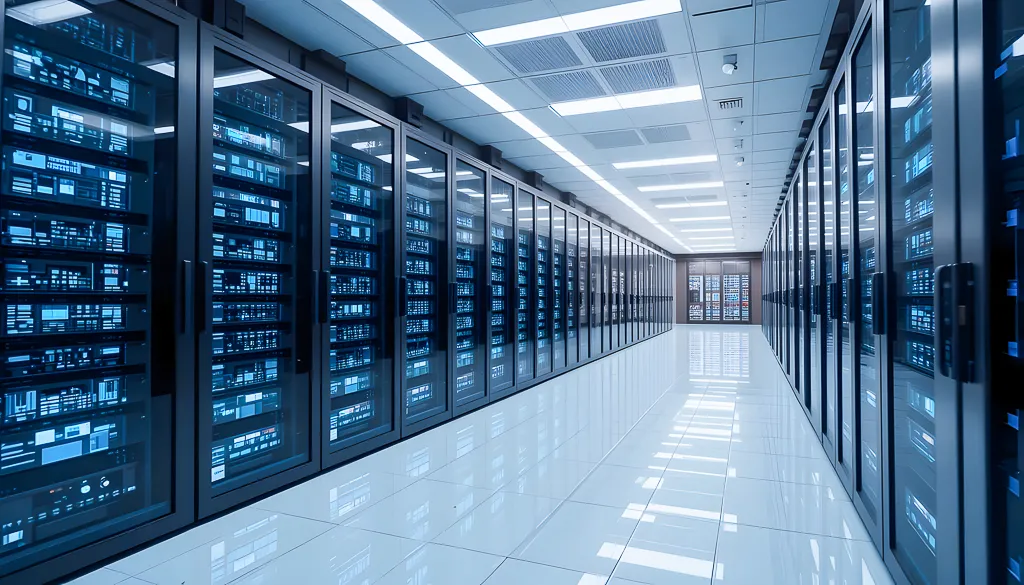
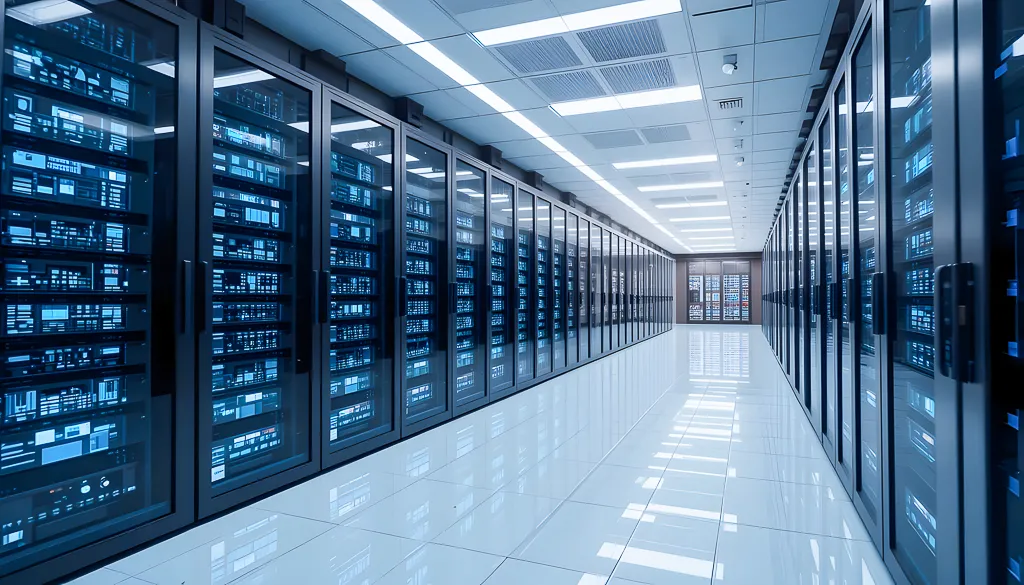
45MW Hyperscale DC - C
Mission Critical
45MW Hyperscale DC - C
Mission Critical
Mission Critical
Electrical
Wenatchee
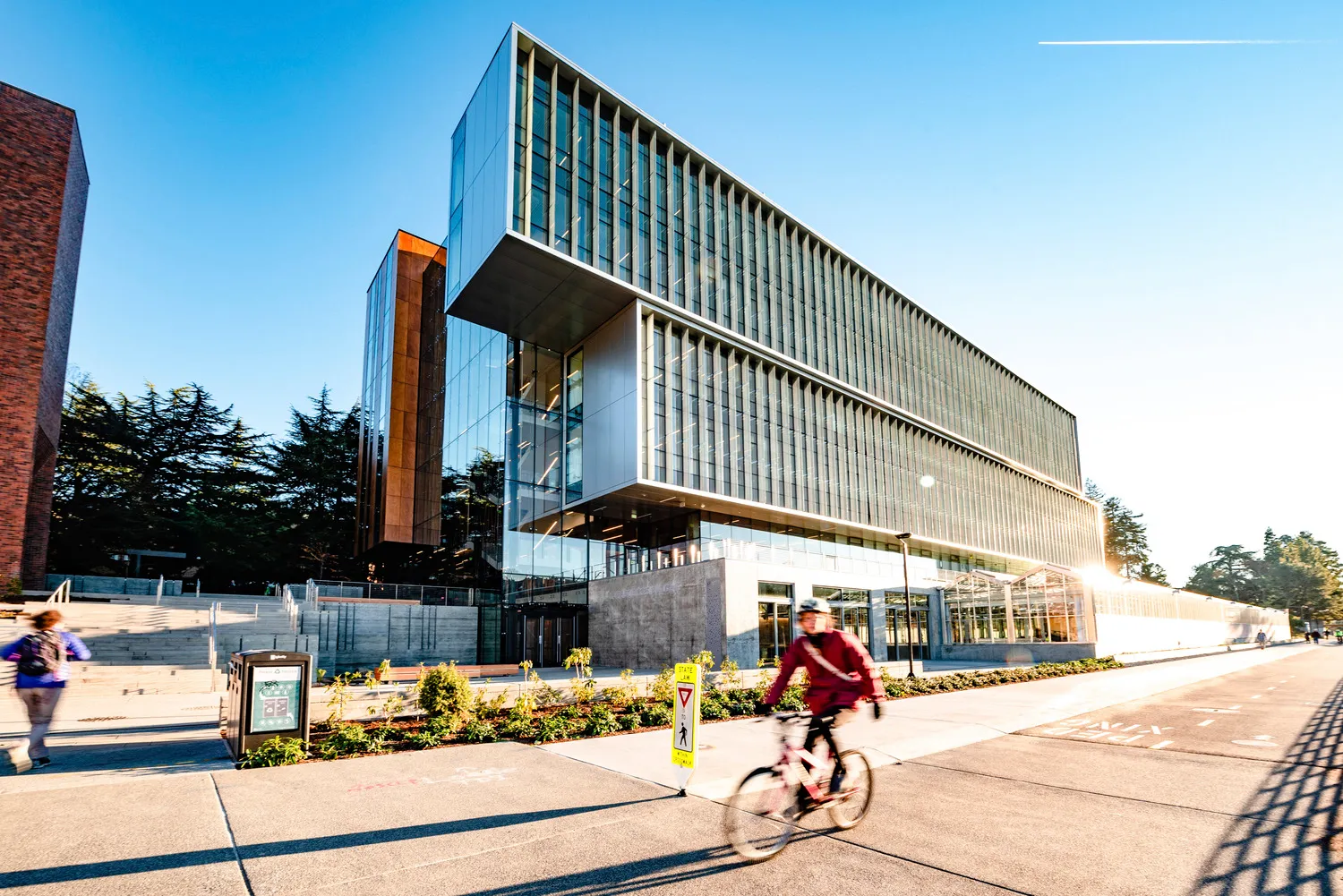
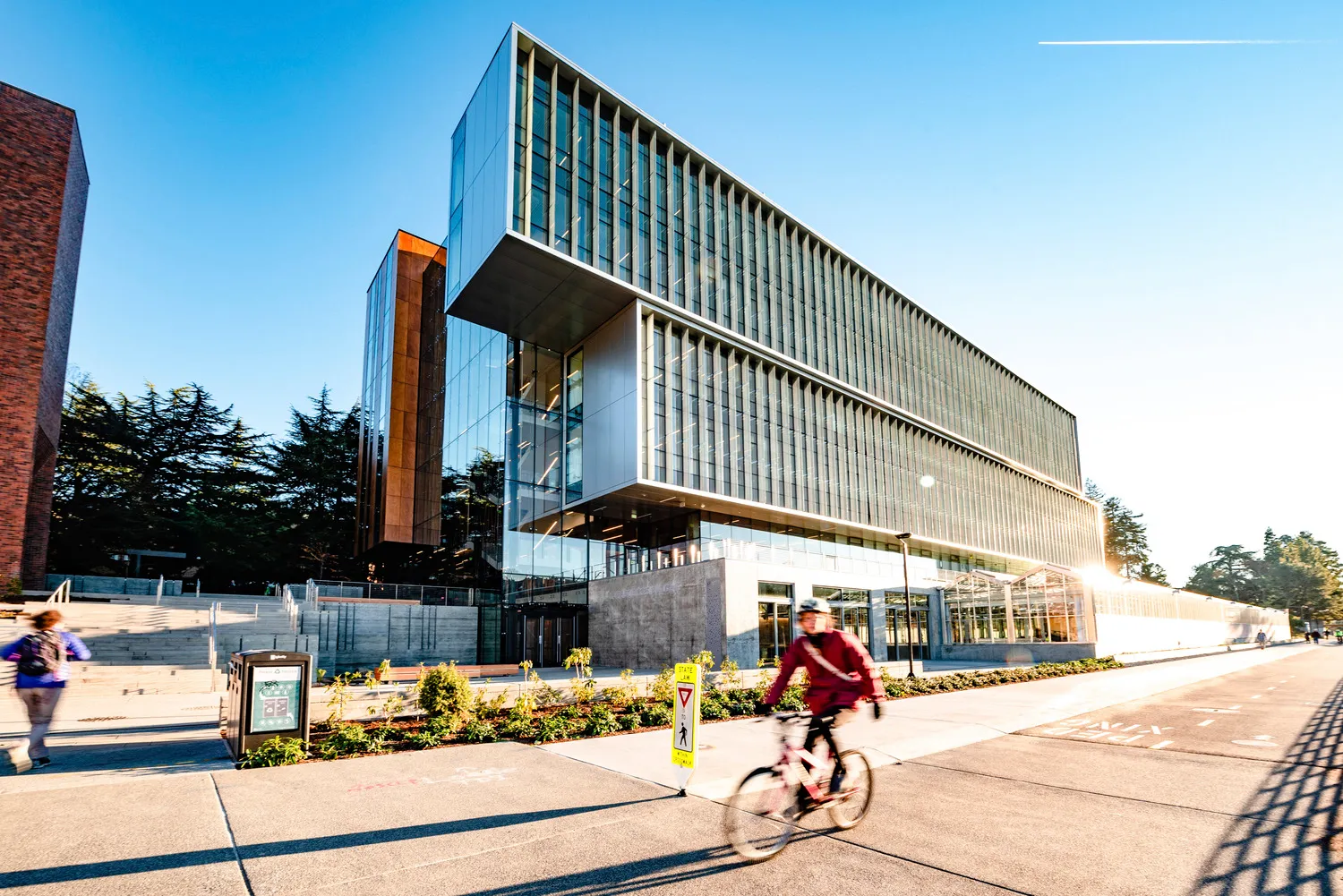
UW - Life Sciences Building
Life Sciences
UW - Life Sciences Building
Life Sciences
Life Sciences, Education
Electrical, Technologies
Diversity, VDC, Preconstruction, Sustainability
Seattle
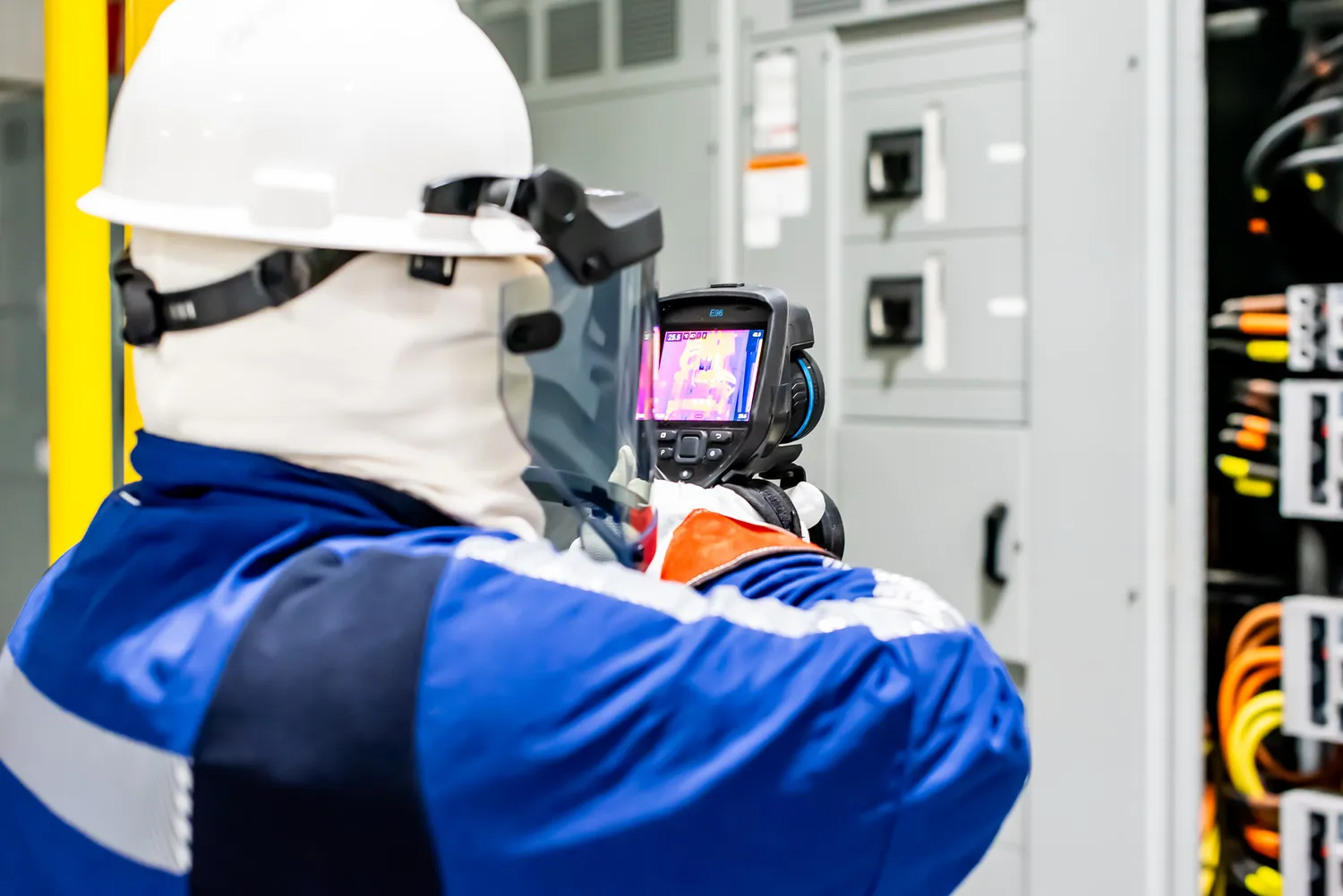
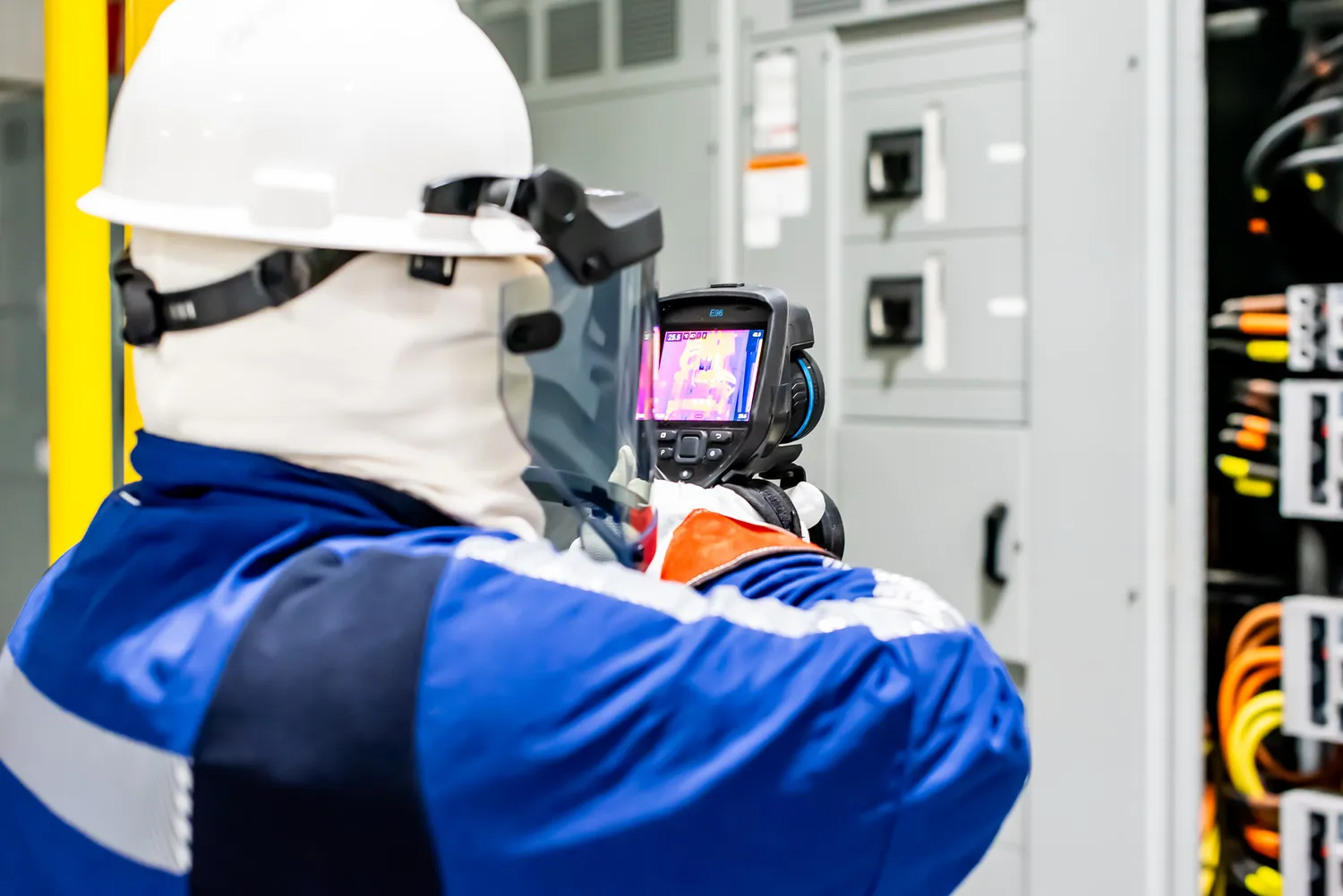
Service & Maintenance Project Capabilities
Service & Maintenance Project Capabilities
Education, Healthcare, Transportation Infrastructure, Commercial, Life Sciences
Service & Maintenance
Sustainability, Preconstruction, EV Solutions
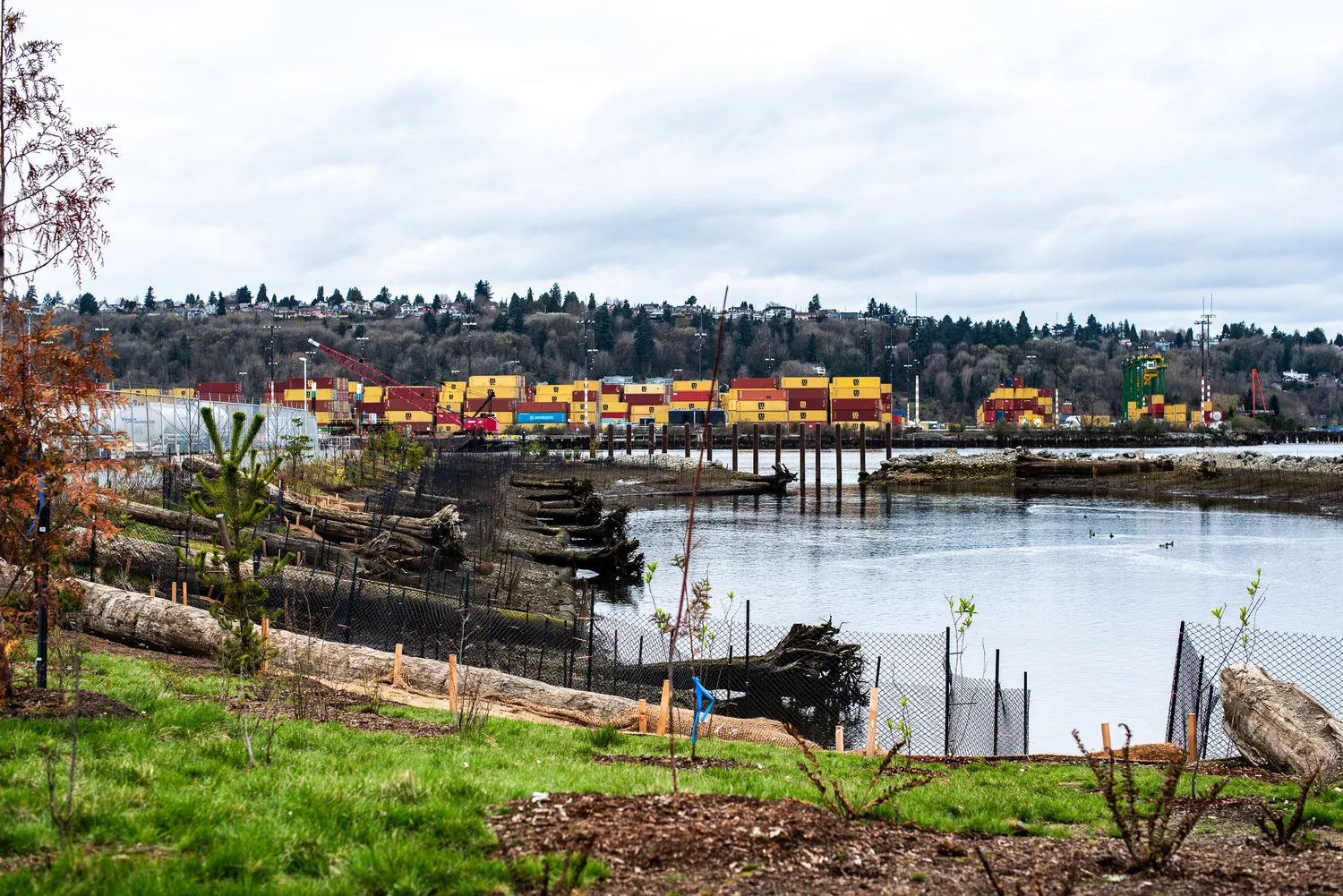
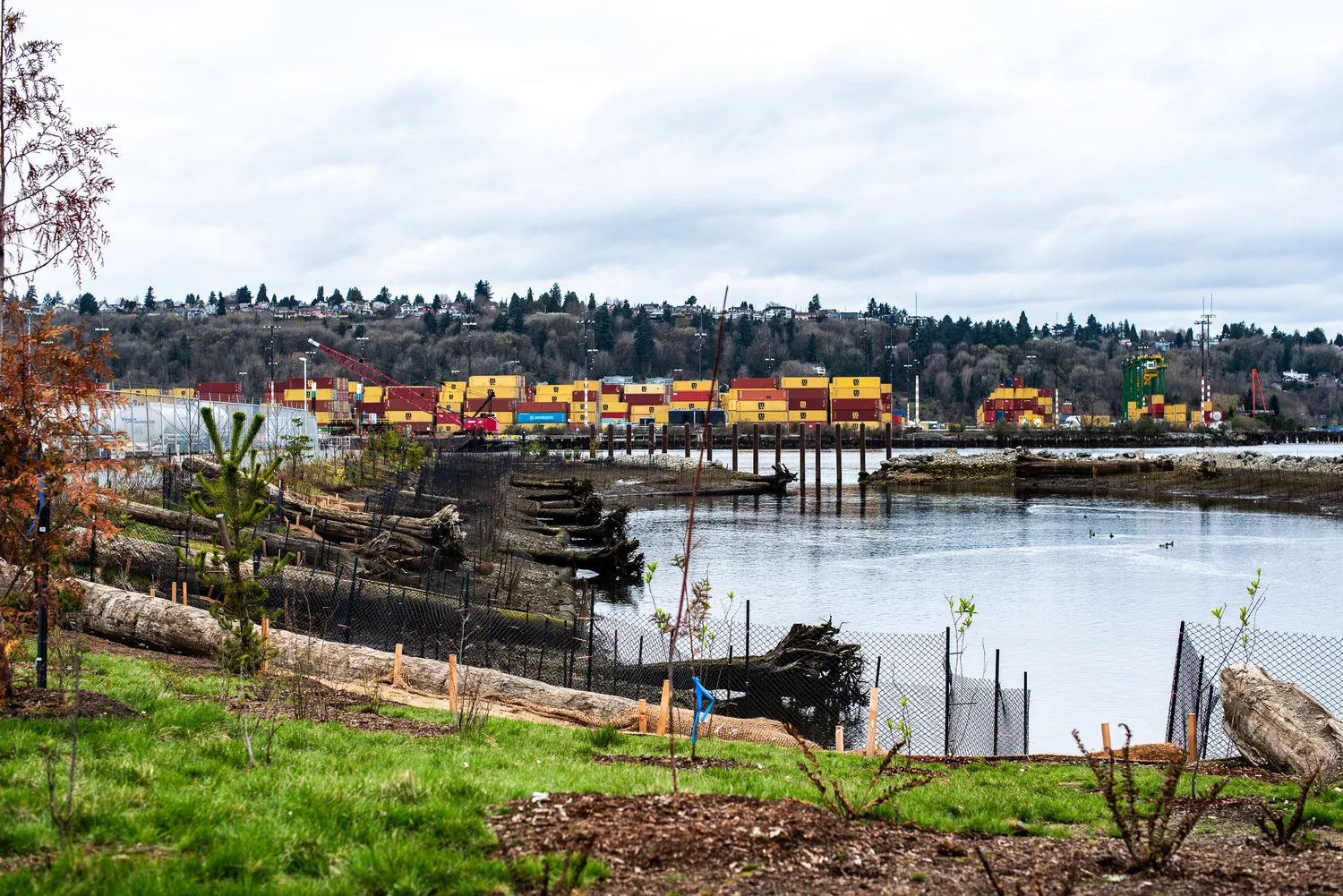
Harbor Island Southwest Yard Habitat Restoration
Industrial & Manufacturing
Harbor Island Southwest Yard Habitat Restoration
Industrial & Manufacturing
Industrial & Manufacturing
Electrical
Sustainability
Seattle
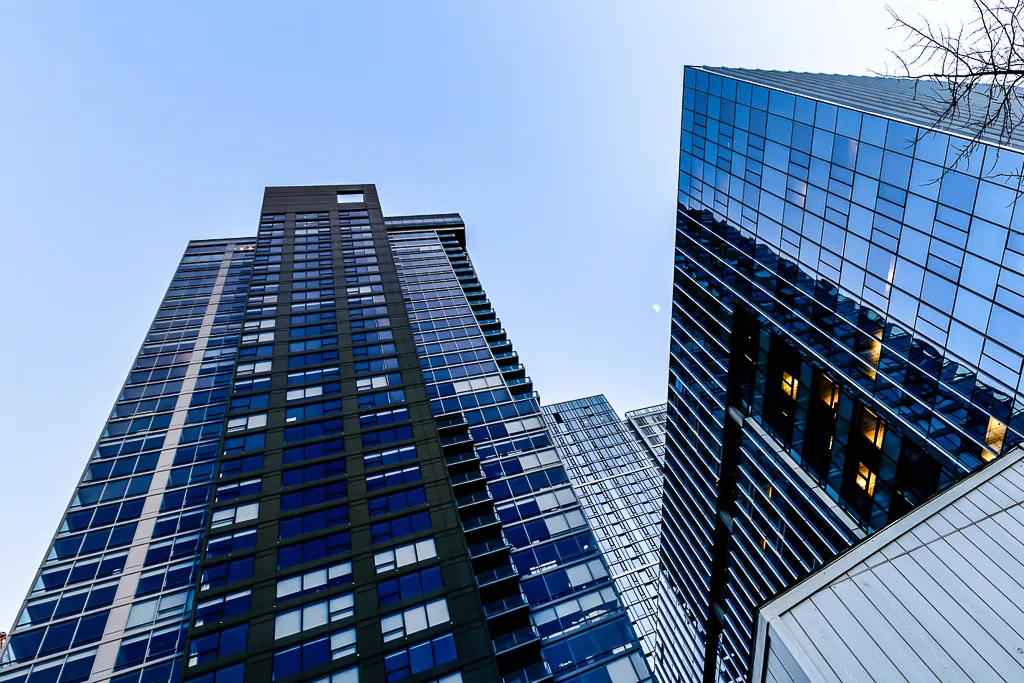
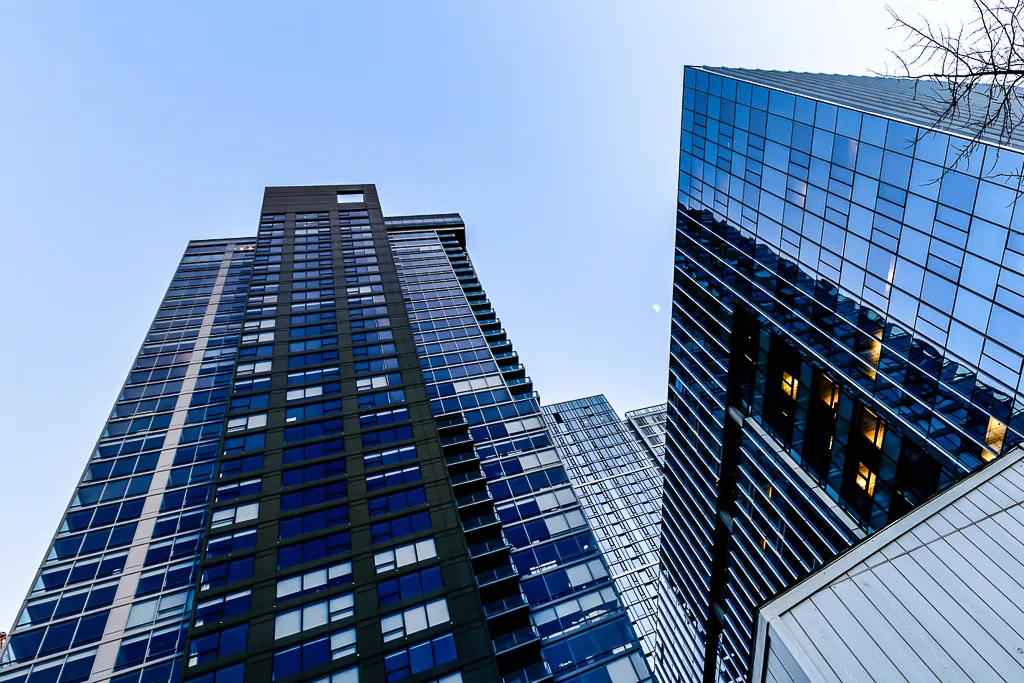
Kinects Tower
Commercial
Kinects Tower
Commercial
Commercial
Electrical
Preconstruction, Sustainability, VDC
Seattle
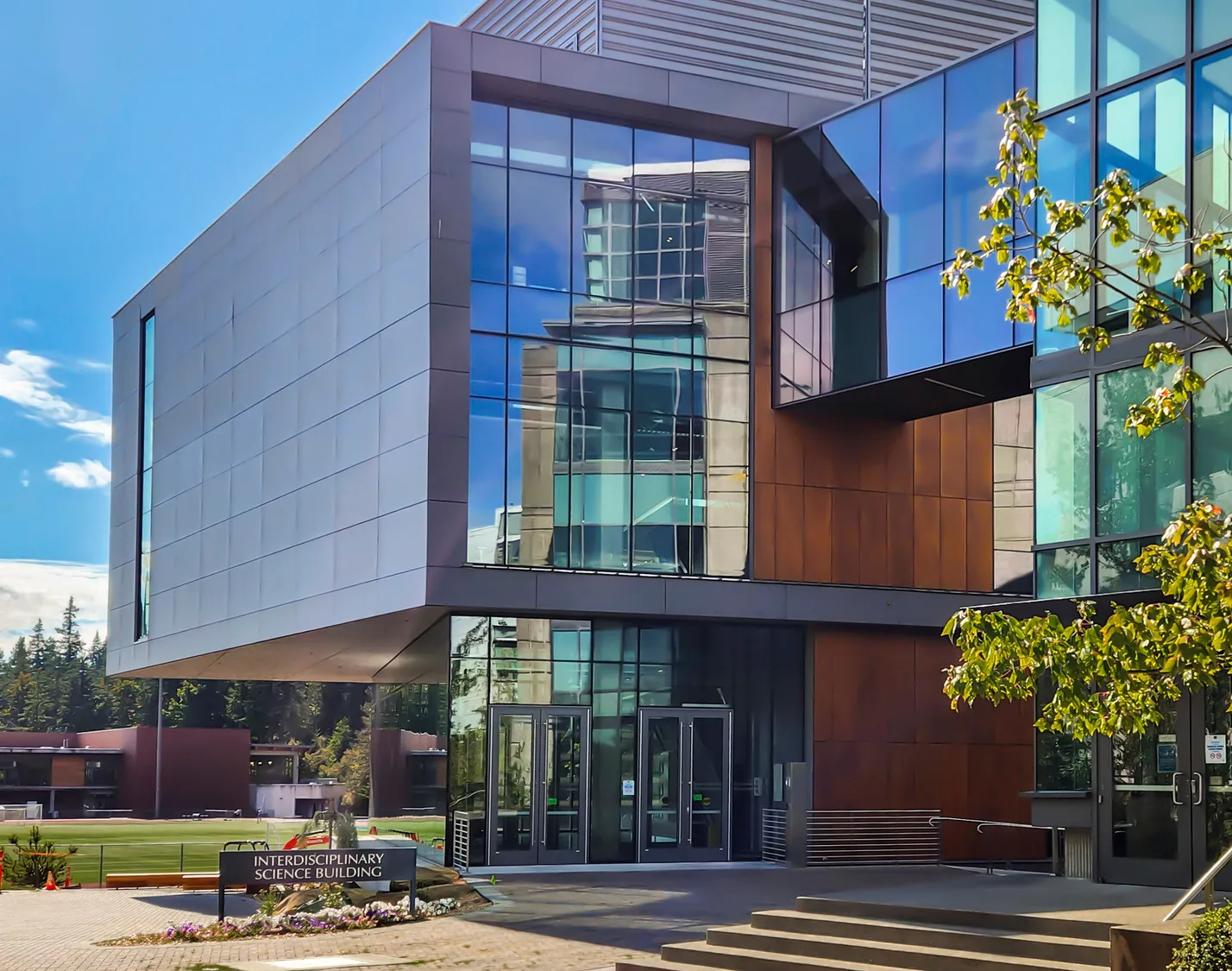
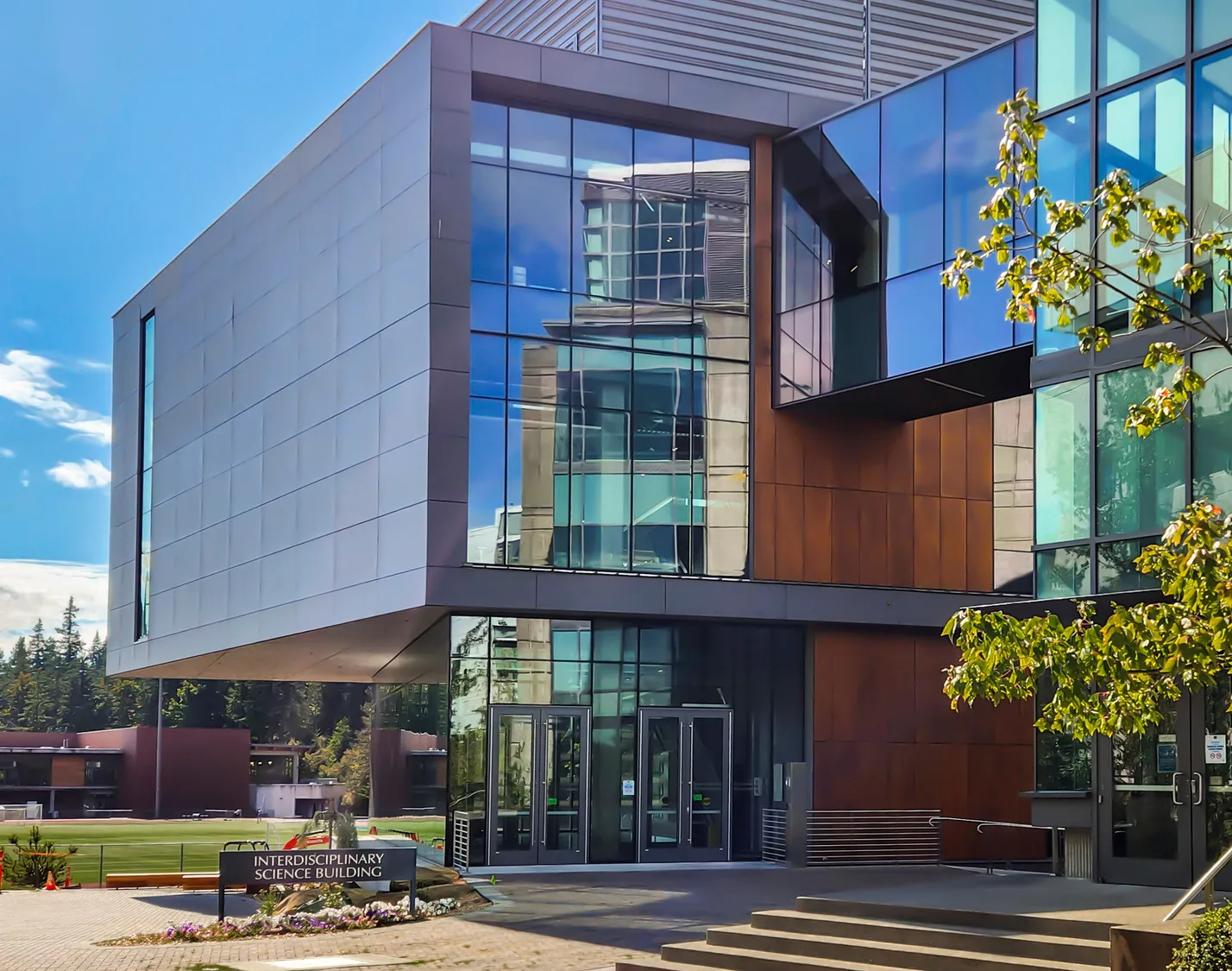
WWU - Interdisciplinary Science Building
Life Sciences
WWU - Interdisciplinary Science Building
Life Sciences
Life Sciences, Education
Electrical
VDC, Preconstruction, Sustainability
Bellingham
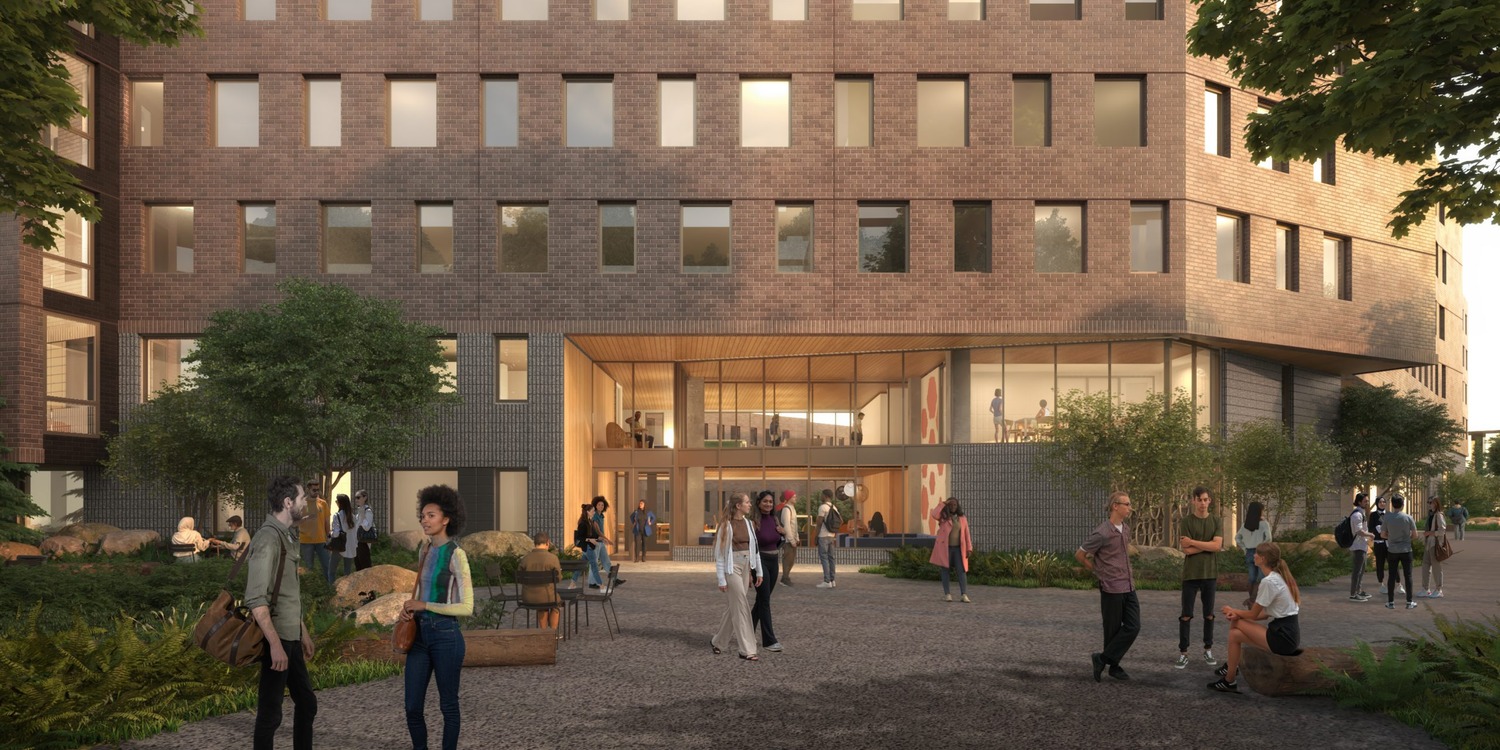
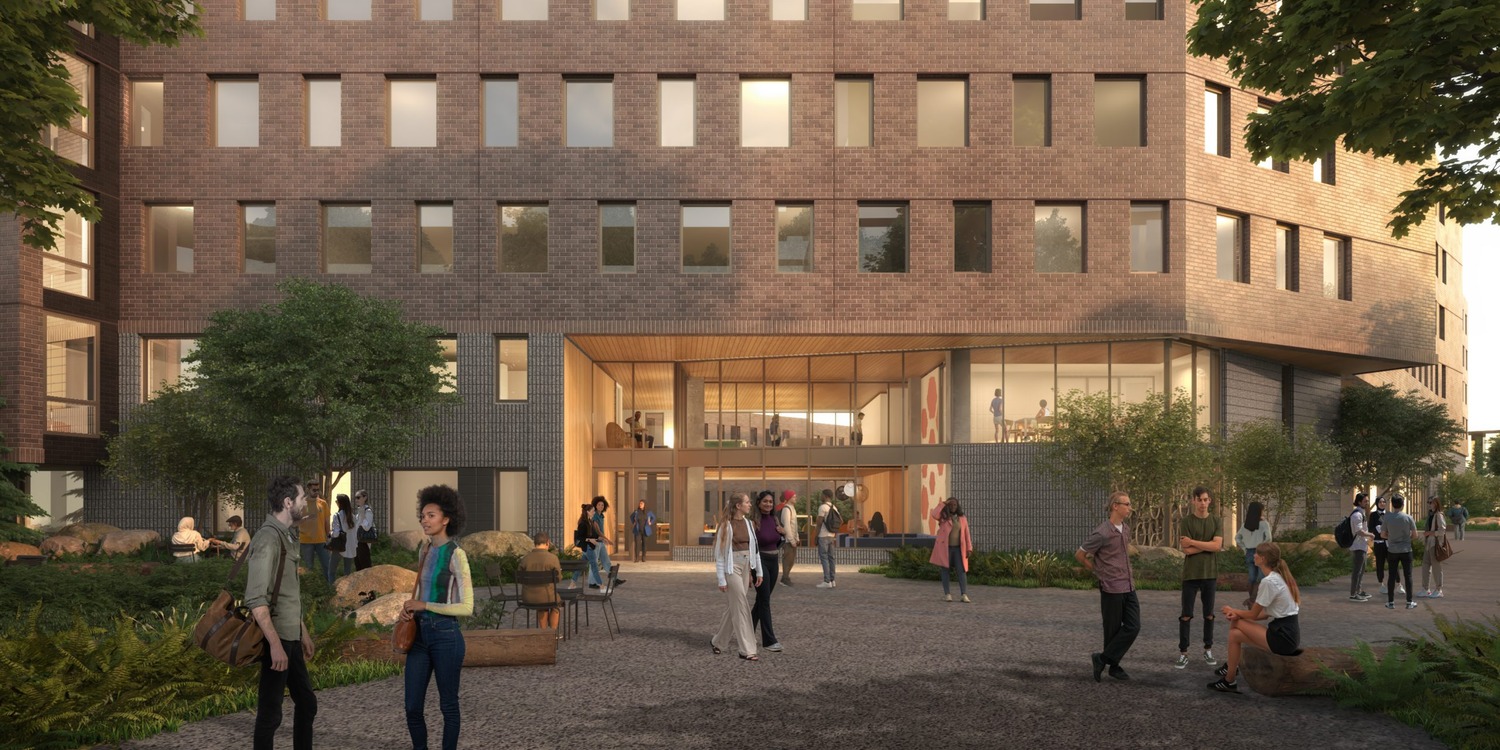
UW - Haggett Hall Demolition and Replacement
Education
UW - Haggett Hall Demolition and Replacement
Education
Education, Commercial
Electrical
preconstruction, sustainability, VDC, fabrication
Seattle
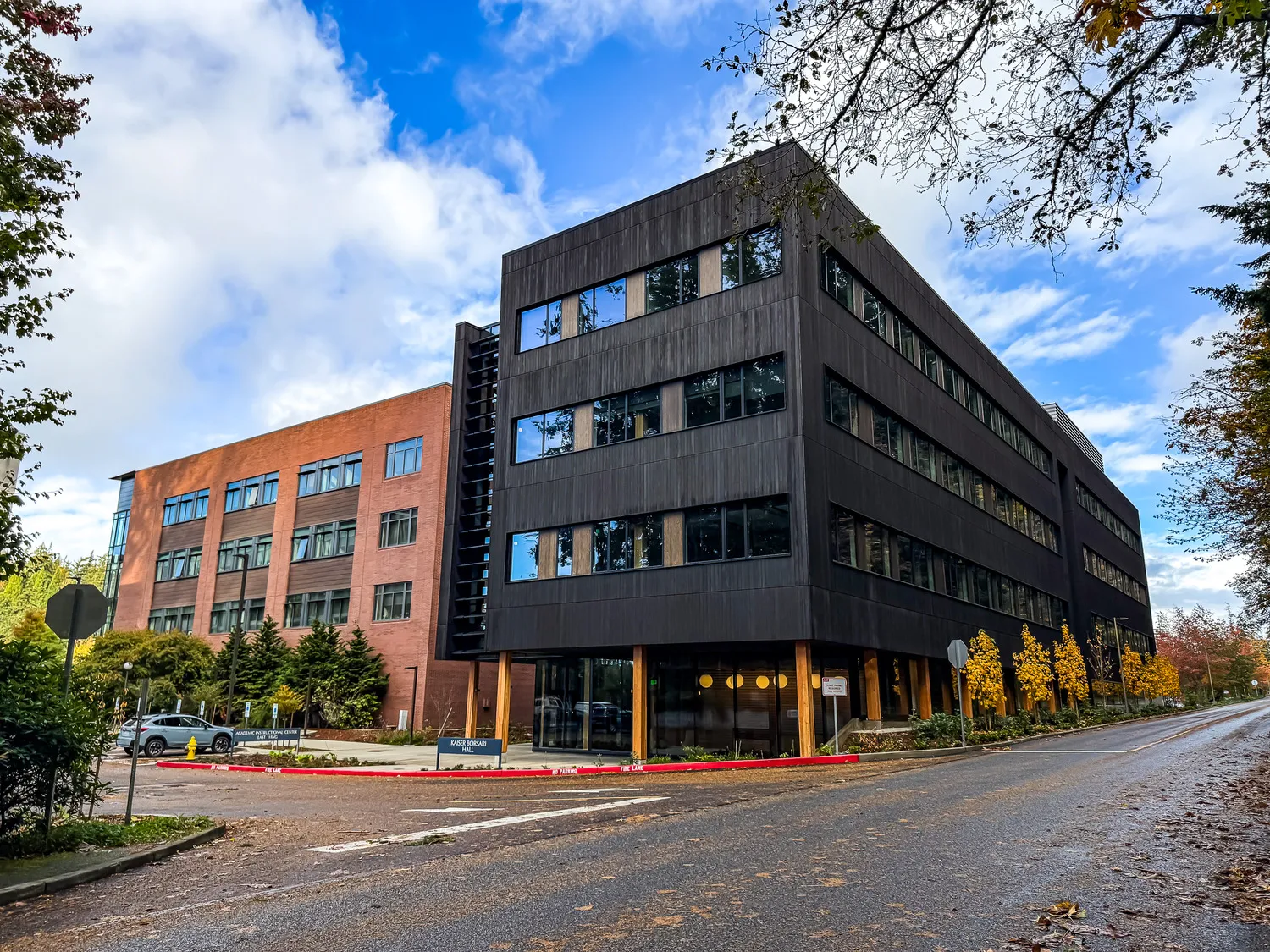
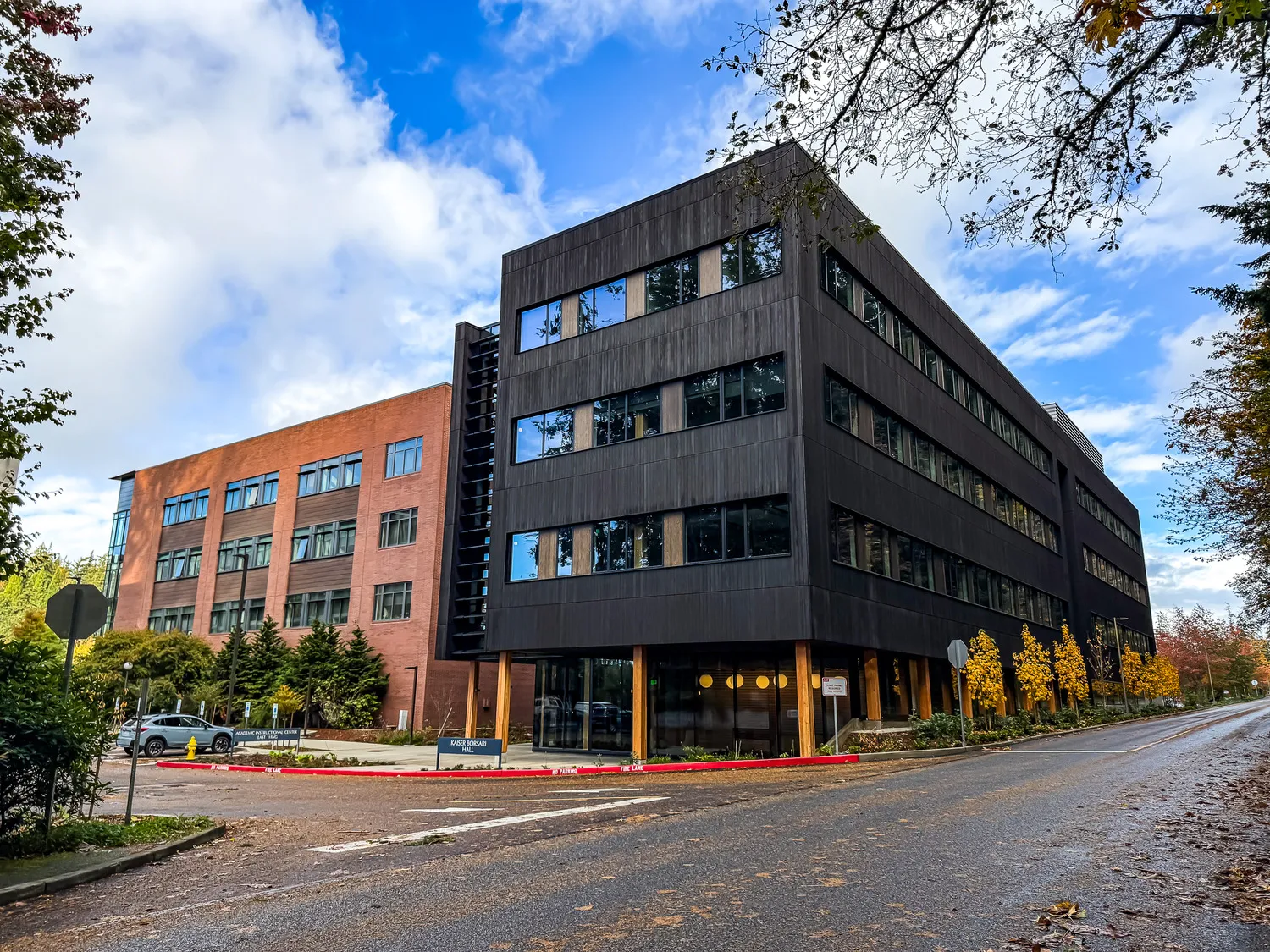
WWU - Kaiser Borsari Hall
Education
WWU - Kaiser Borsari Hall
Education
Education
Electrical
Fabrication, Sustainability, Technologies, EV Solutions, Preconstruction
Bellingham
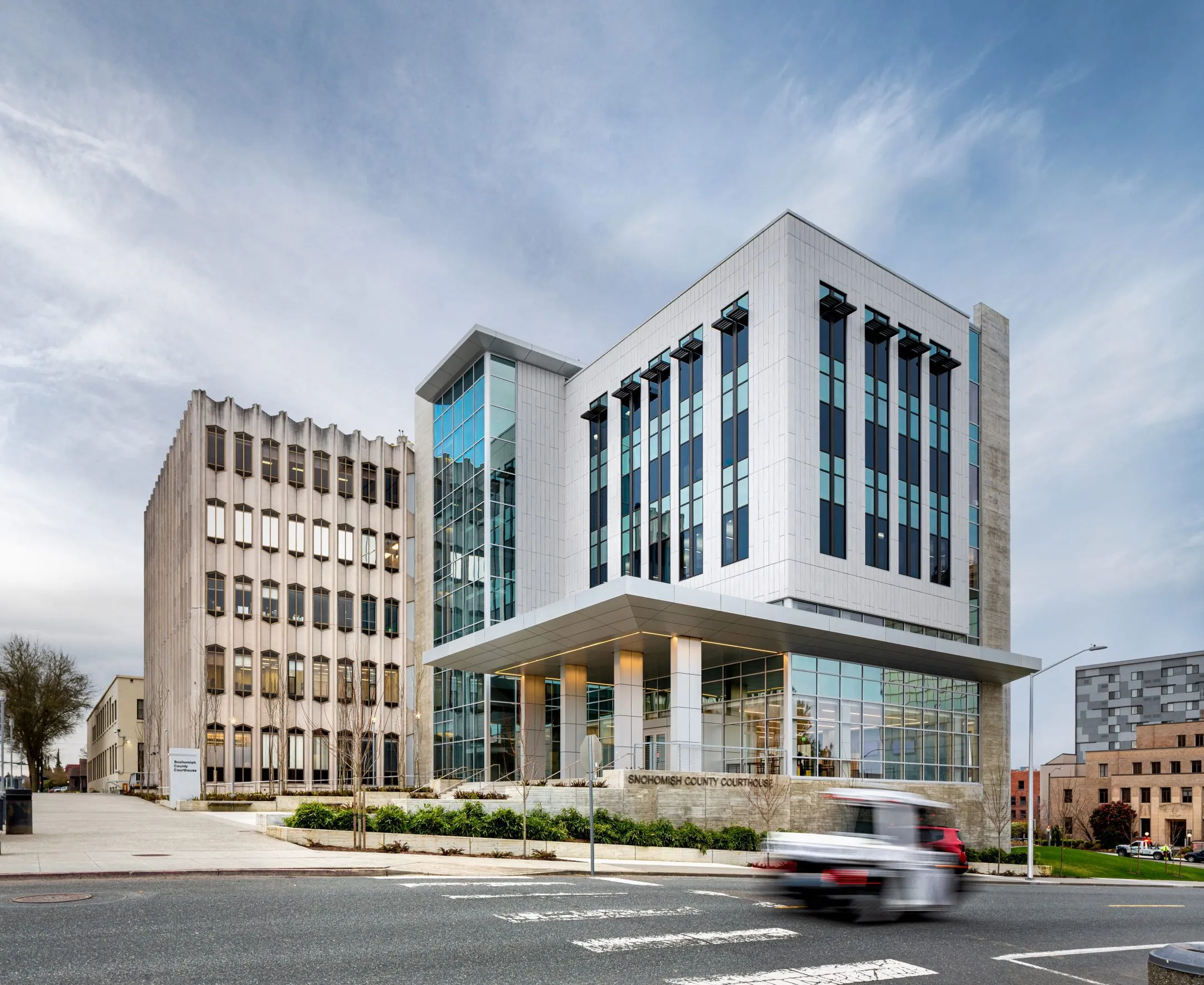
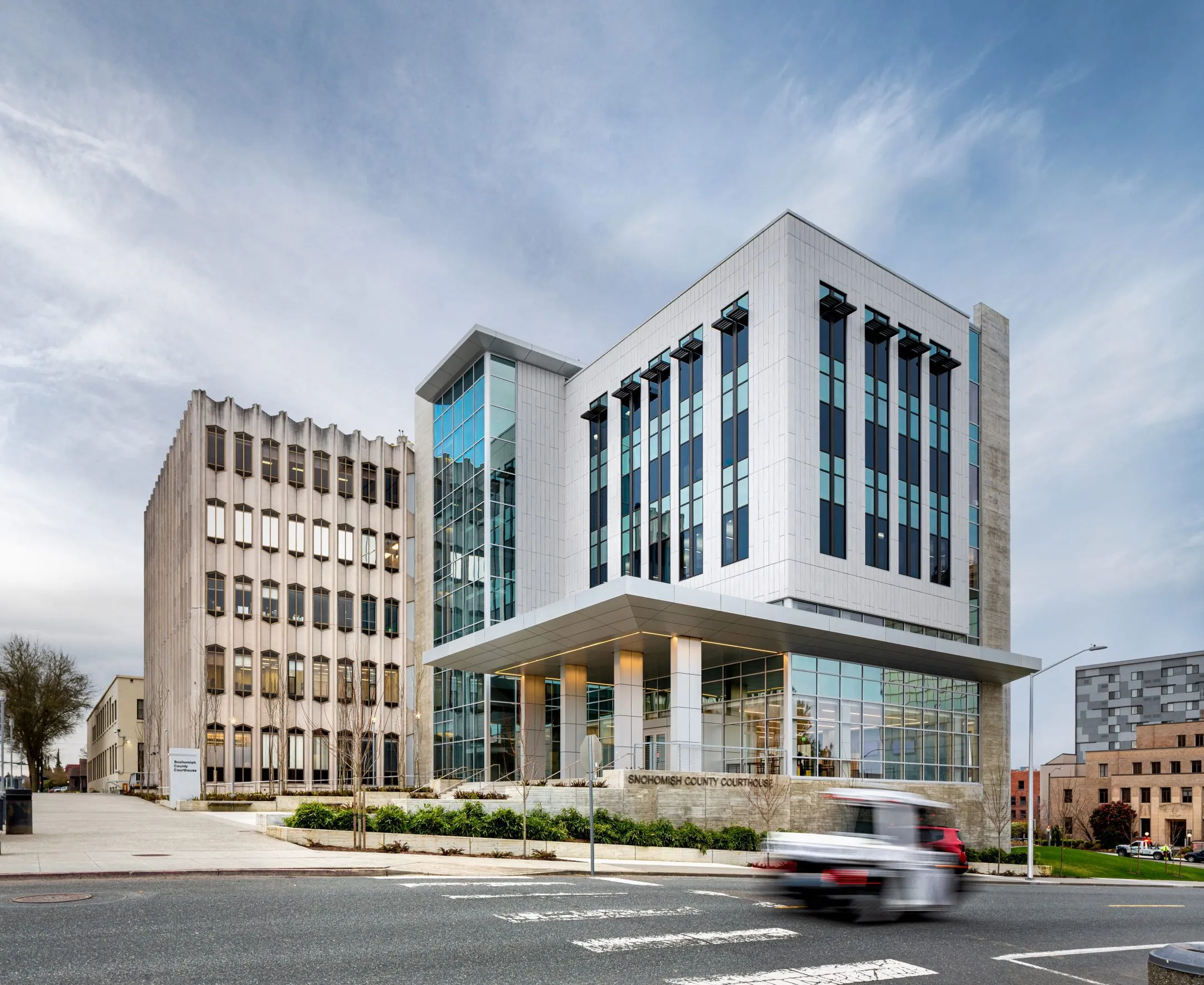
Snohomish County Courthouse
Government
Snohomish County Courthouse
Government
Government
Electrical
VDC, Sustainability, Preconstruction
Bellingham
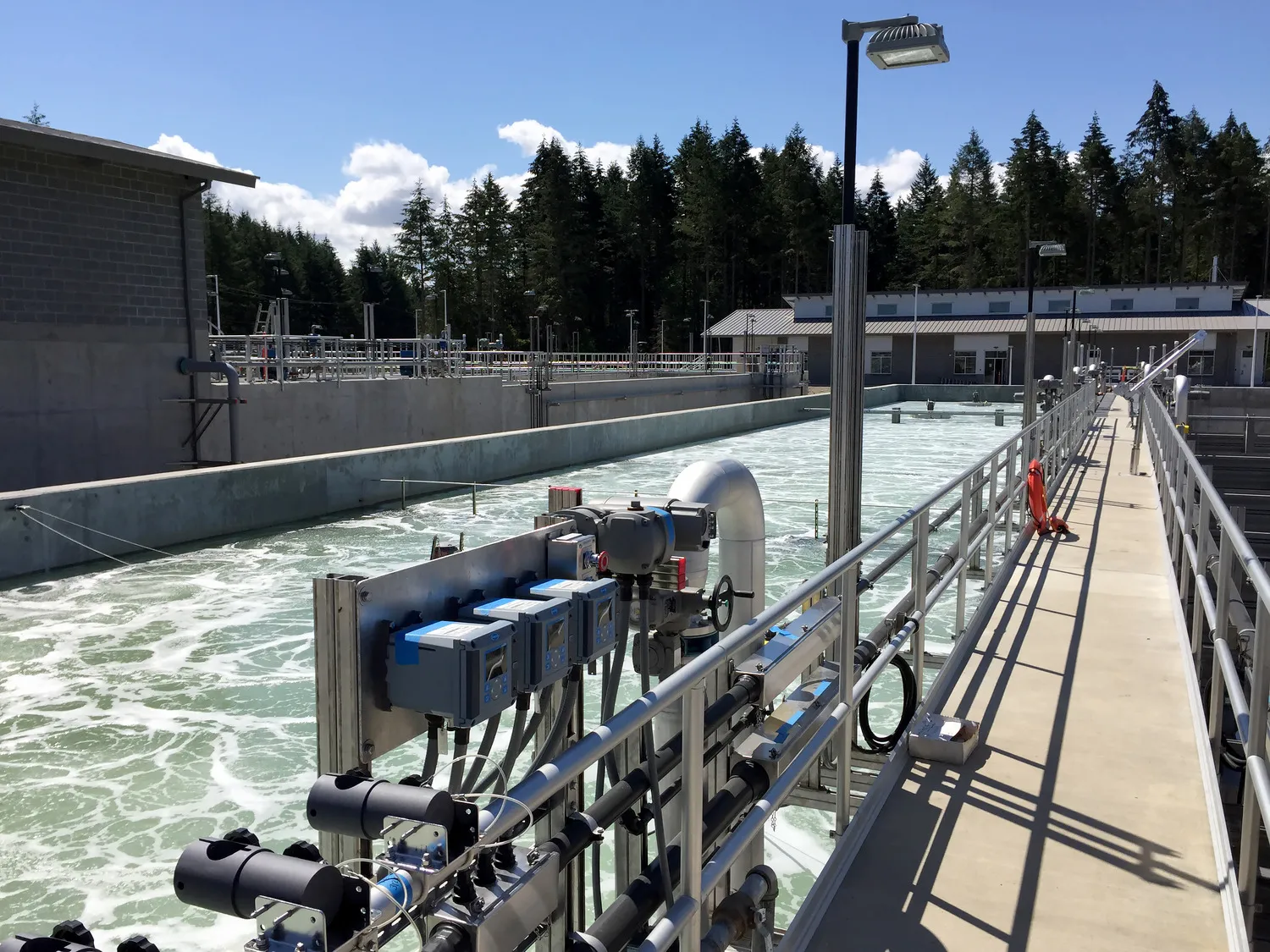
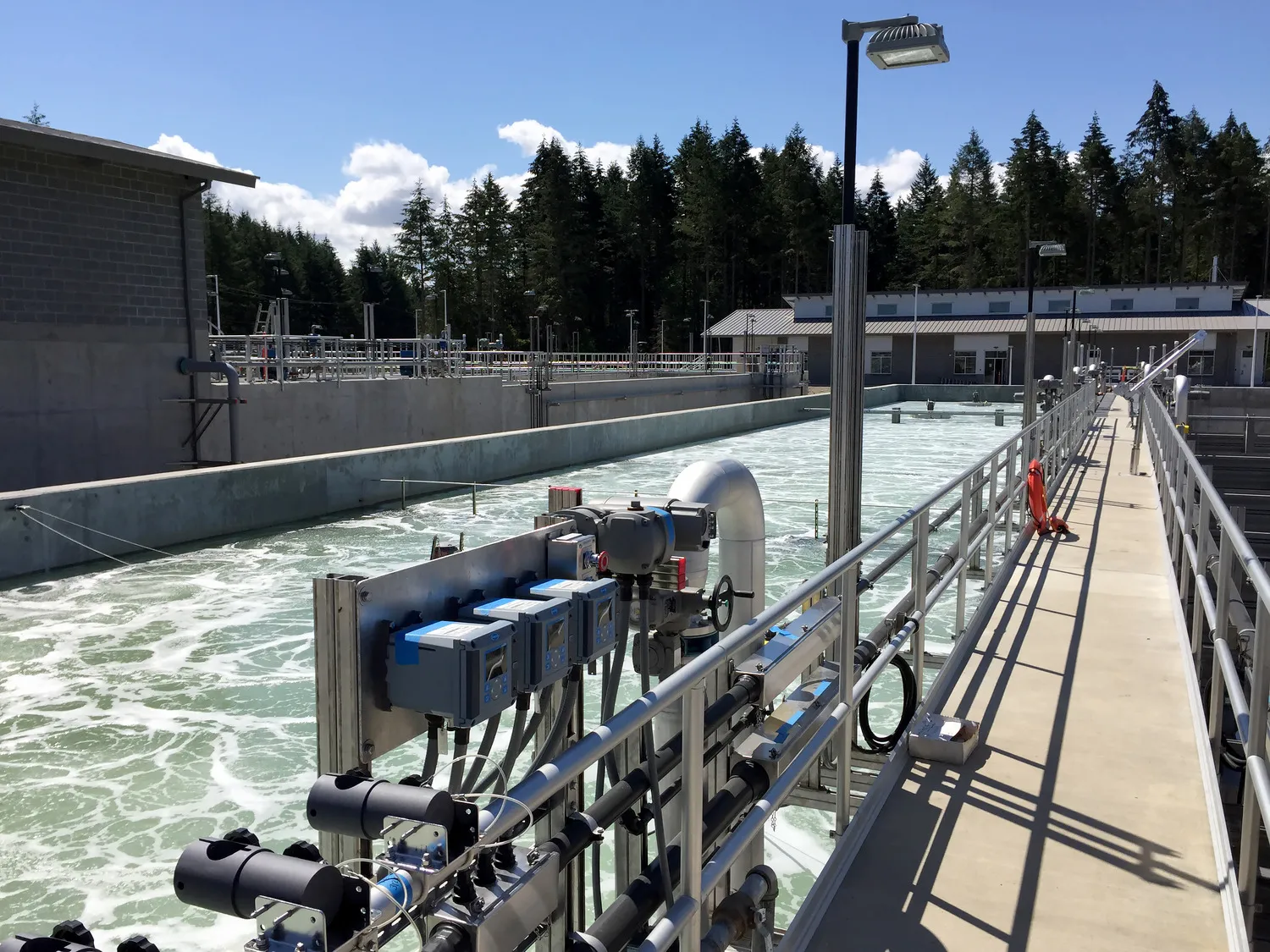
JBLM - Waste Water Treatment Plant
Industrial & Manufacturing
JBLM - Waste Water Treatment Plant
Industrial & Manufacturing
Industrial & Manufacturing, Government
Electrical
Preconstruction, VDC, Sustainability
Seattle
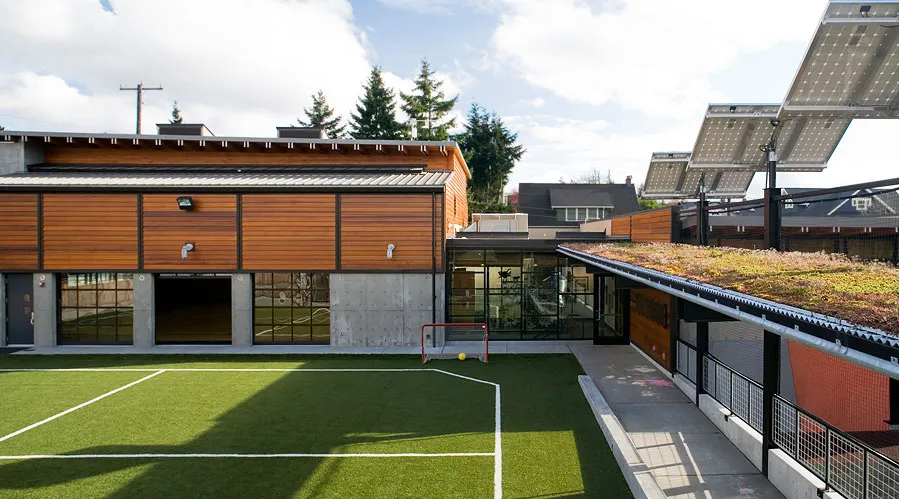
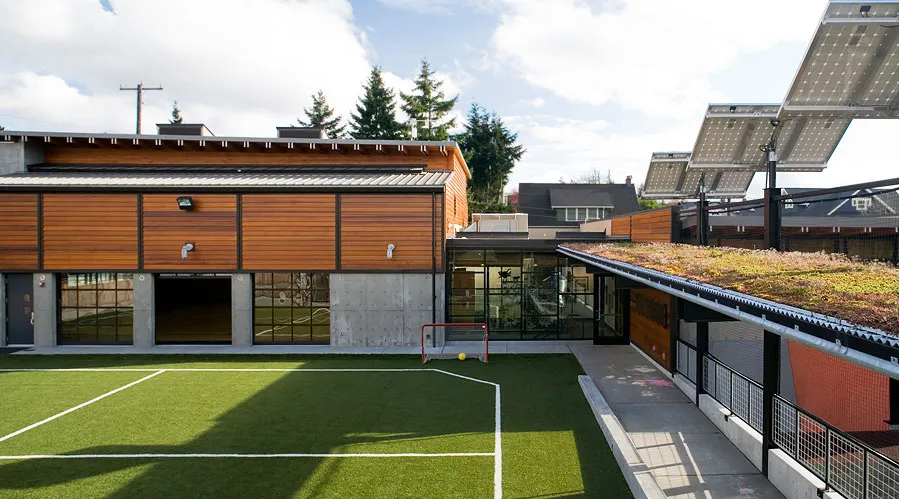
Bertschi School - Living Science Classroom
Commercial
Bertschi School - Living Science Classroom
Commercial
Education
Electrical
Preconstruction, Sustainability
Seattle
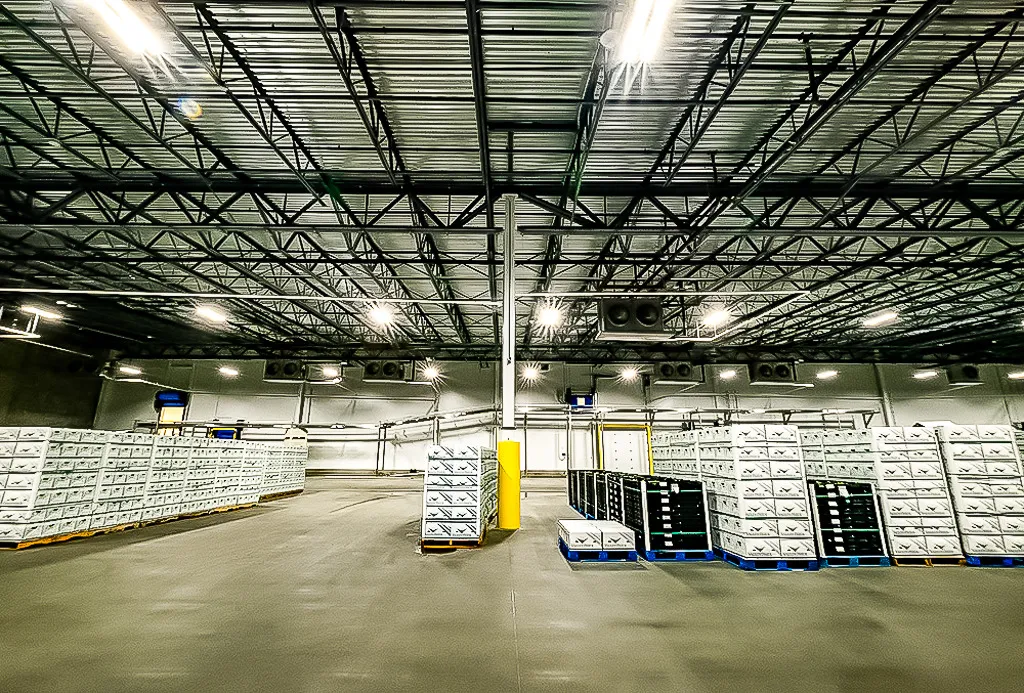
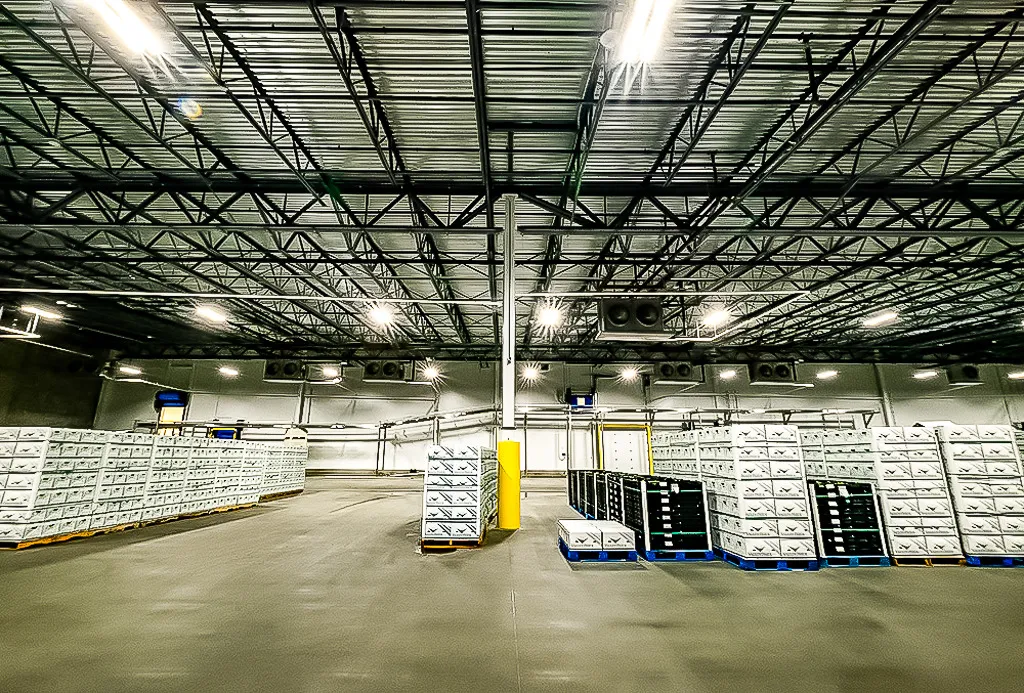
Skagit Valley Farms - Cooling and Operations Facility
Industrial & Manufacturing
Skagit Valley Farms - Cooling and Operations Facility
Industrial & Manufacturing
Industrial & Manufacturing
Electrical
Preconstruction
Bellingham
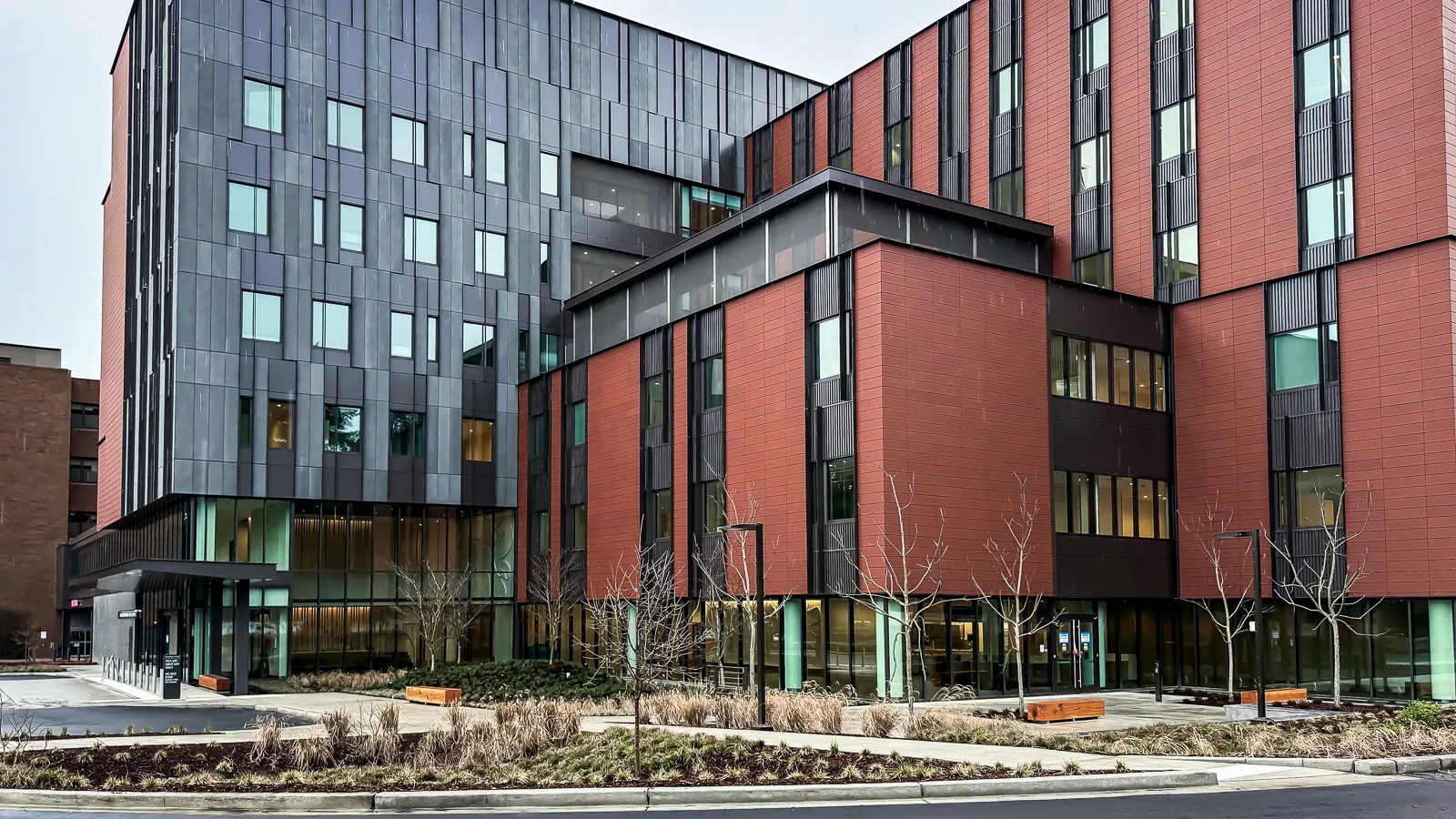
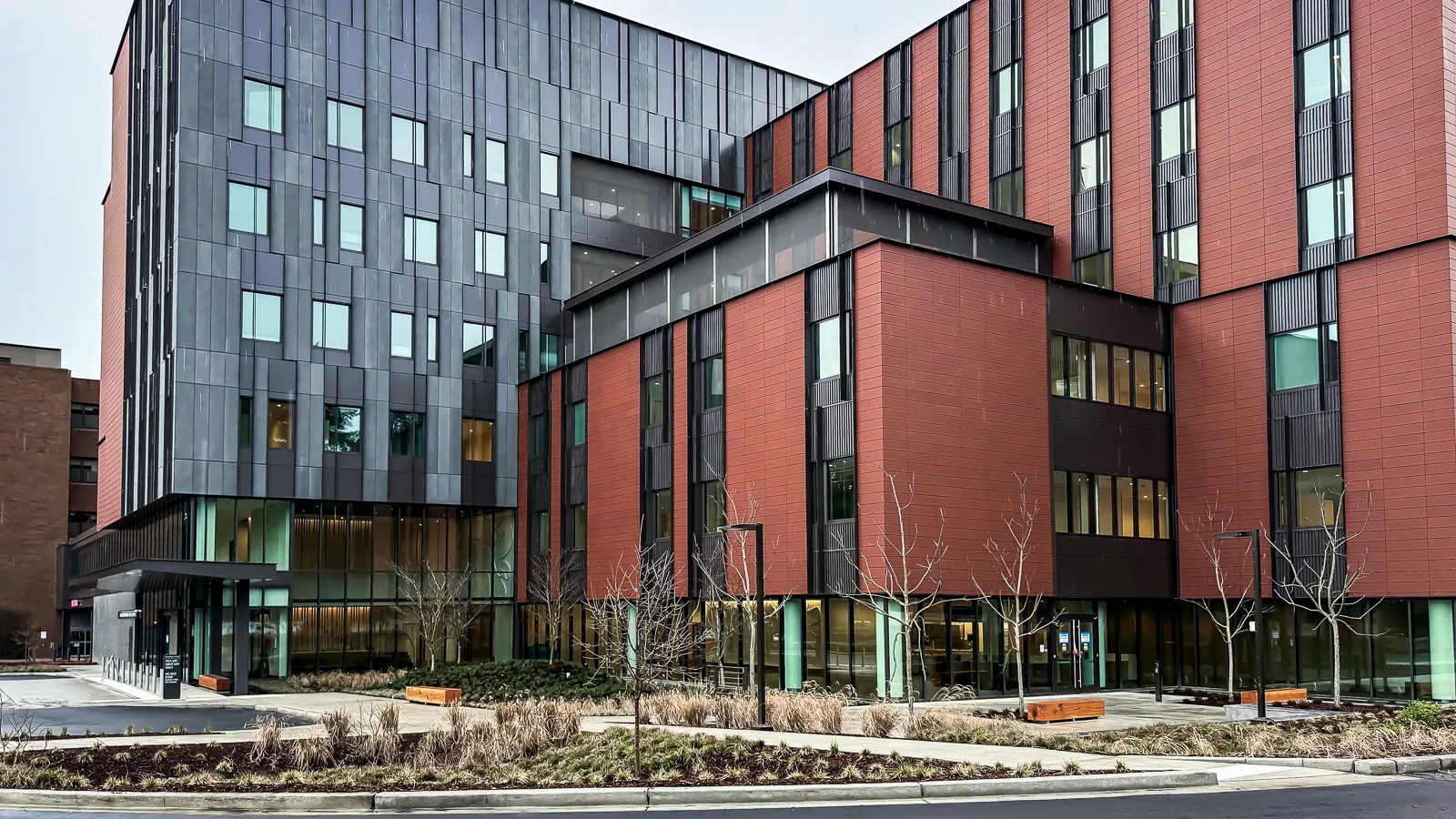
UW - Center for Behavioral Health and Learning
Education
UW - Center for Behavioral Health and Learning
Education
Education, Healthcare
Electrical, Technologies
Preconstruction, MWESB Participation, Fabrication
Seattle
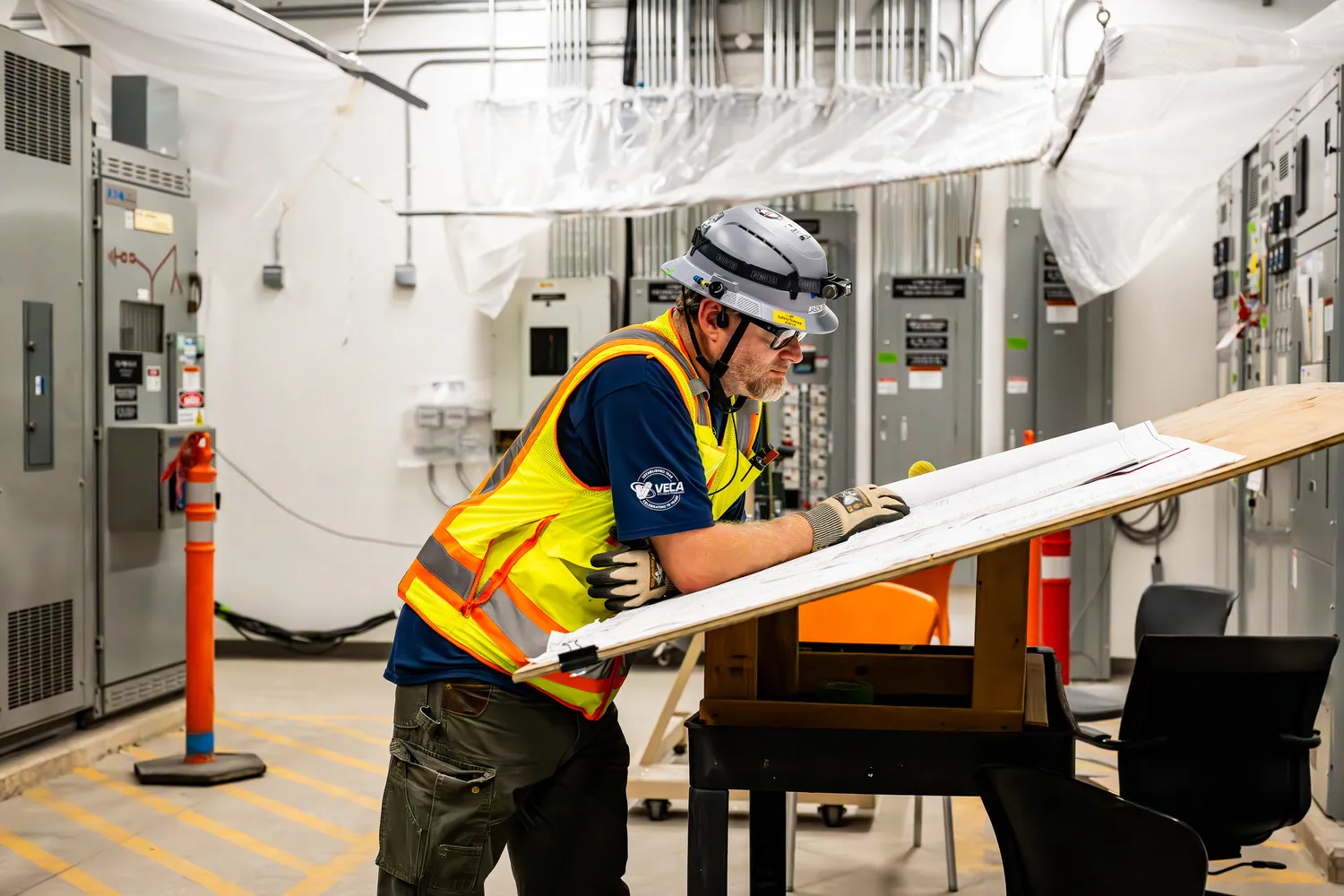
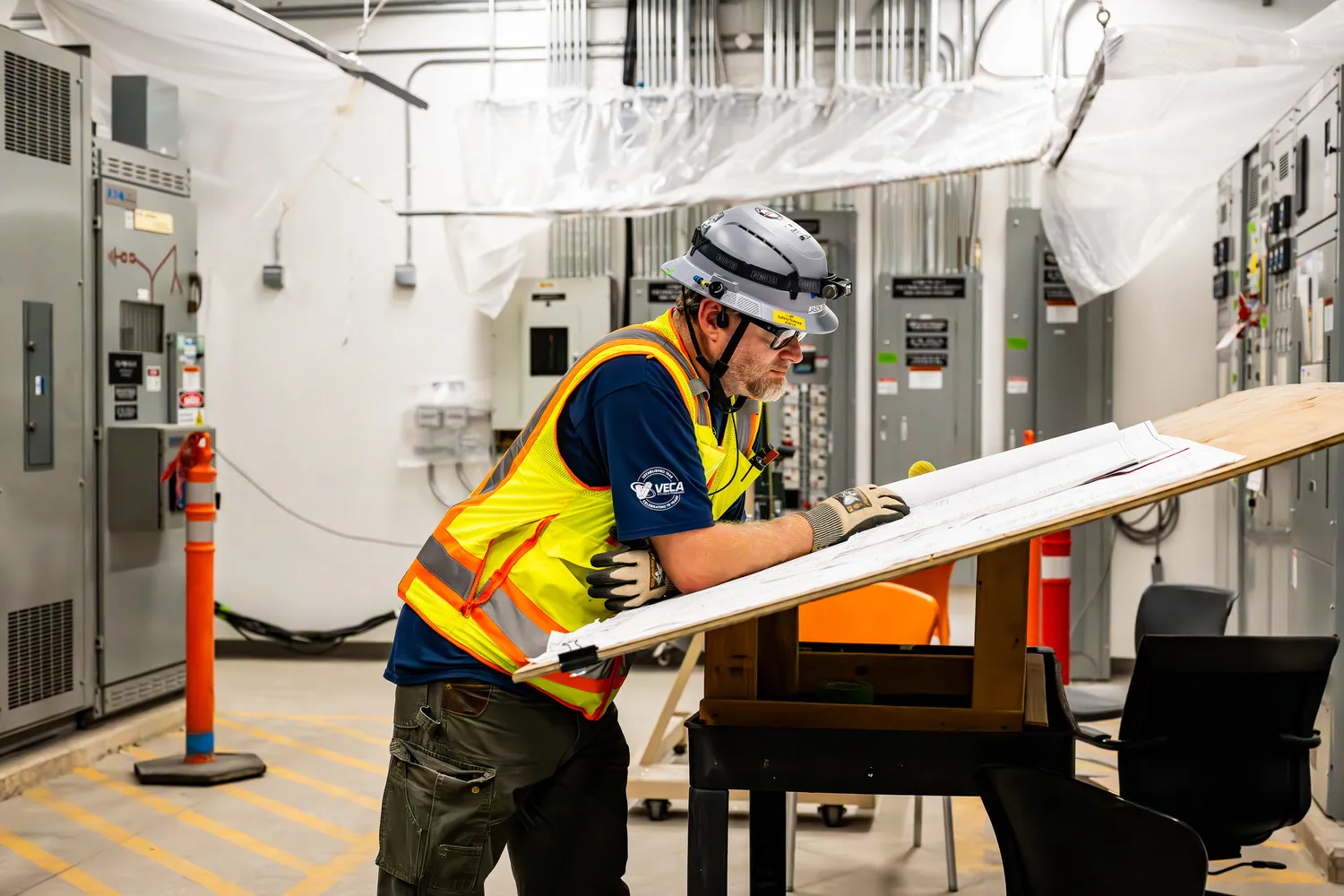
SEA - C Concourse Expansion
Transportation Infrastructure
SEA - C Concourse Expansion
Transportation Infrastructure
Transportation Infrastructure
Electrical
Diversity, Fabrication, VDC, Preconstruction
Seattle
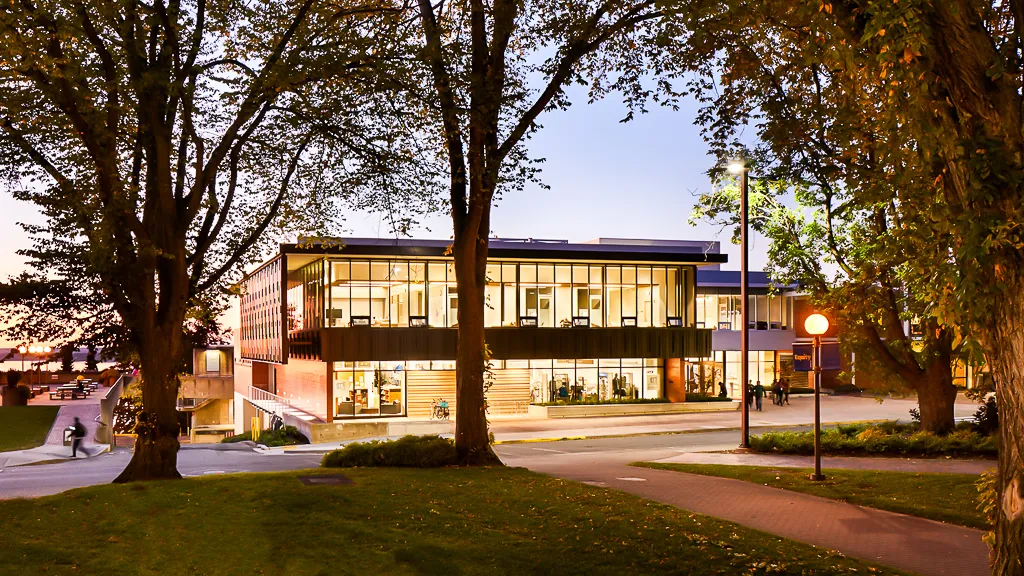
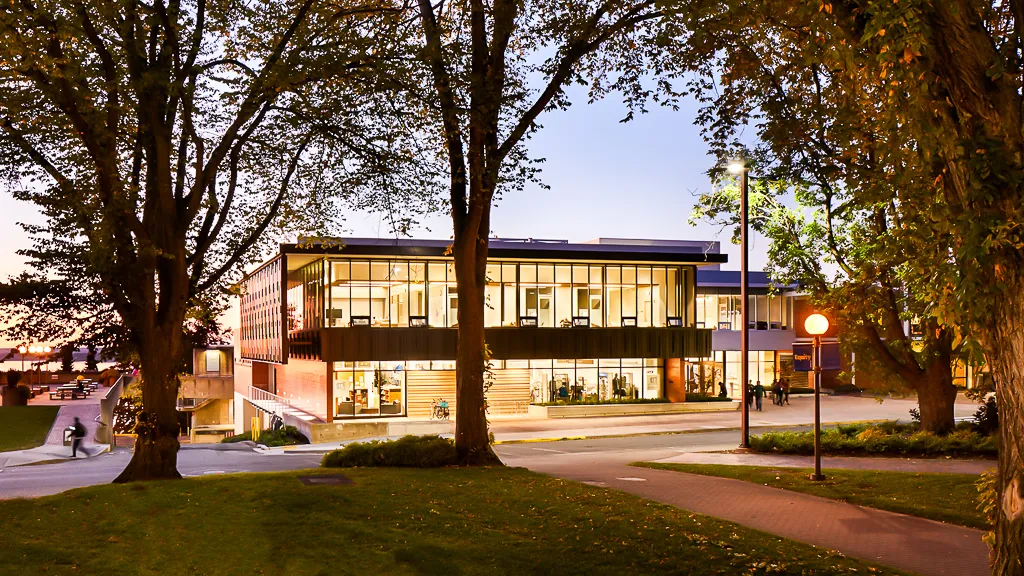
WWU - Multicultural Center
Education
WWU - Multicultural Center
Education
Education
Electrical
Diversity, Sustainability
Bellingham
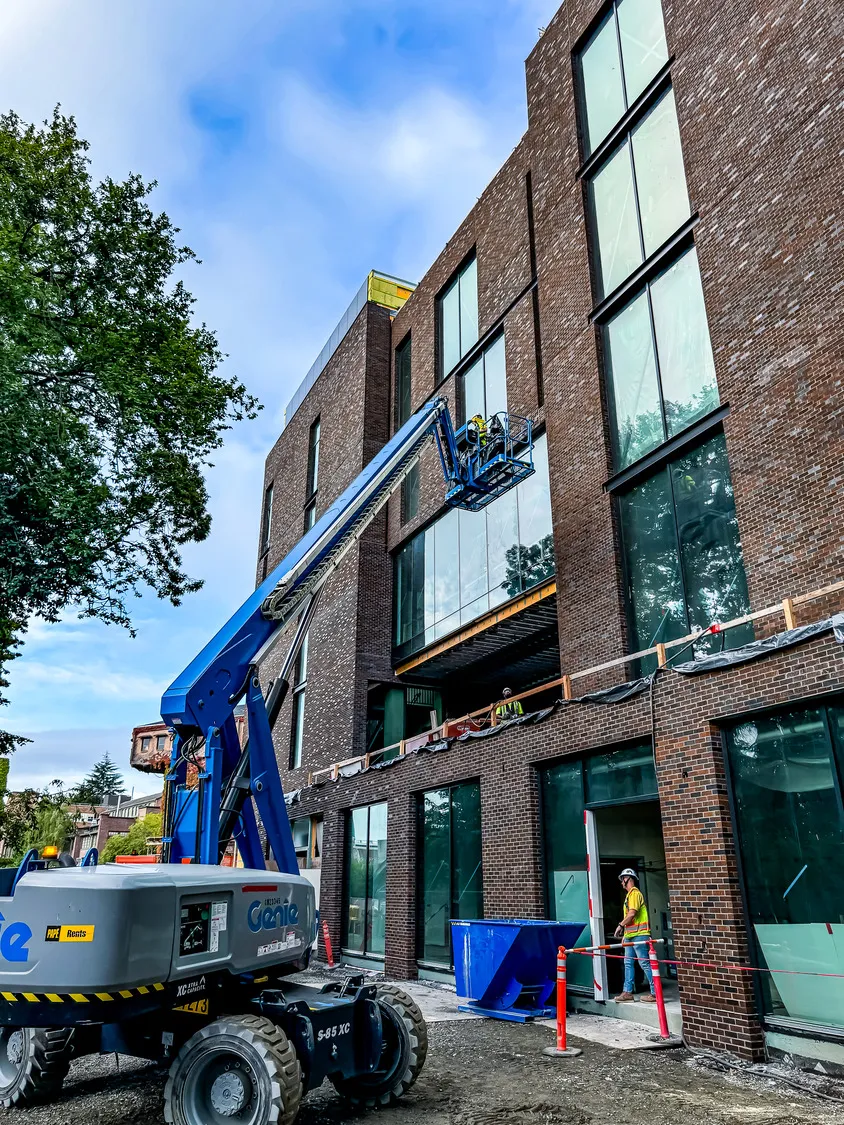
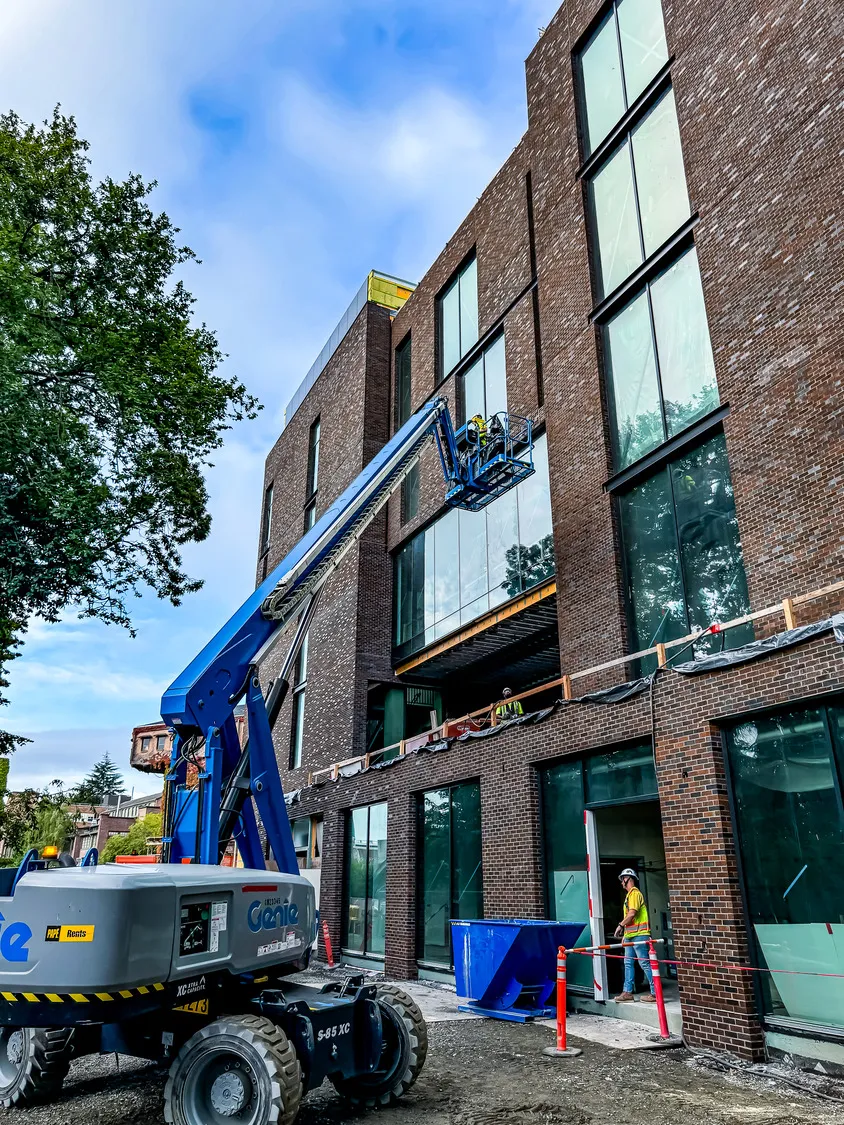
UW - Interdisciplinary Engineering Building
Education
UW - Interdisciplinary Engineering Building
Education
Education
Electrical
Fabrication, Sustainability, VDC, Preconstruction
Seattle
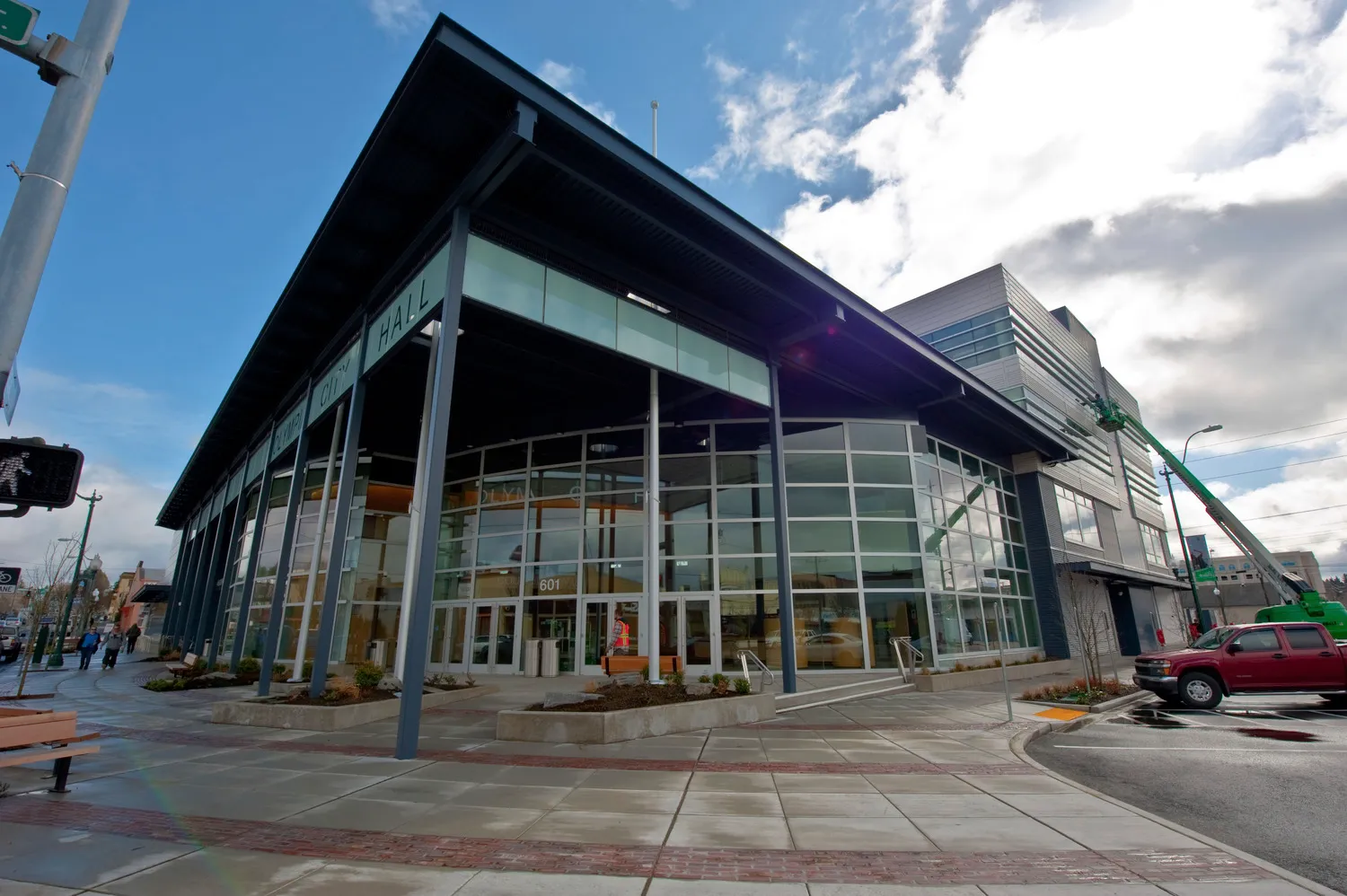
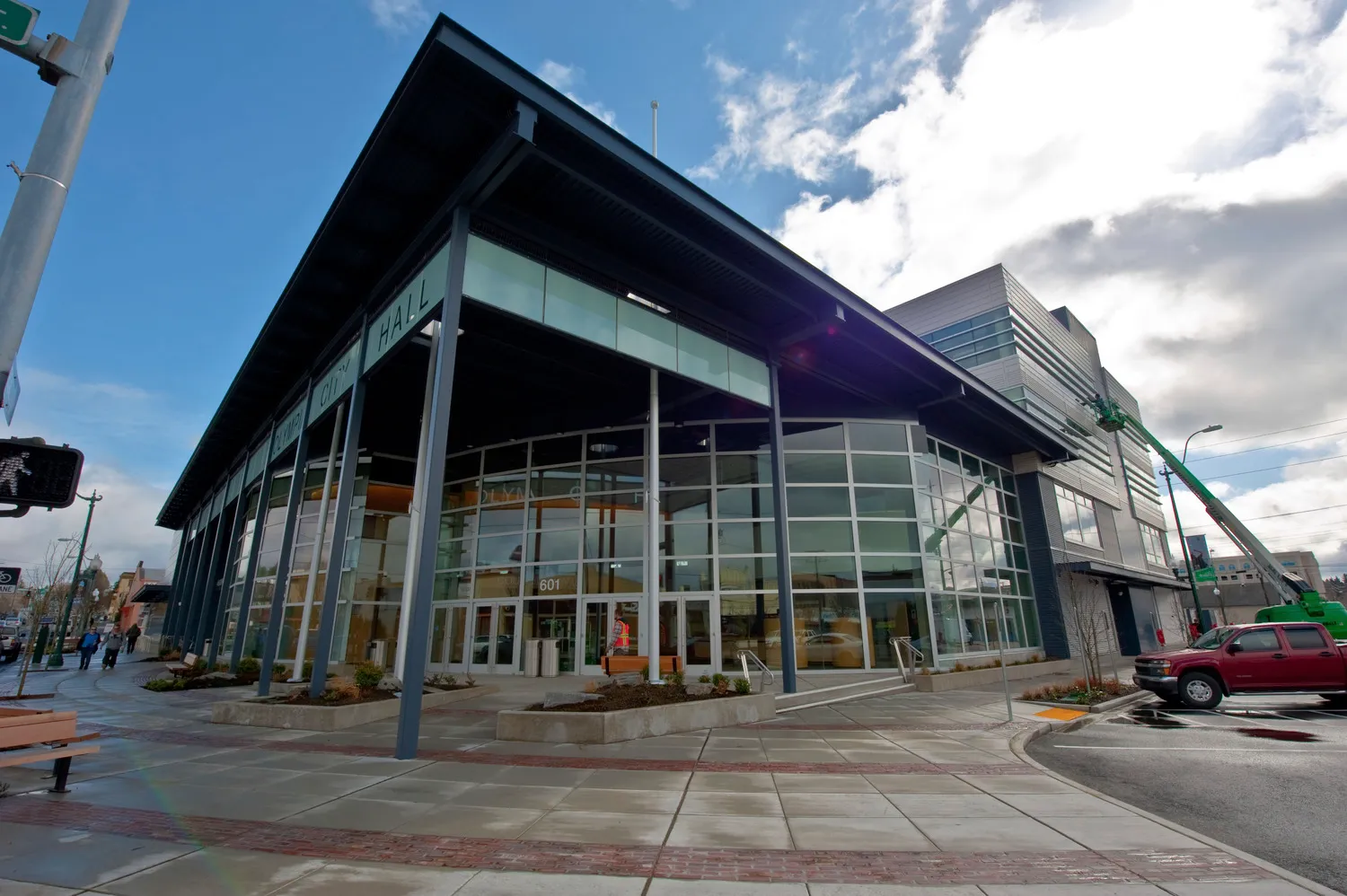
Olympia City Hall
Government
Olympia City Hall
Government
Government
Electrical
VDC, Sustainability, Preconstruction
Seattle
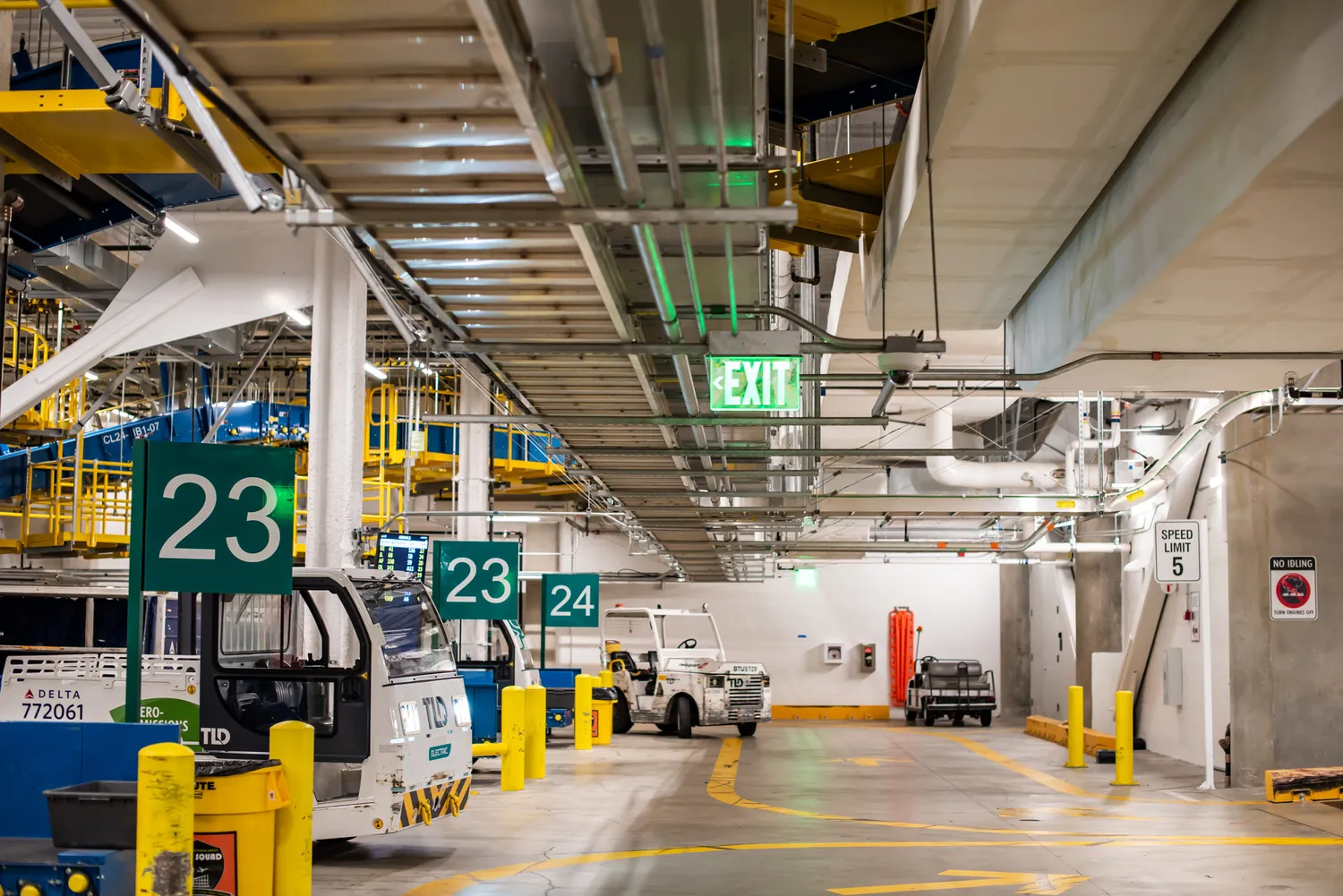
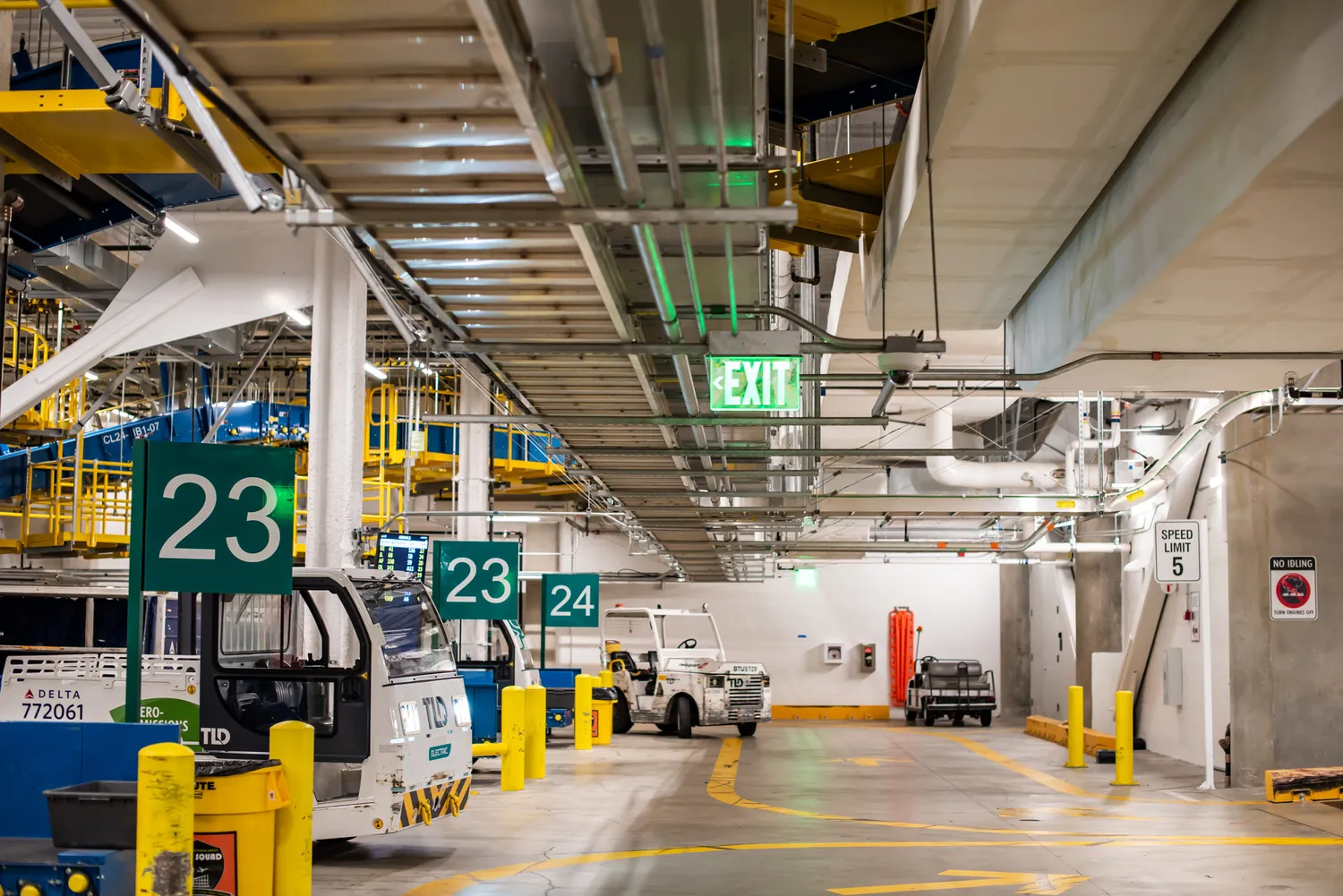
SEA - IAF Baggage Handling System
Transportation Infrastructure
SEA - IAF Baggage Handling System
Transportation Infrastructure
Transportation Infrastructure
Electrical
Preconstruction, Fabrication
Seattle
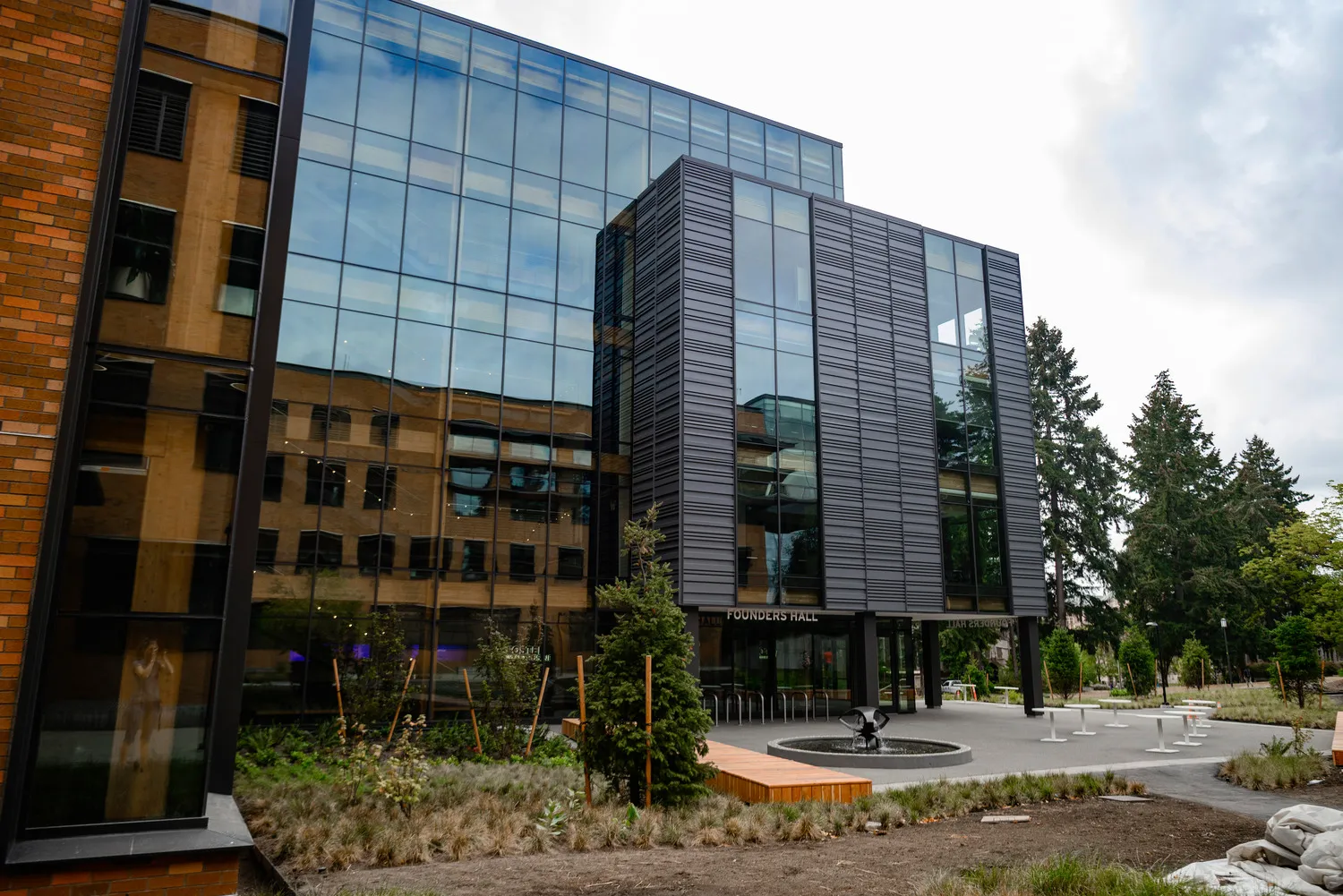
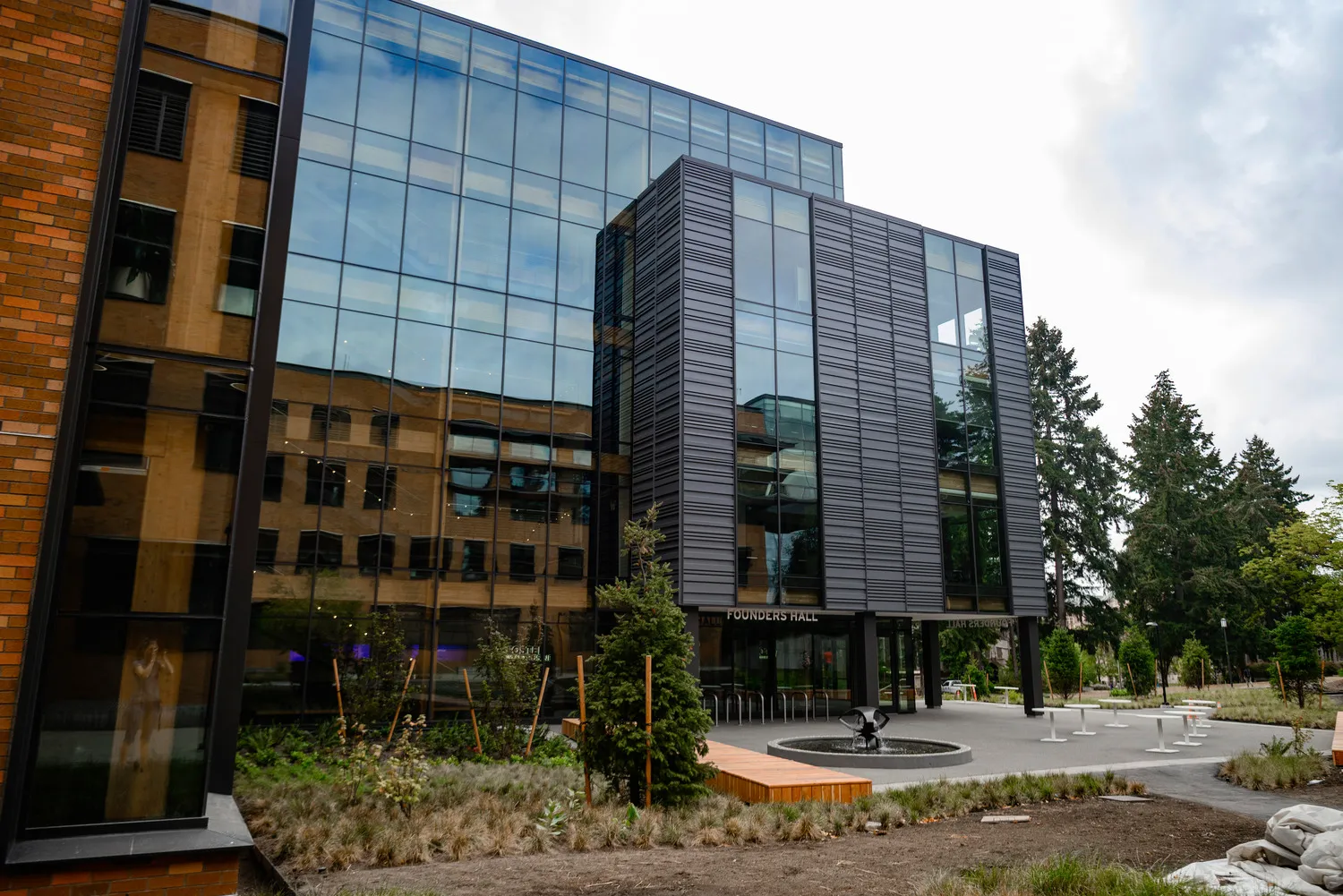
UW - Foster School of Business
Education
UW - Foster School of Business
Education
Education
Electrical, Technologies
Fabrication, Diversity, VDC, Preconstruction, Sustainability
Seattle
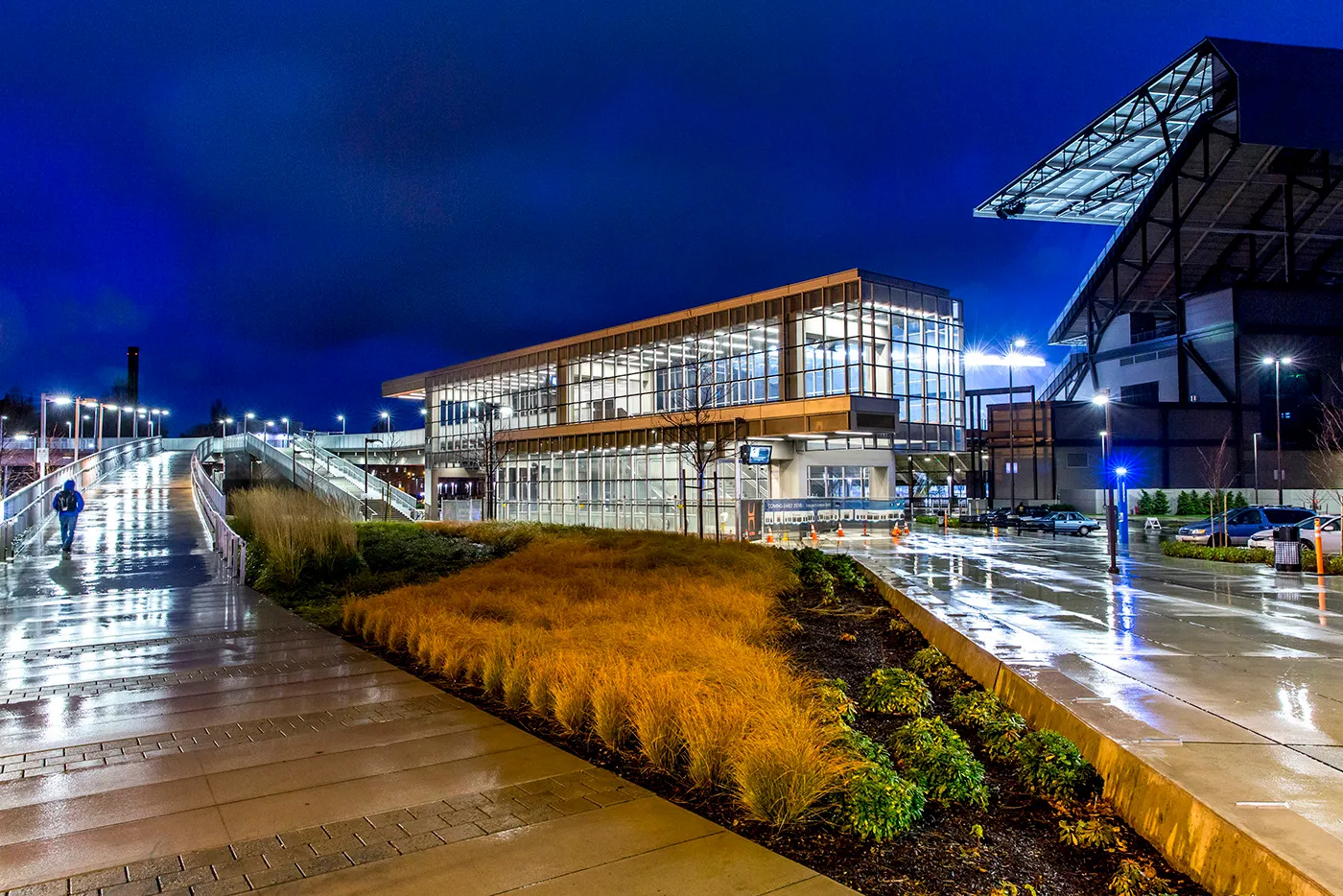
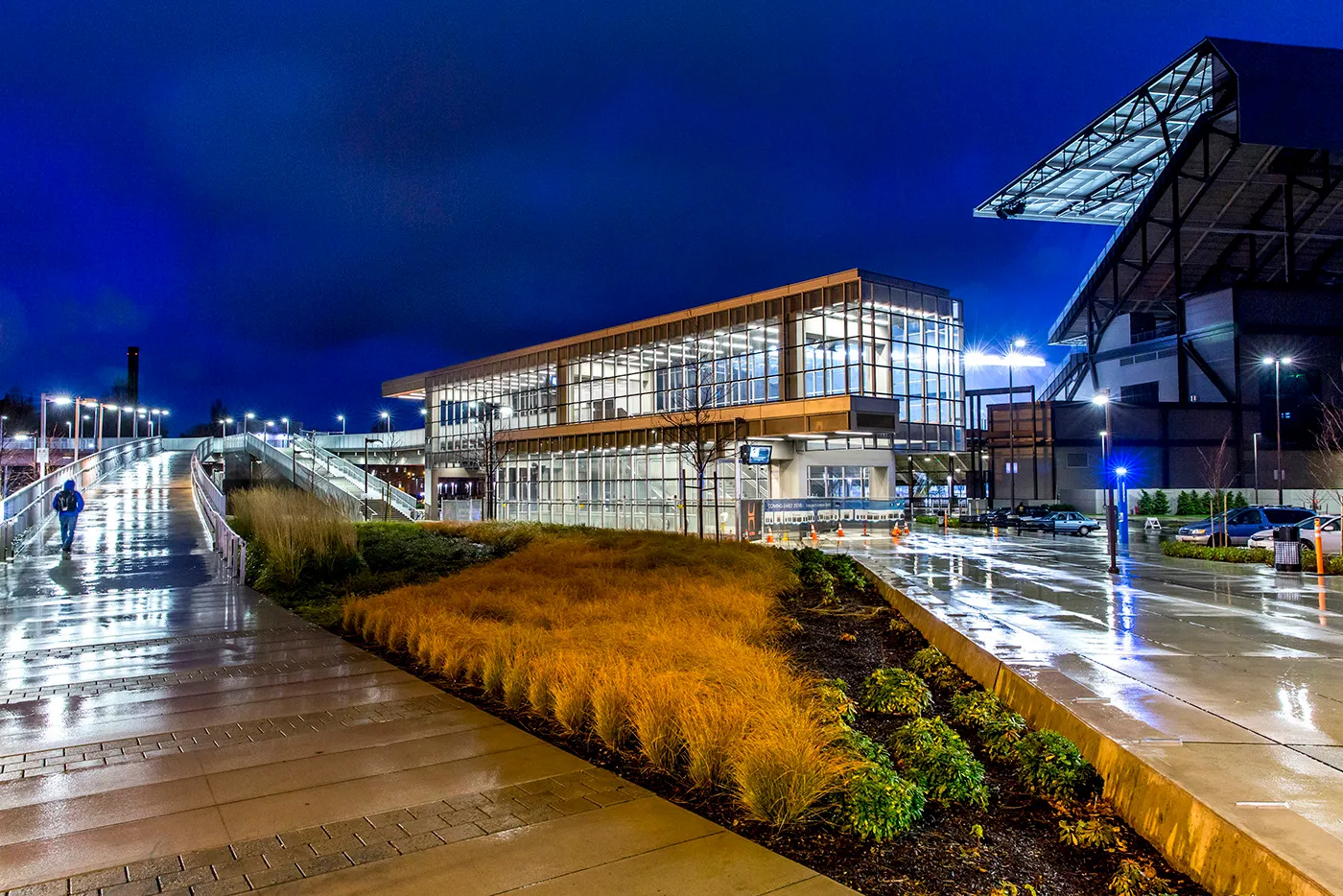
Sound Transit - N140 U District Station
Transportation Infrastructure
Sound Transit - N140 U District Station
Transportation Infrastructure
Transportation Infrastructure
Electrical
VDC, Preconstruction
Seattle
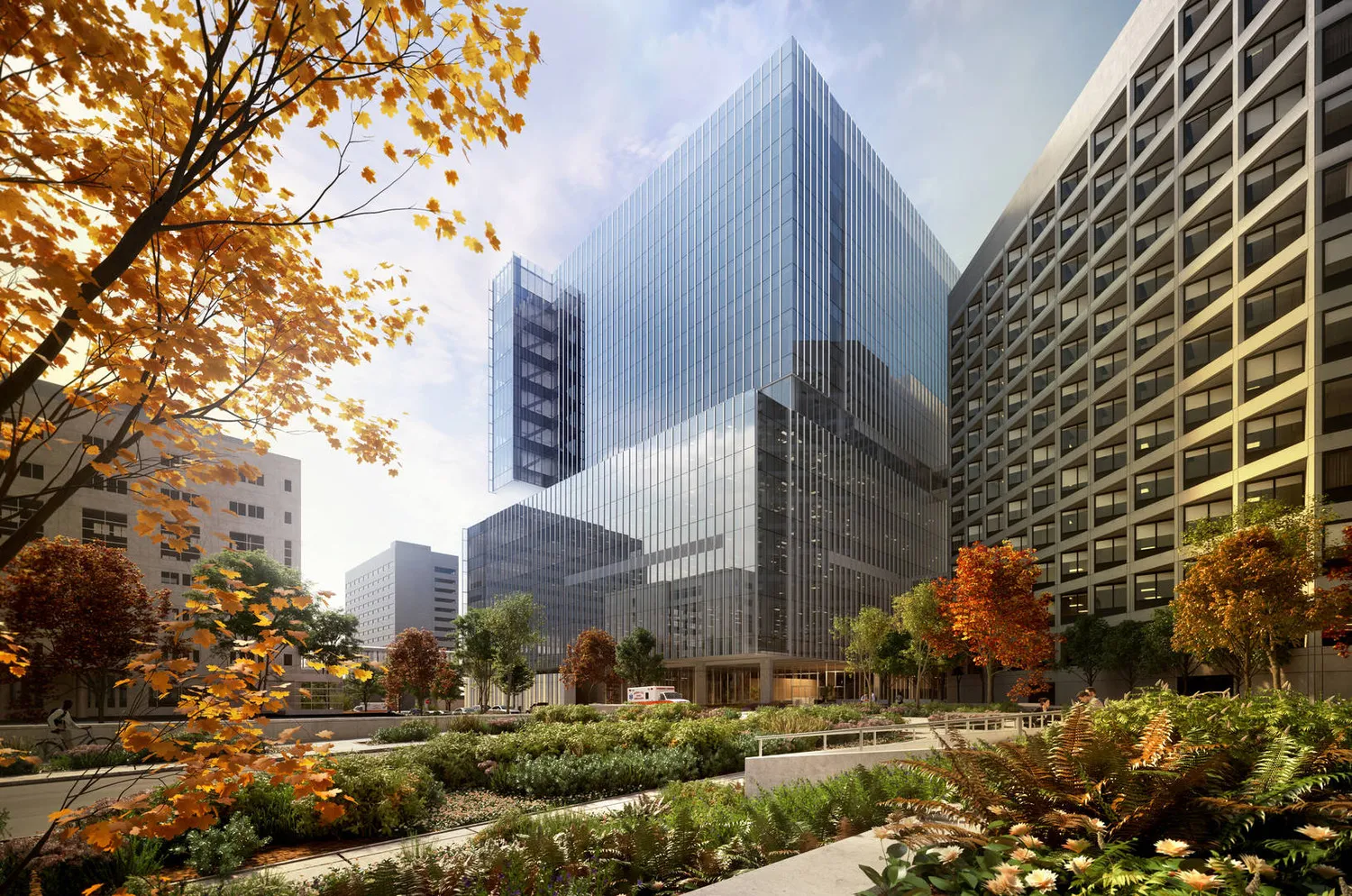
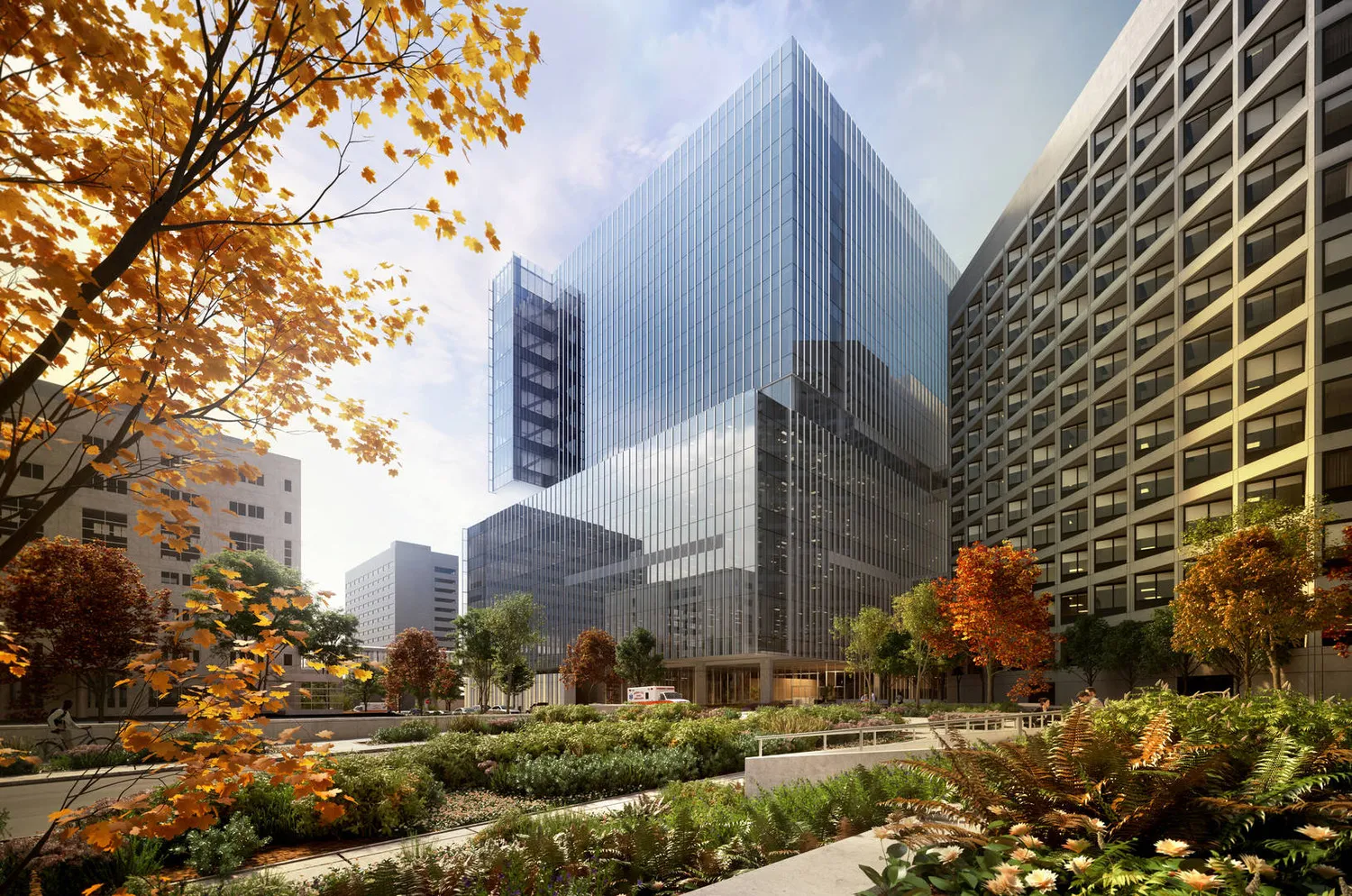
Swedish - First Hill North Tower
Healthcare
Swedish - First Hill North Tower
Healthcare
Healthcare
Electrical
Preconstruction, Fabrication, VDC
Seattle
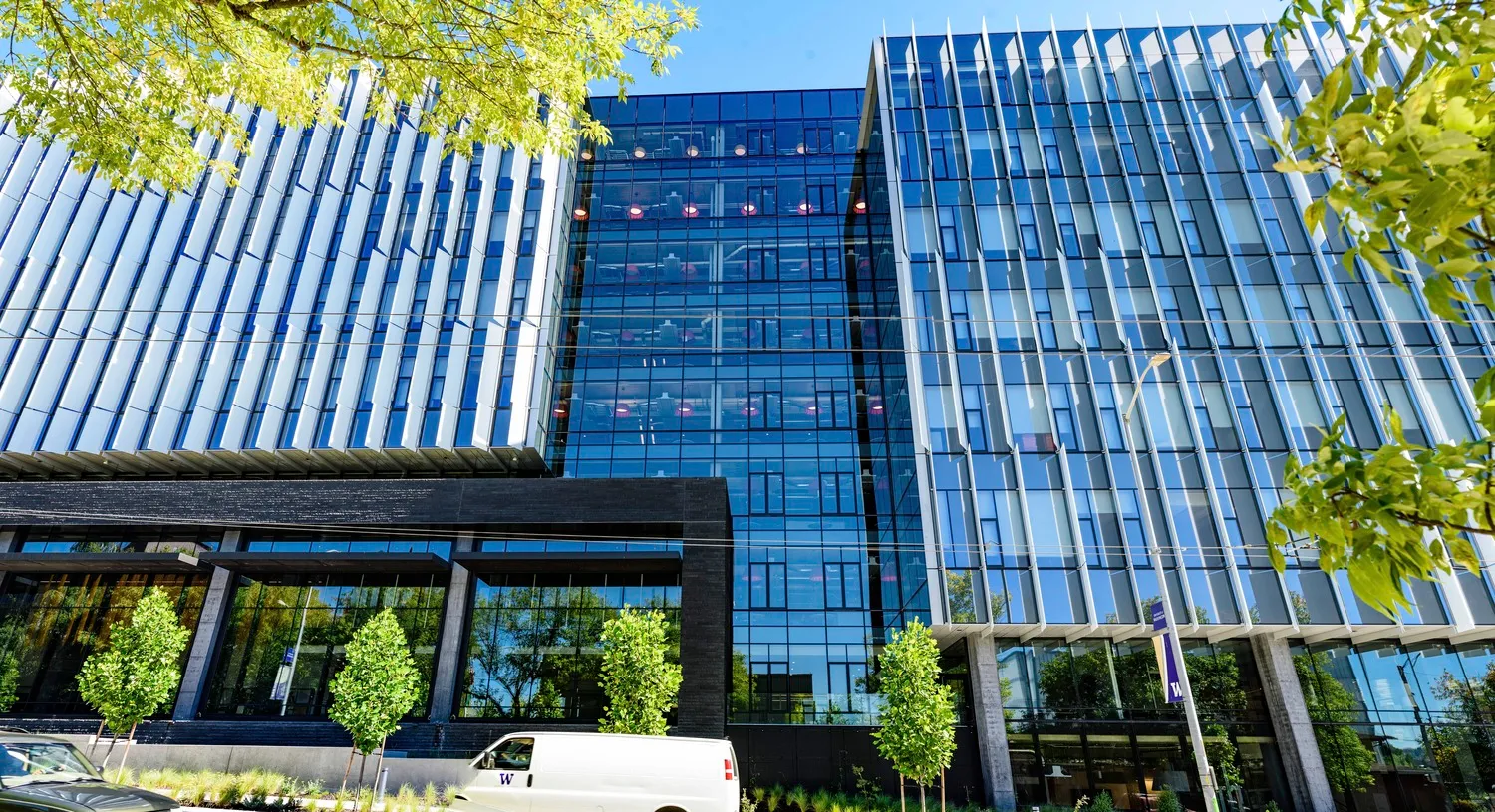
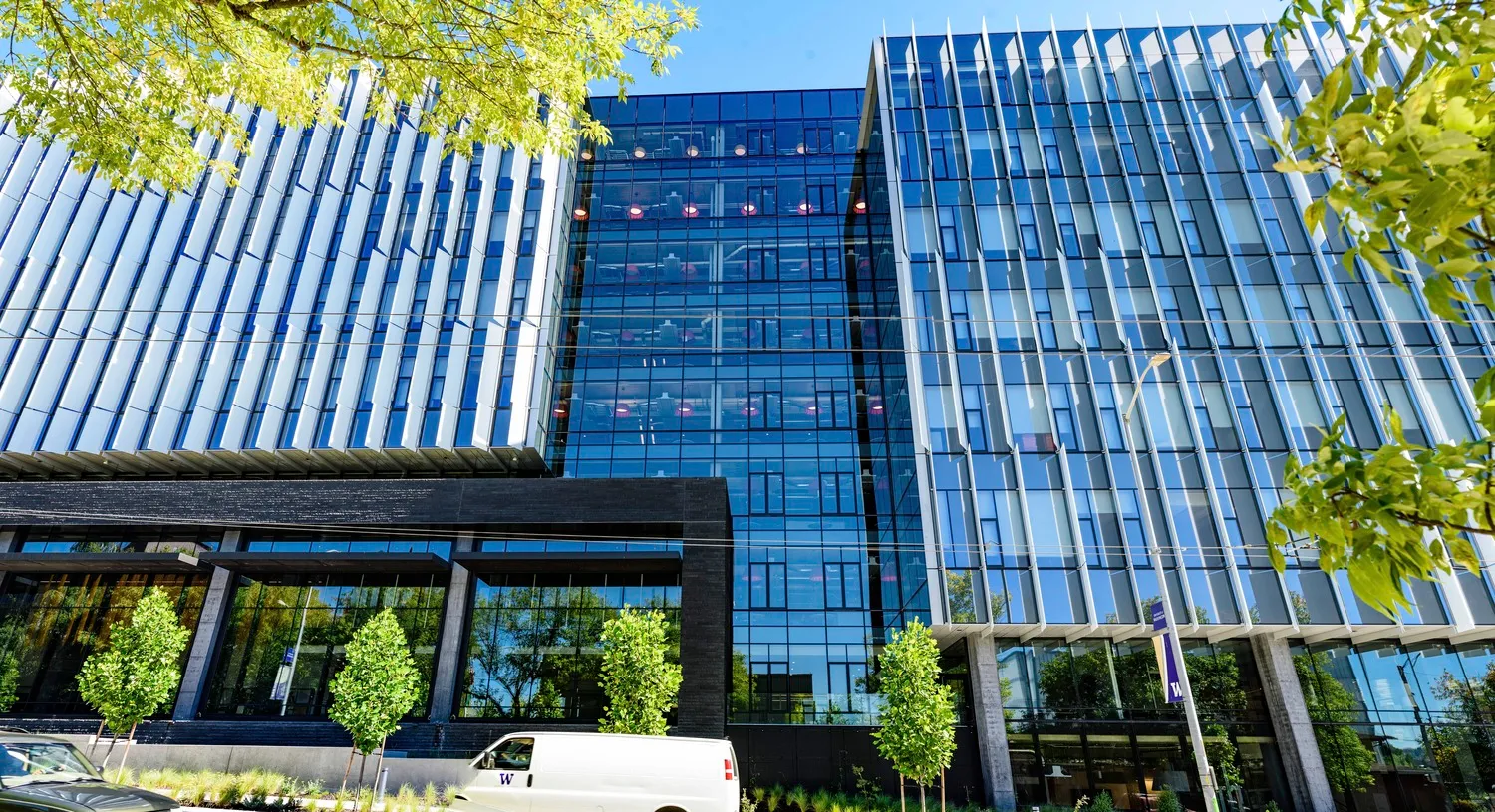
UW - Hans Rosling Center for Population Health
Education
UW - Hans Rosling Center for Population Health
Education
Education
Electrical, Technologies
Fabrication, Diversity, VDC, Preconstruction, Sustainability
Seattle
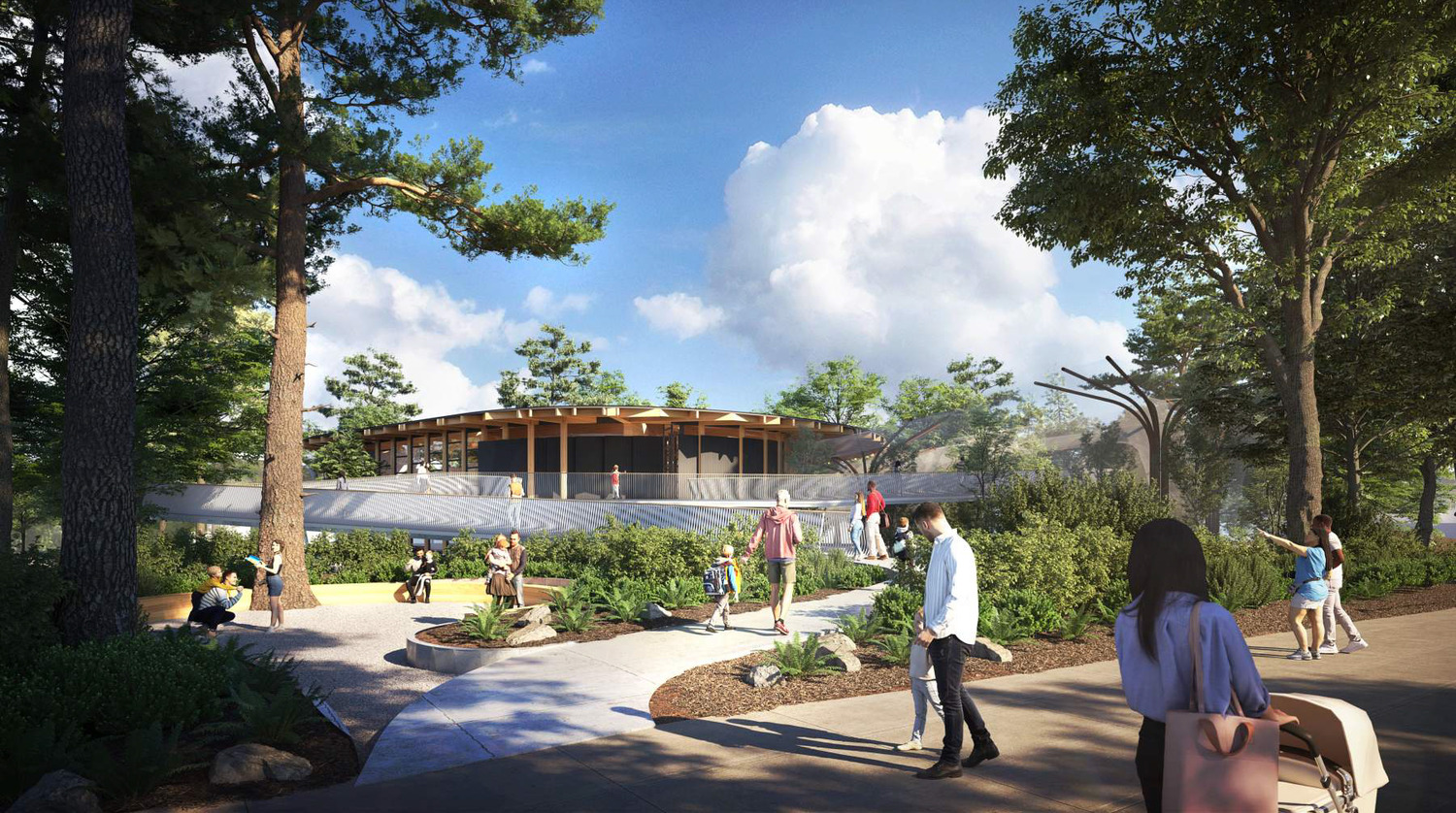
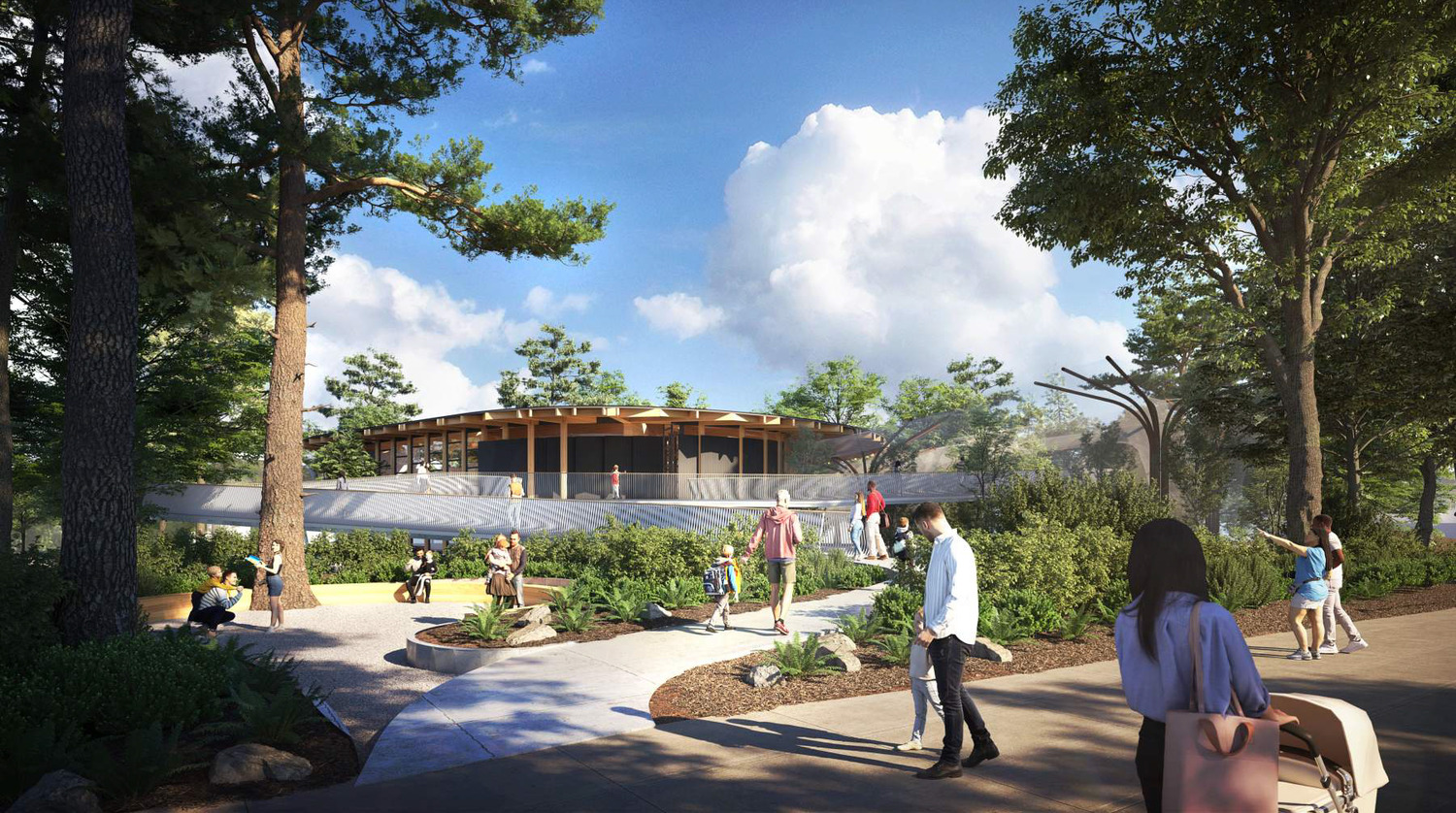
Woodland Park Zoo Forest Trailhead
Commercial
Woodland Park Zoo Forest Trailhead
Commercial
Commercial
Electrical
Sustainability
Seattle
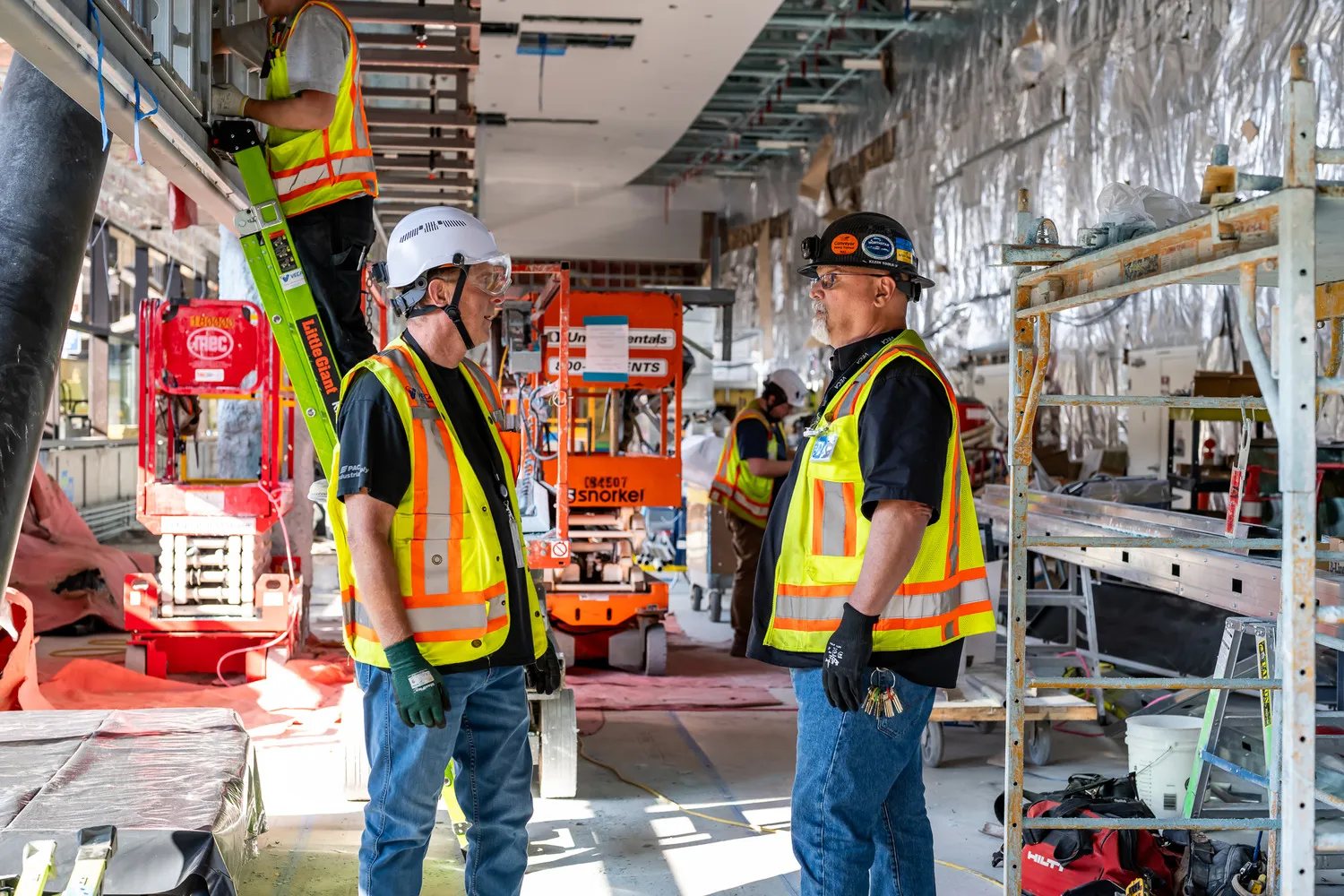
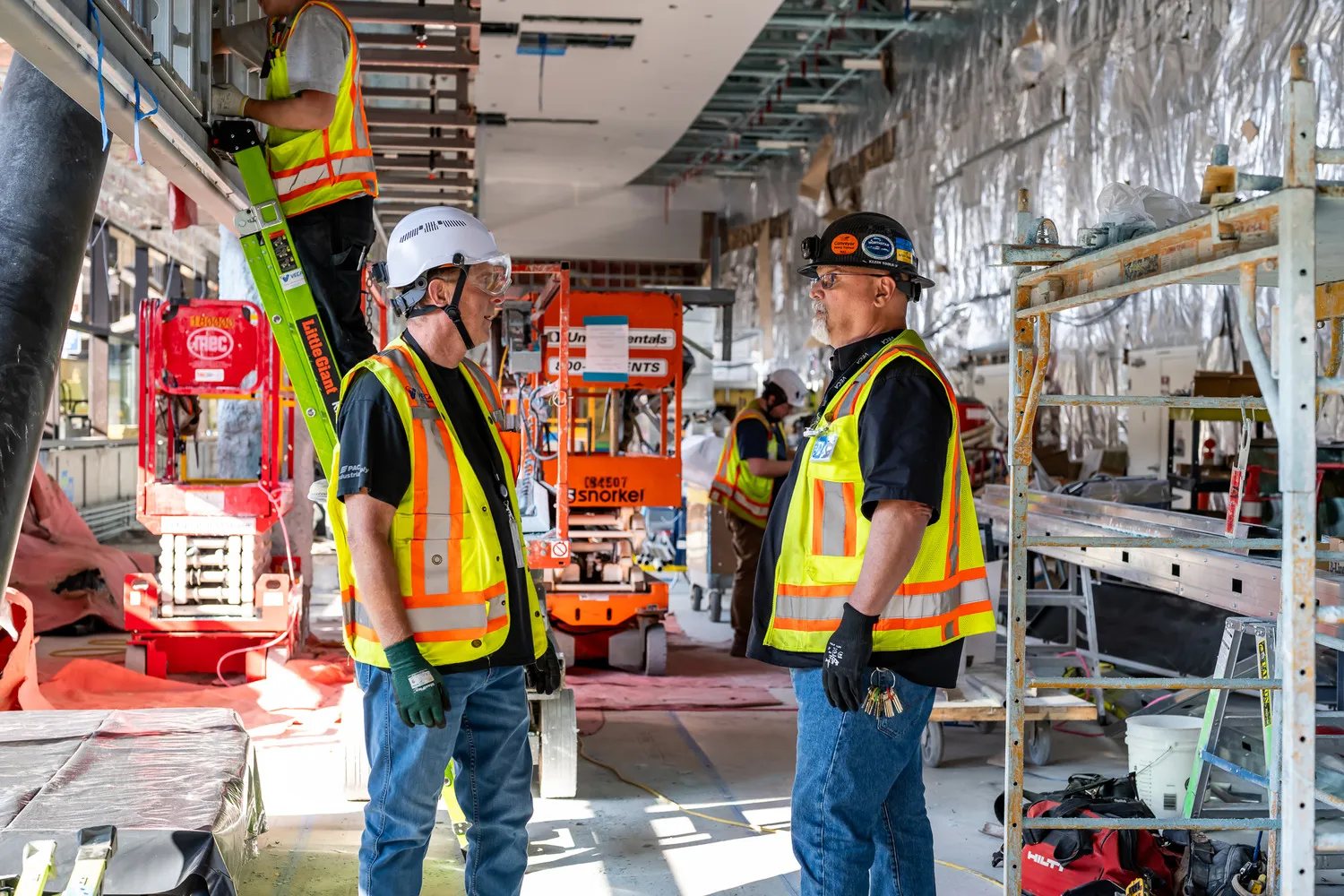
SEA - North Main Terminal Redevelopment
Transportation Infrastructure
SEA - North Main Terminal Redevelopment
Transportation Infrastructure
Transportation Infrastructure
Electrical, Technologies
VDC, Alternative Delivery, Fabrication
Seattle
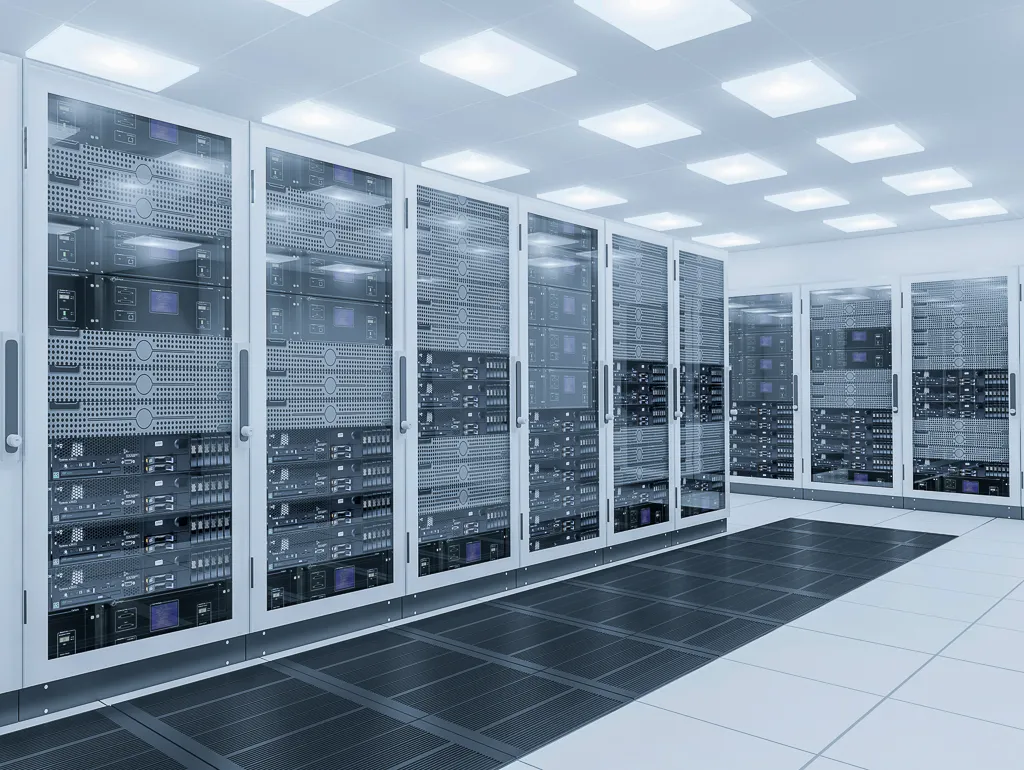
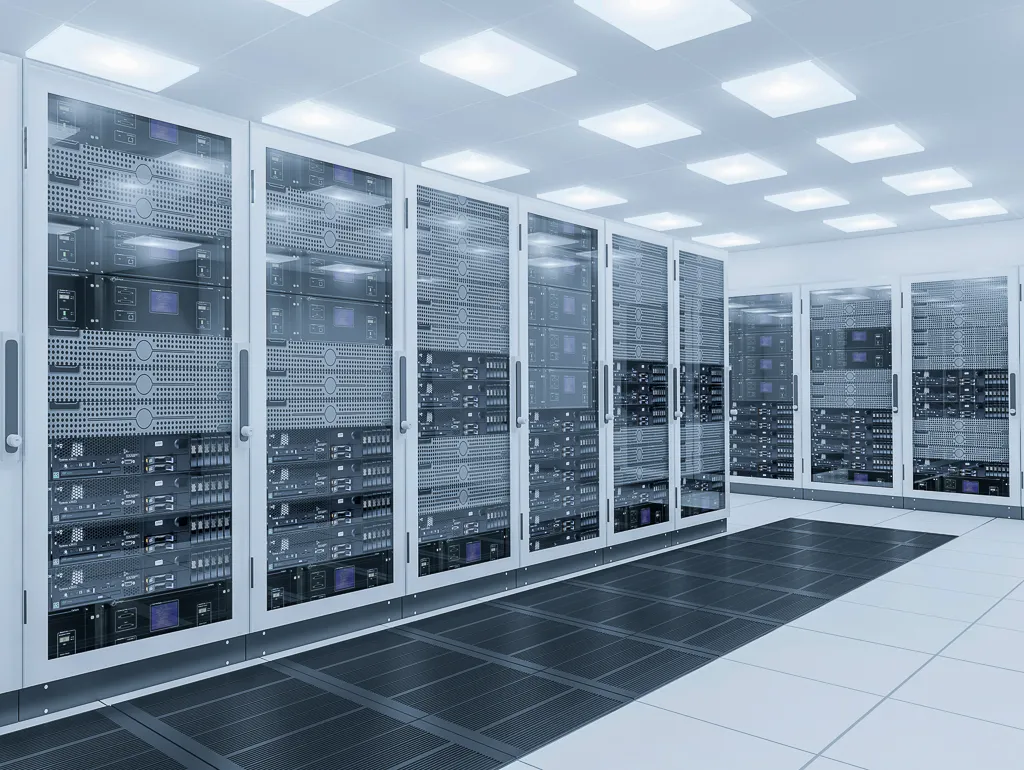
45MW Hyperscale DC - A
Mission Critical
45MW Hyperscale DC - A
Mission Critical
Mission Critical
Electrical
Wenatchee
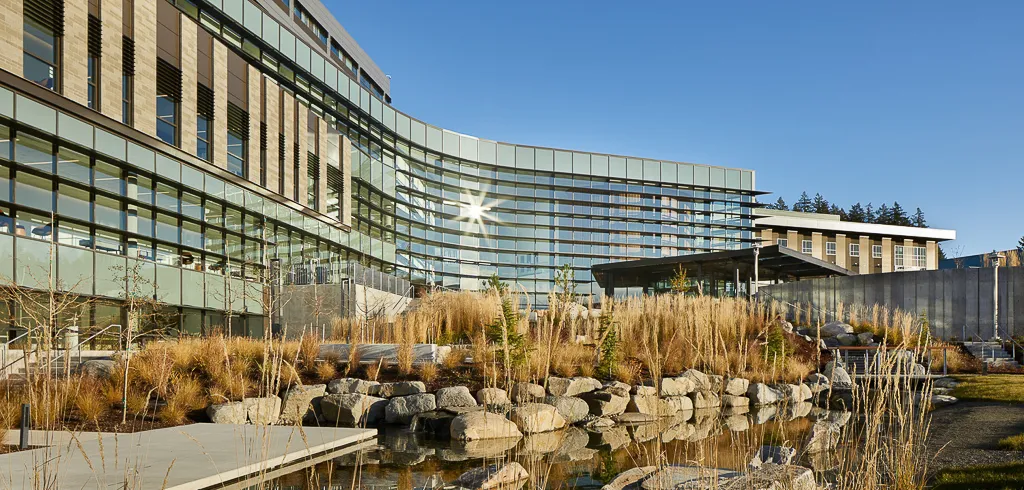
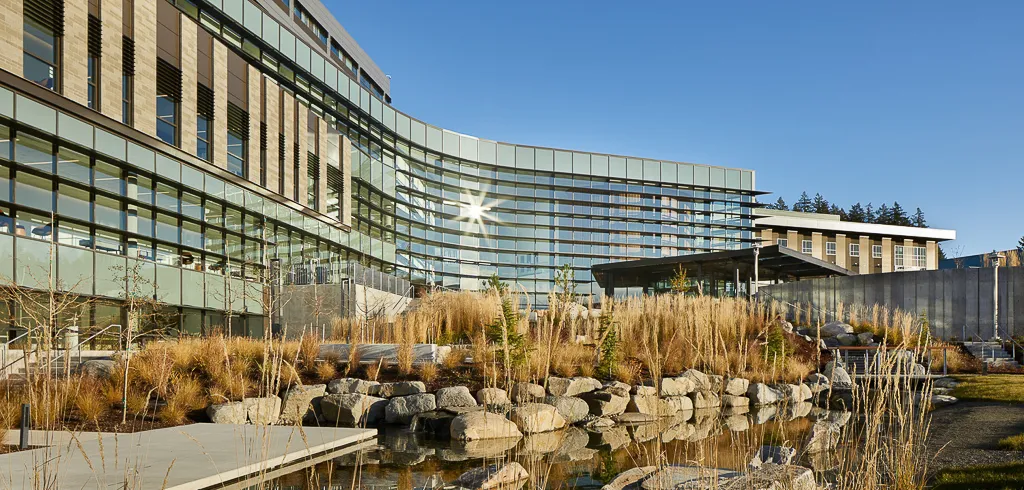
St. Michael Medical Center Acute Care Expansion
Healthcare
St. Michael Medical Center Acute Care Expansion
Healthcare
Healthcare
Electrical
Fabrication, Sustainability
Seattle
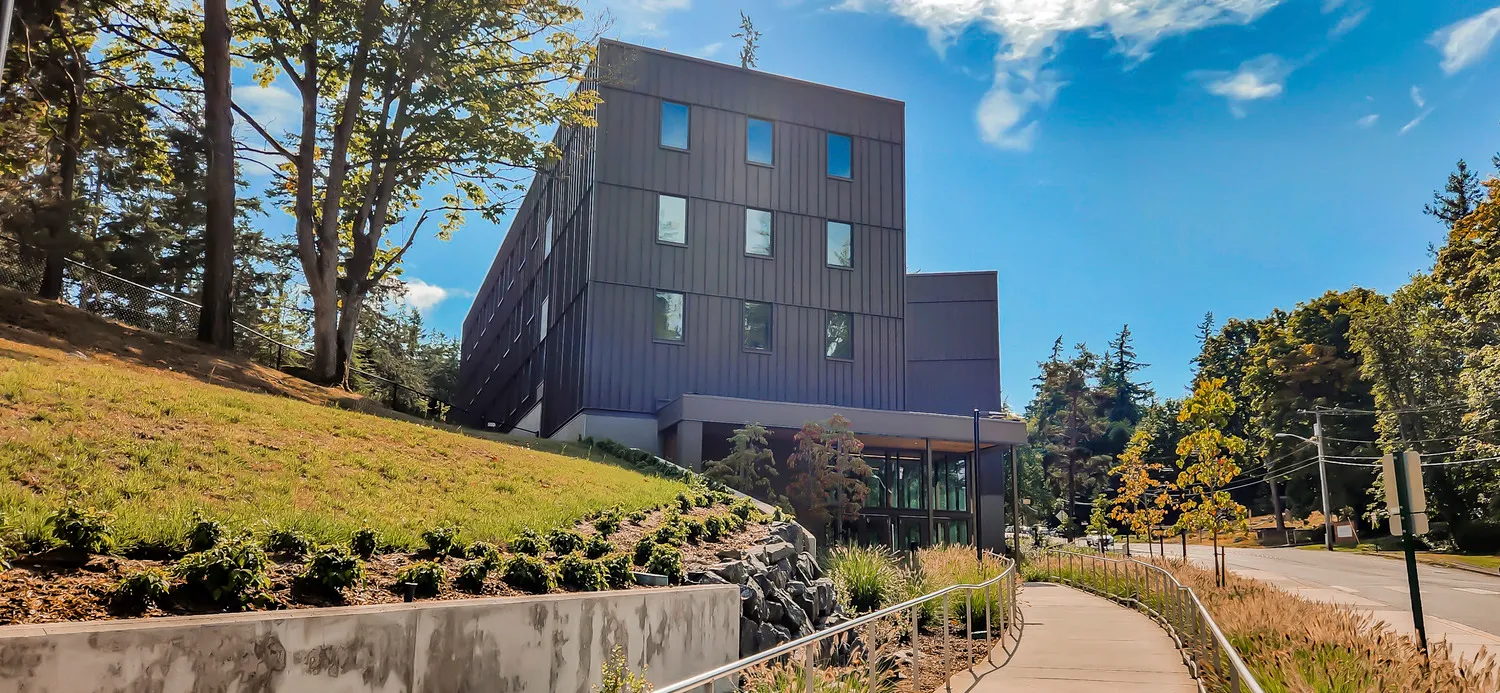
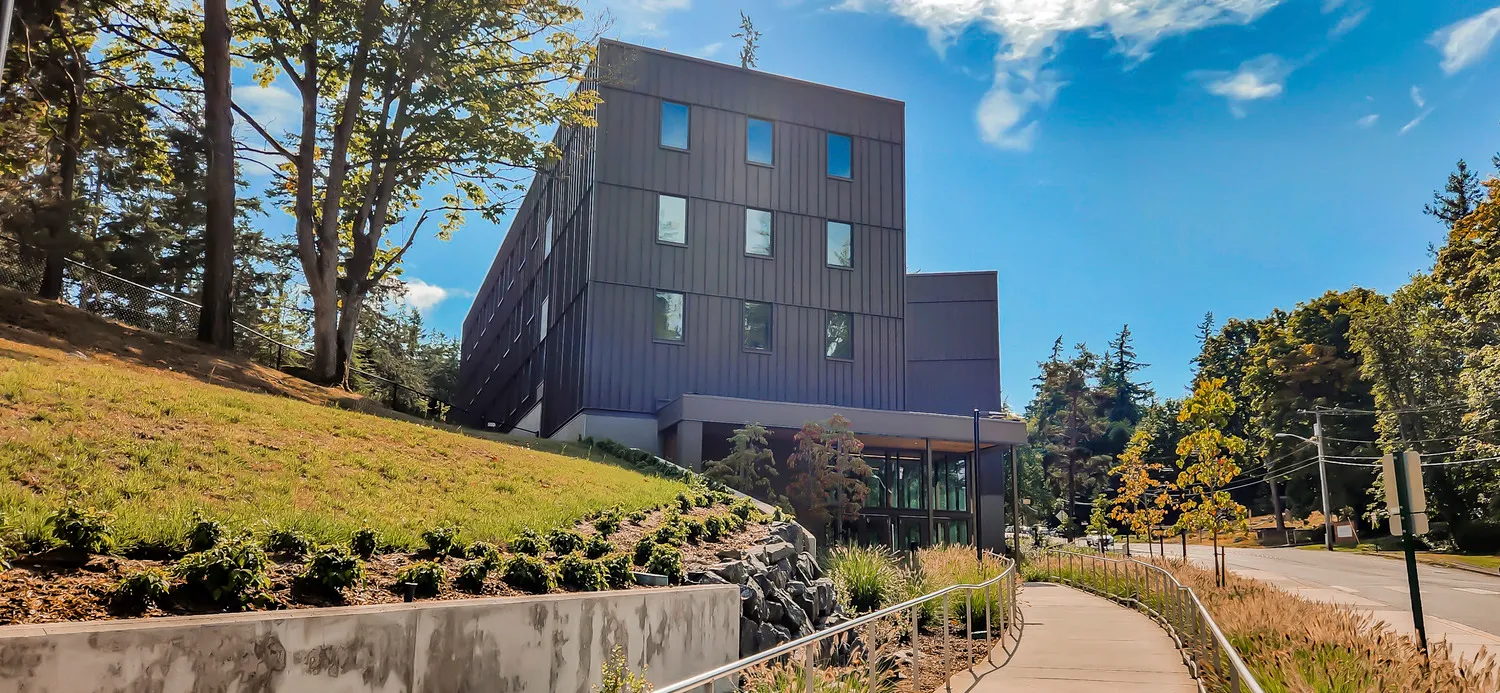
WWU - Alma Clark Glass Hall
Education
WWU - Alma Clark Glass Hall
Education
Education, Commercial
Electrical
VDC, Preconstruction, Sustainability, Diversity
Bellingham
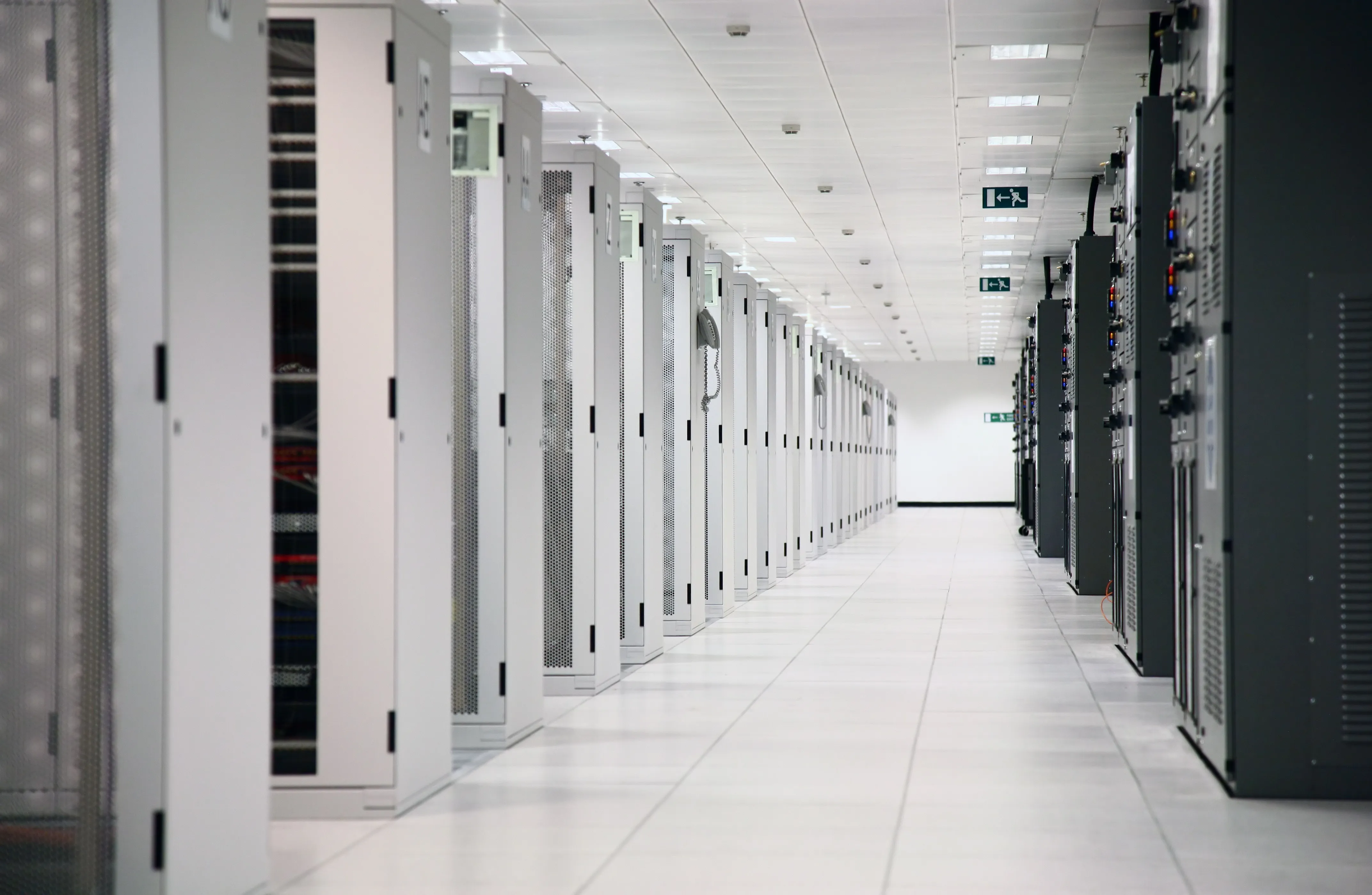
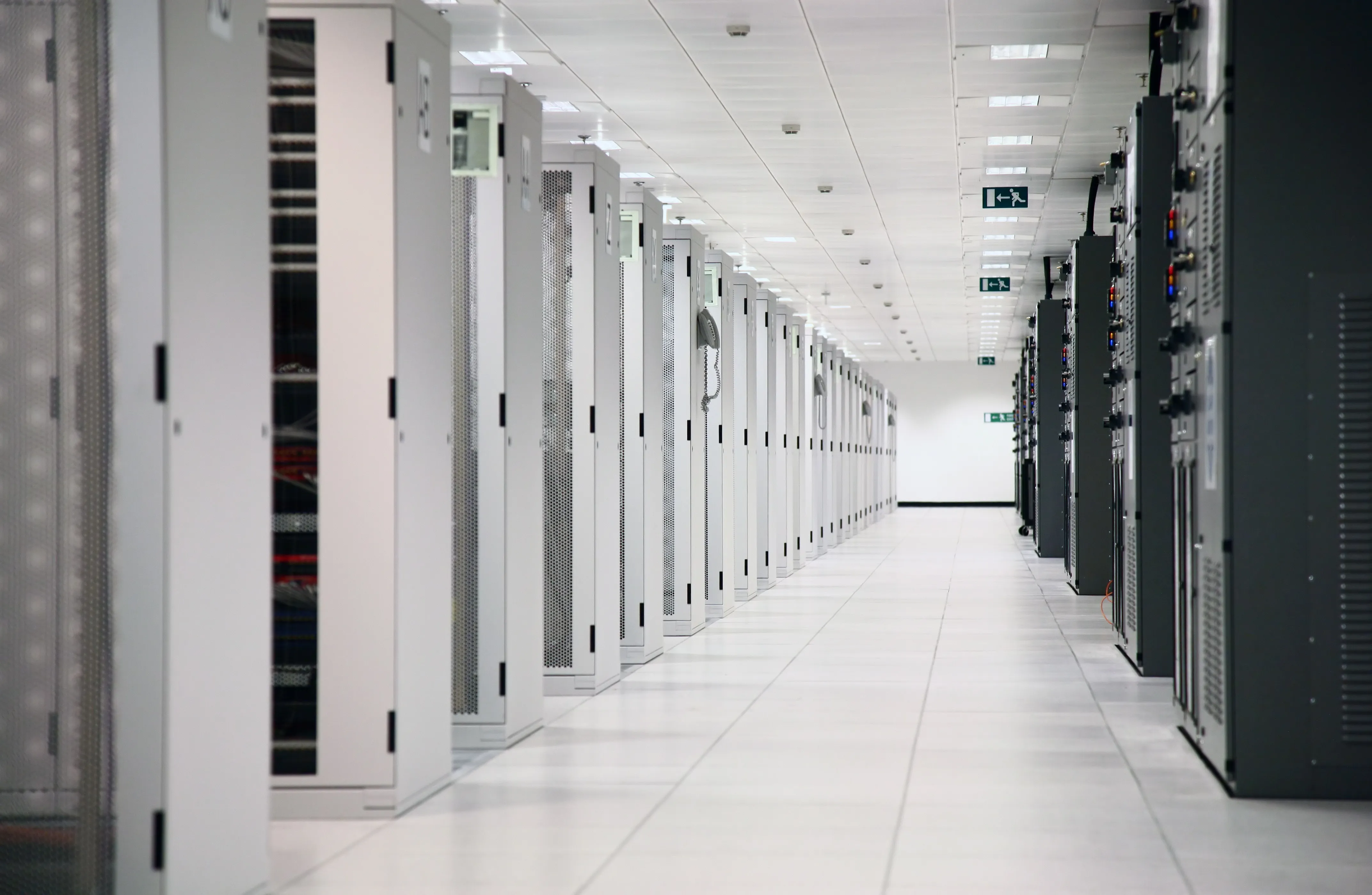
24MW Hyperscale DC
Mission Critical
24MW Hyperscale DC
Mission Critical
Mission Critical
Electrical
Wenatchee
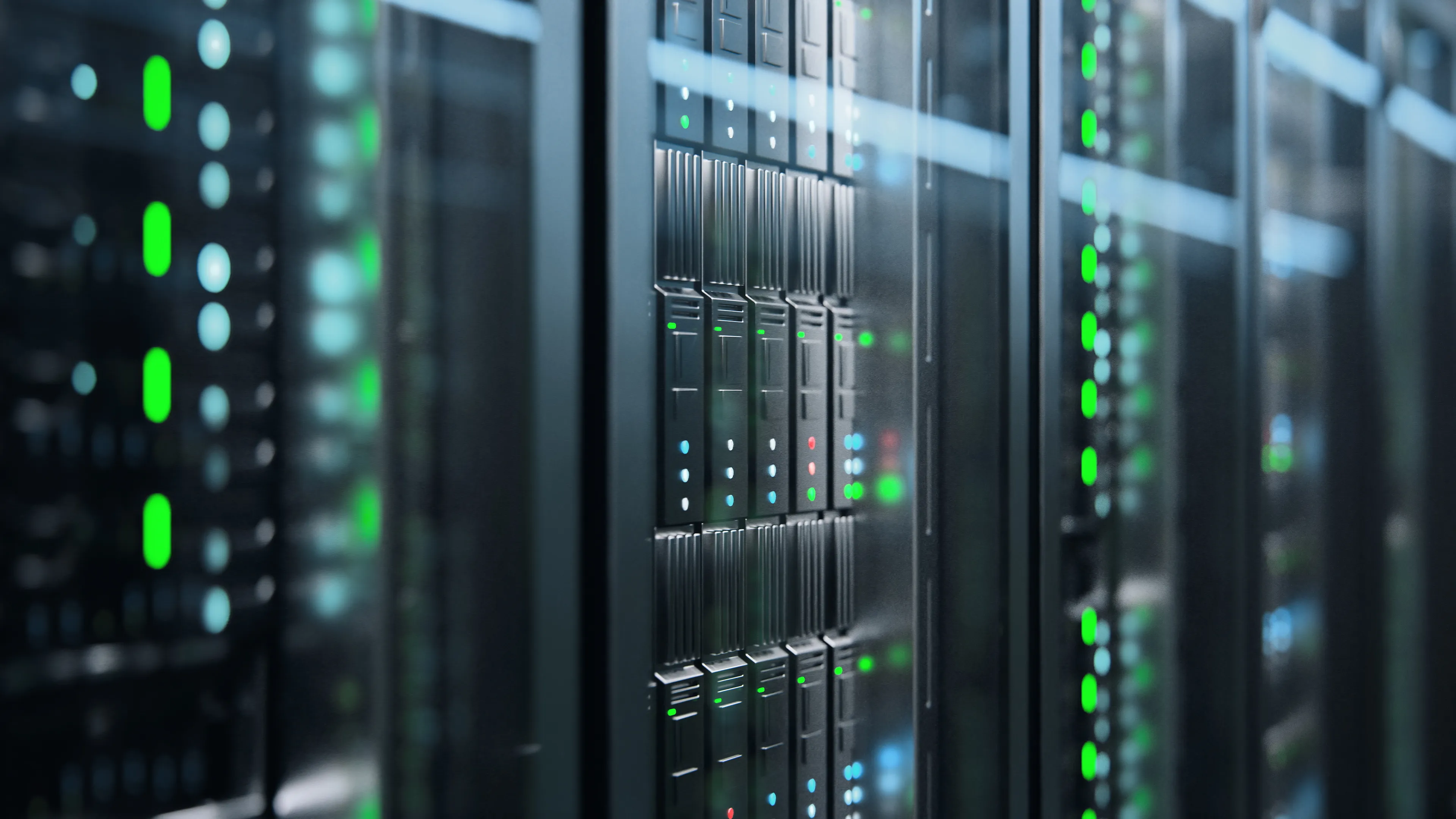
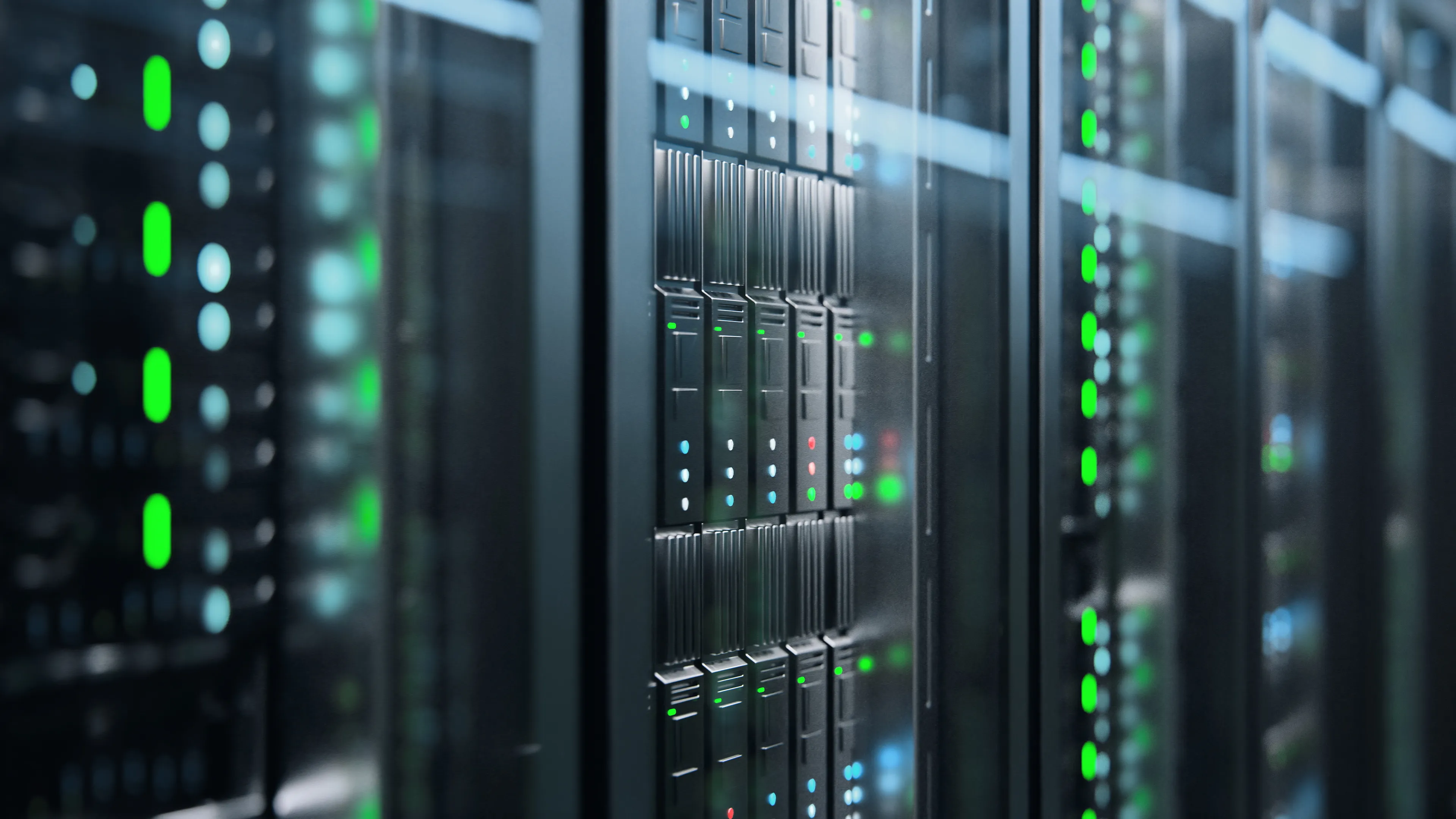
32MW Hyperscale DC
Mission Critical
32MW Hyperscale DC
Mission Critical
Mission Critical
Electrical
Wenatchee
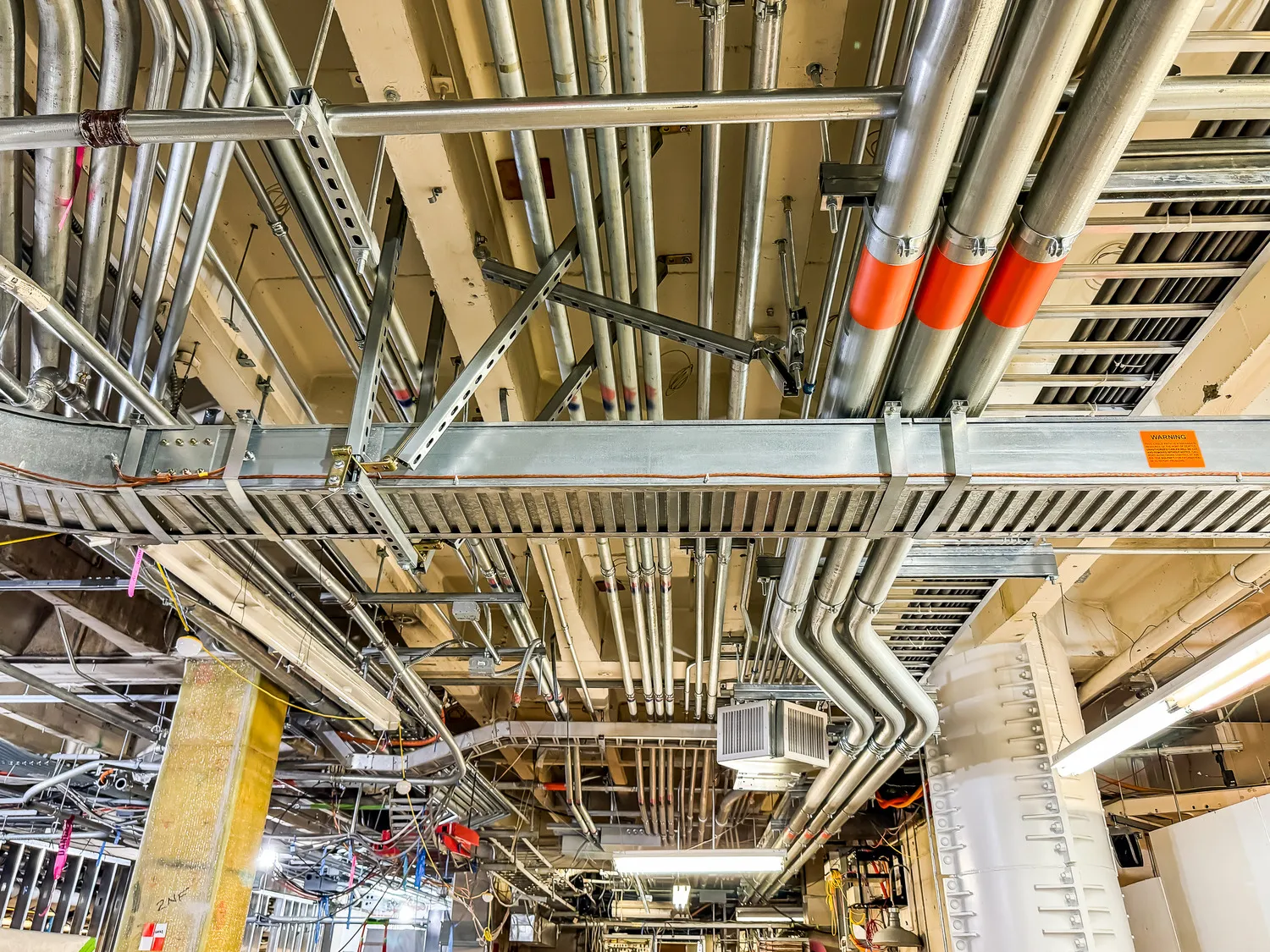
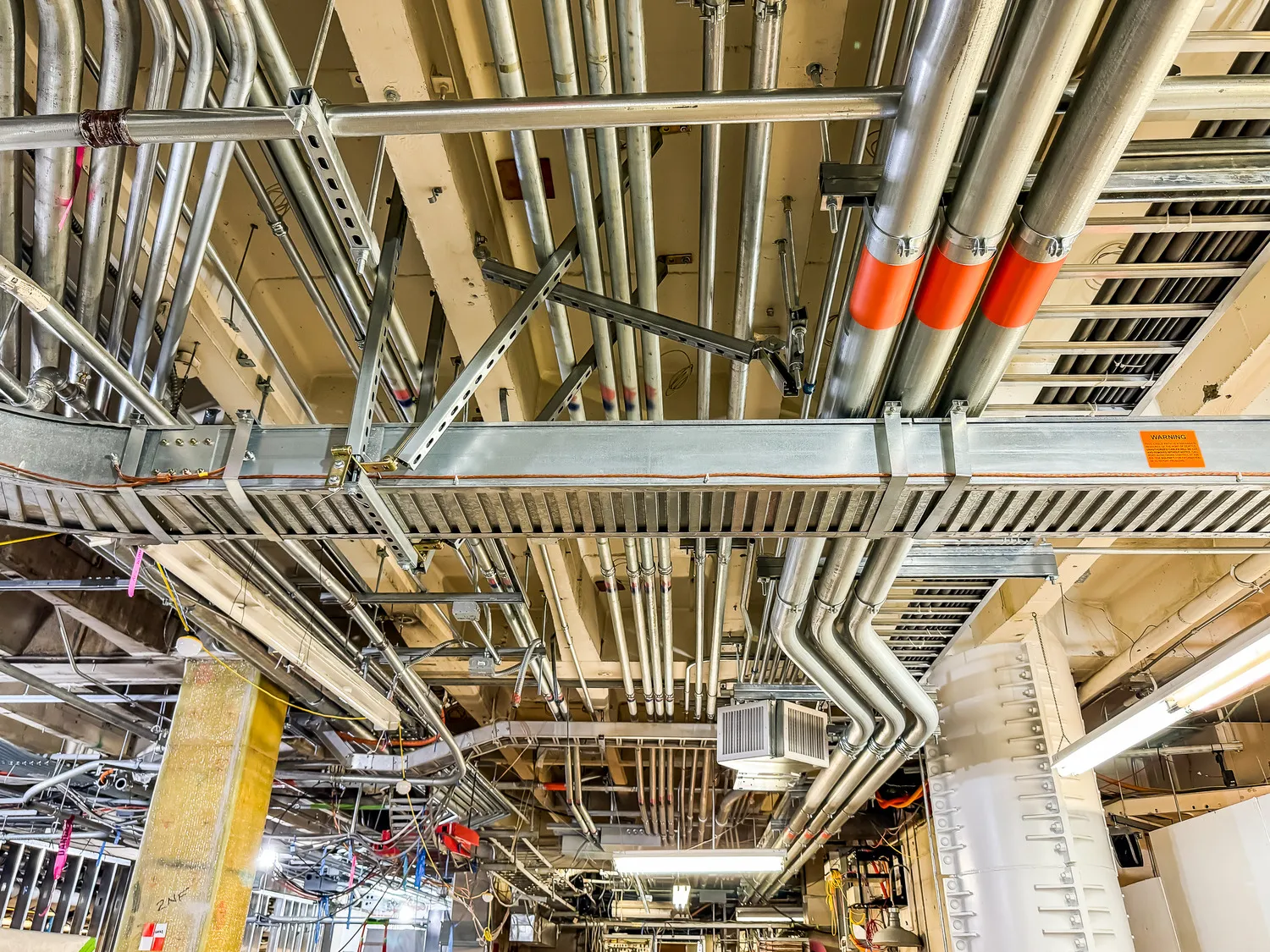
SEA - Main Terminal Low Voltage Upgrades
Transportation Infrastructure
SEA - Main Terminal Low Voltage Upgrades
Transportation Infrastructure
Transportation Infrastructure
Electrical
VDC, Alternative Delivery, Fabrication
Seattle
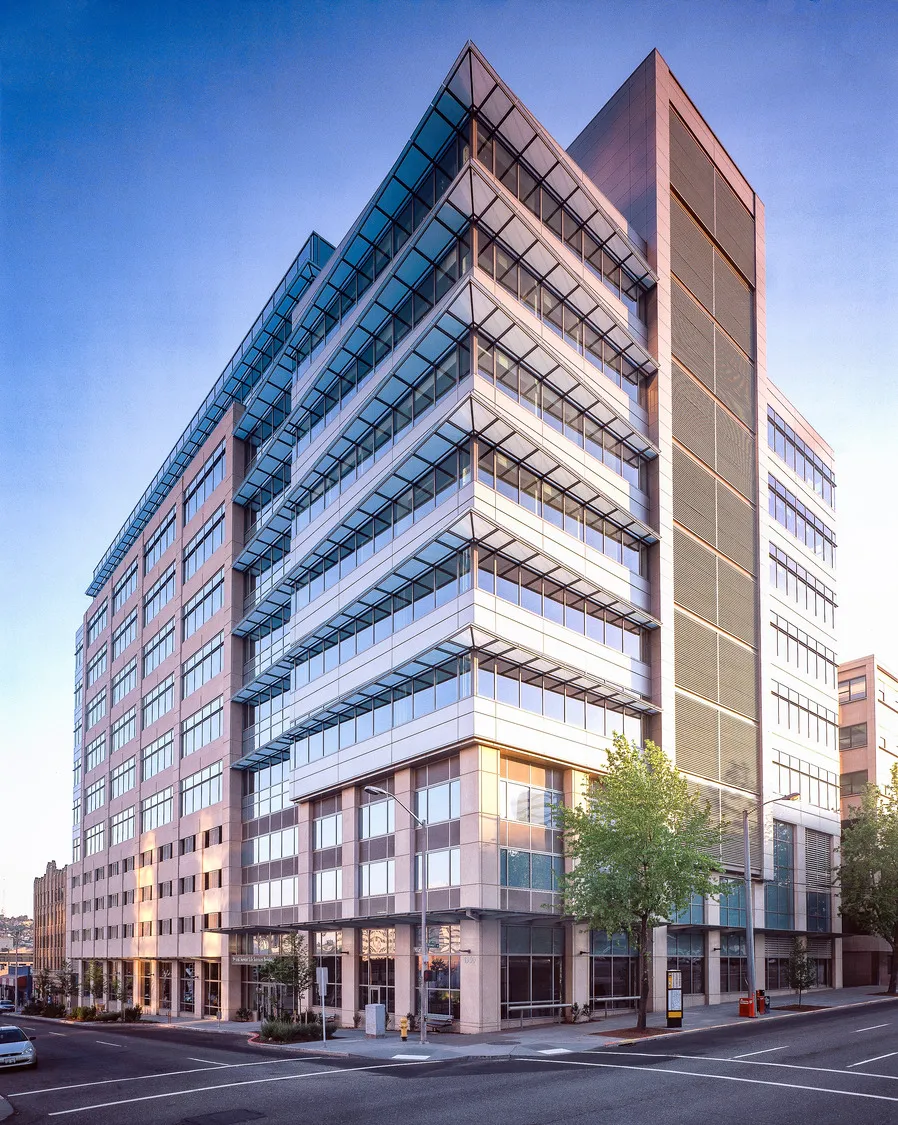
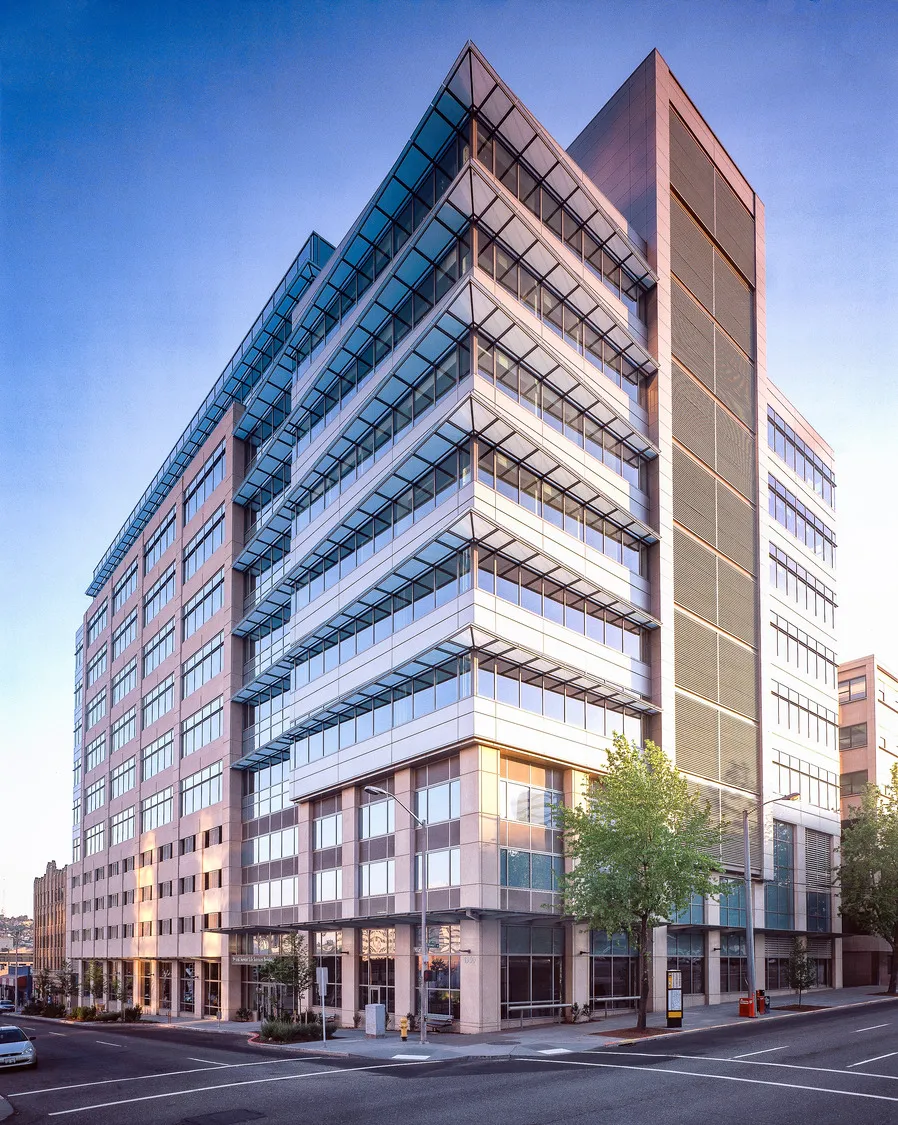
9th and Stewart Life Sciences Building
Life Sciences
9th and Stewart Life Sciences Building
Life Sciences
Life Sciences
Electrical
VDC
Seattle
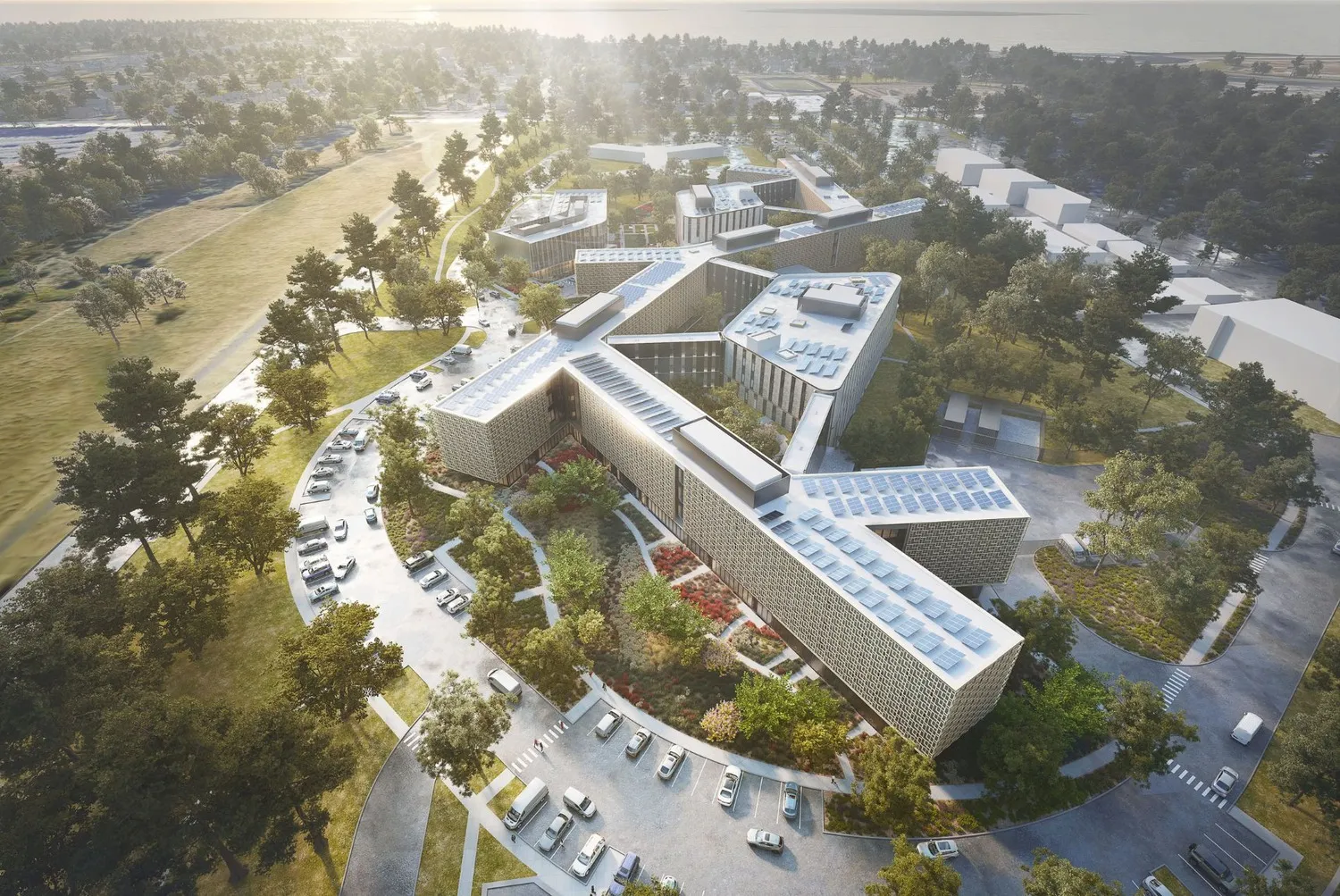
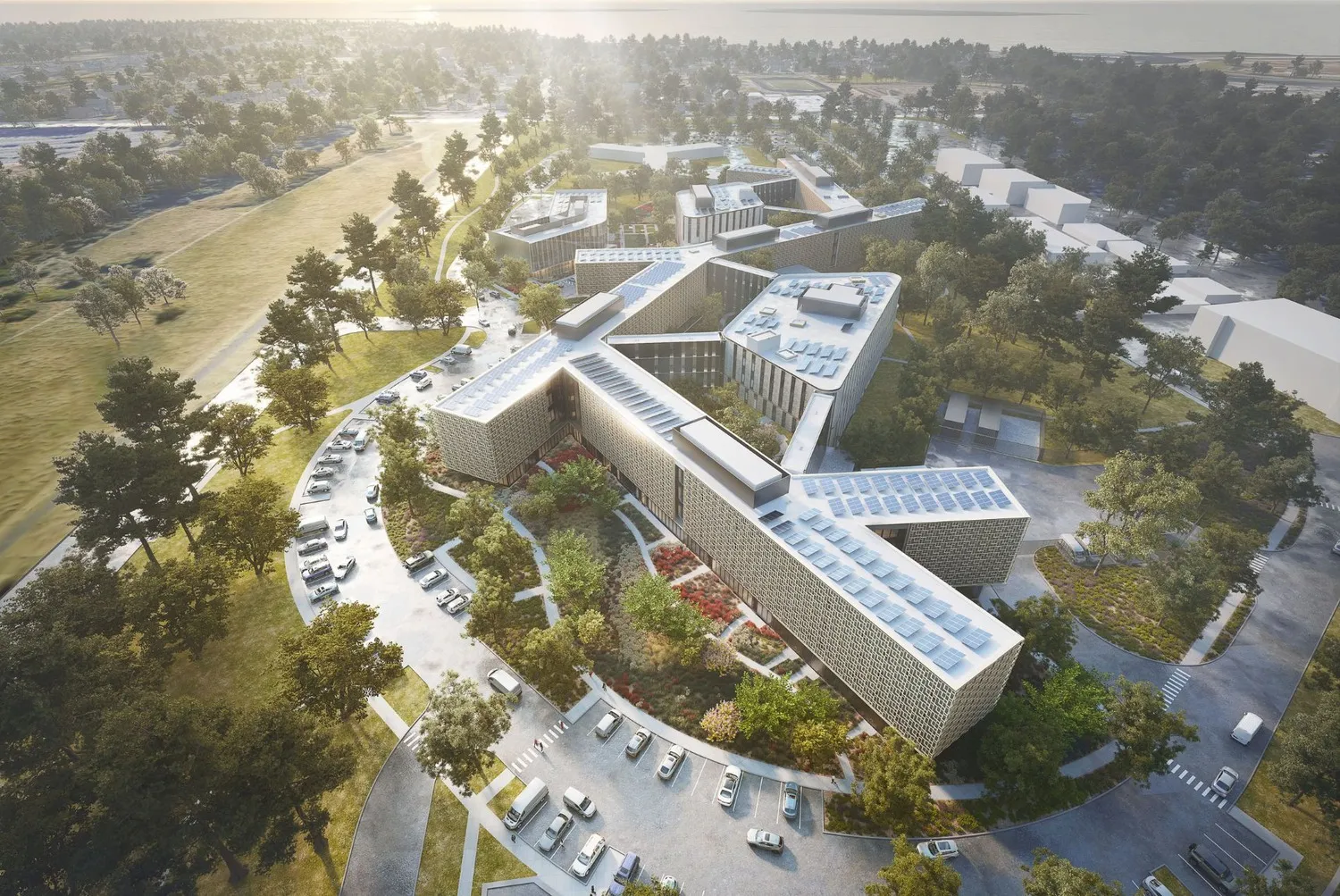
Western State Hospital - Forensic Center of Excellence
Healthcare
Western State Hospital - Forensic Center of Excellence
Healthcare
Healthcare
Electrical
Preconstruction, Sustainability, VDC, Fabrication
Seattle
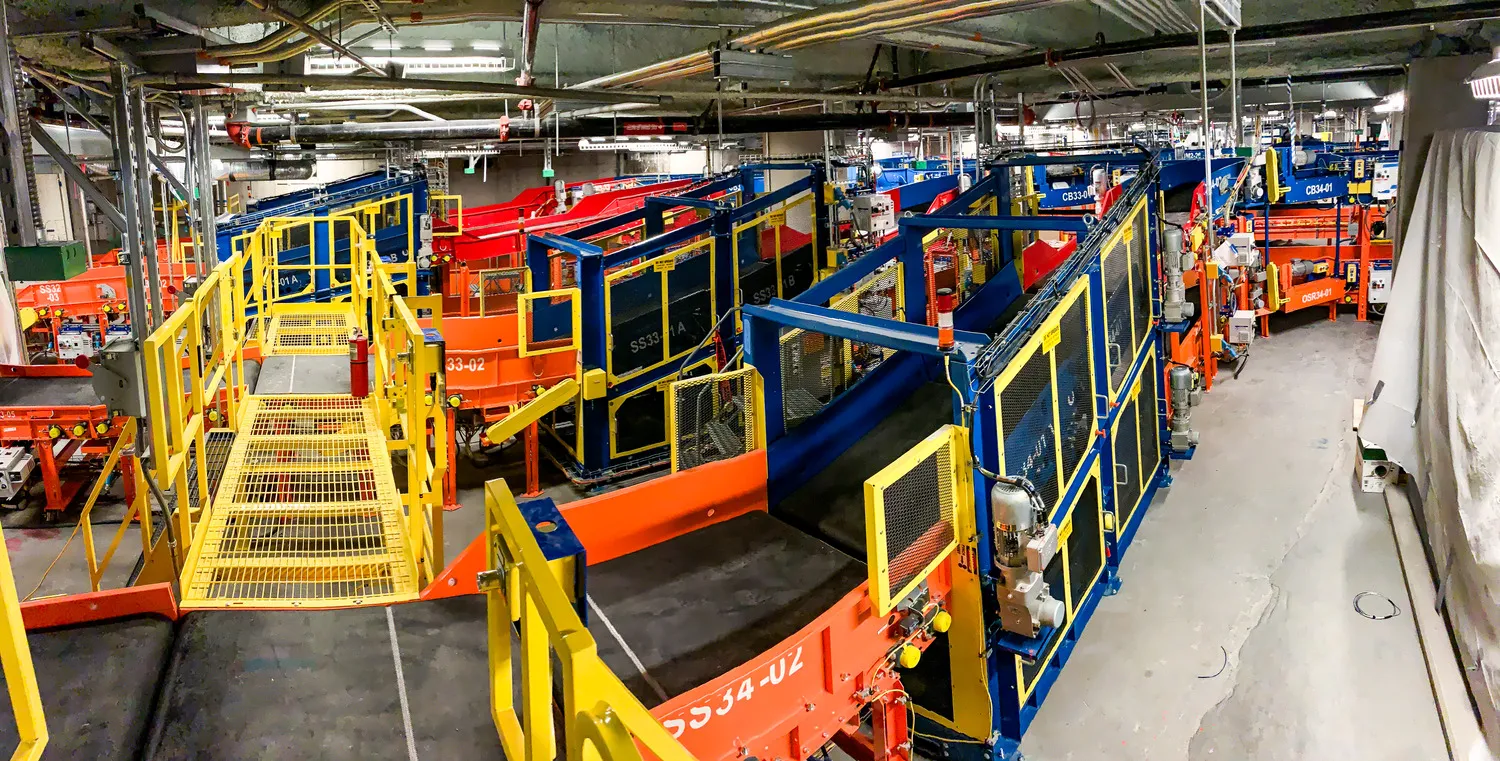
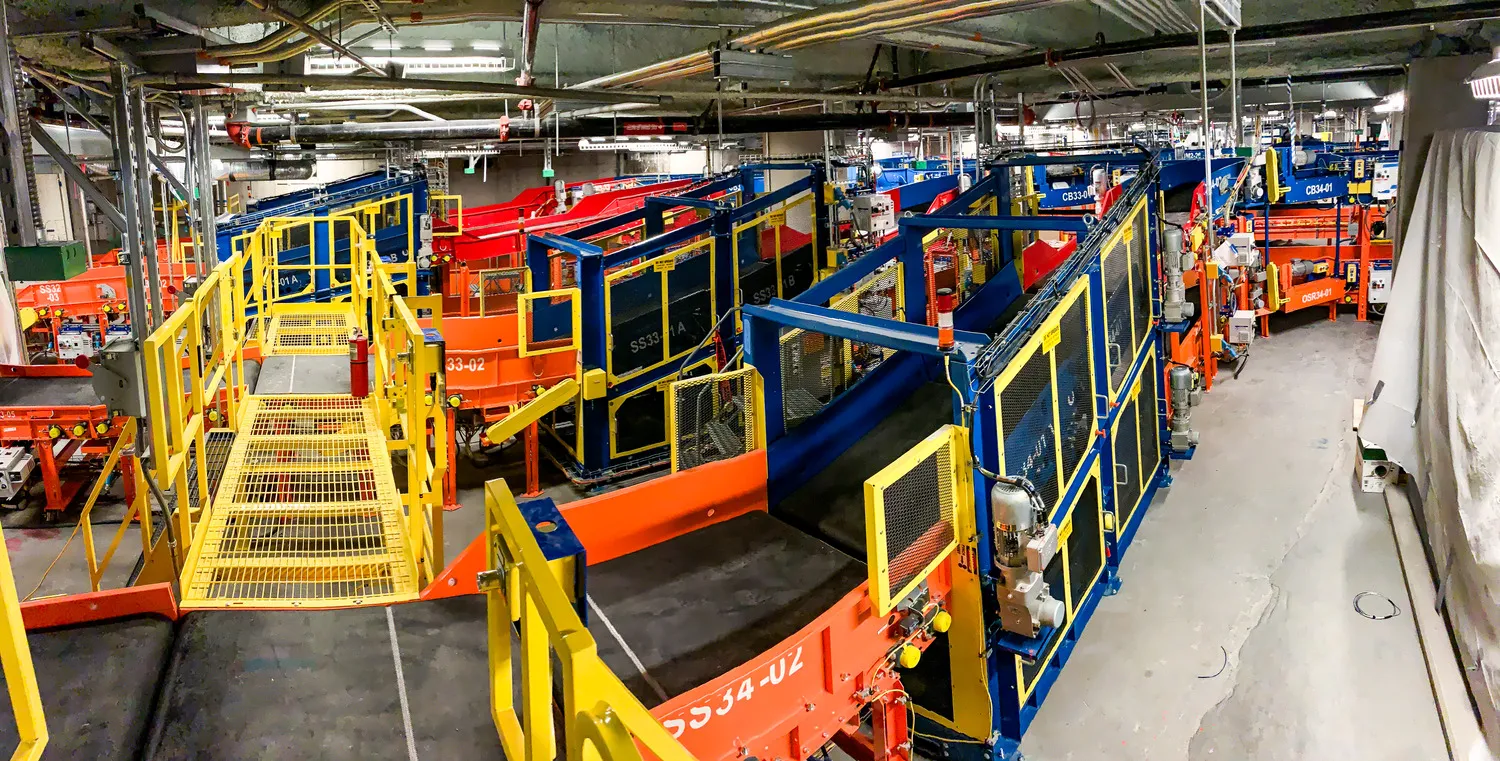
SEA - Baggage Optimization Phase 1
Transportation Infrastructure
SEA - Baggage Optimization Phase 1
Transportation Infrastructure
Transportation Infrastructure
Electrical
VDC, Diversity
Seattle
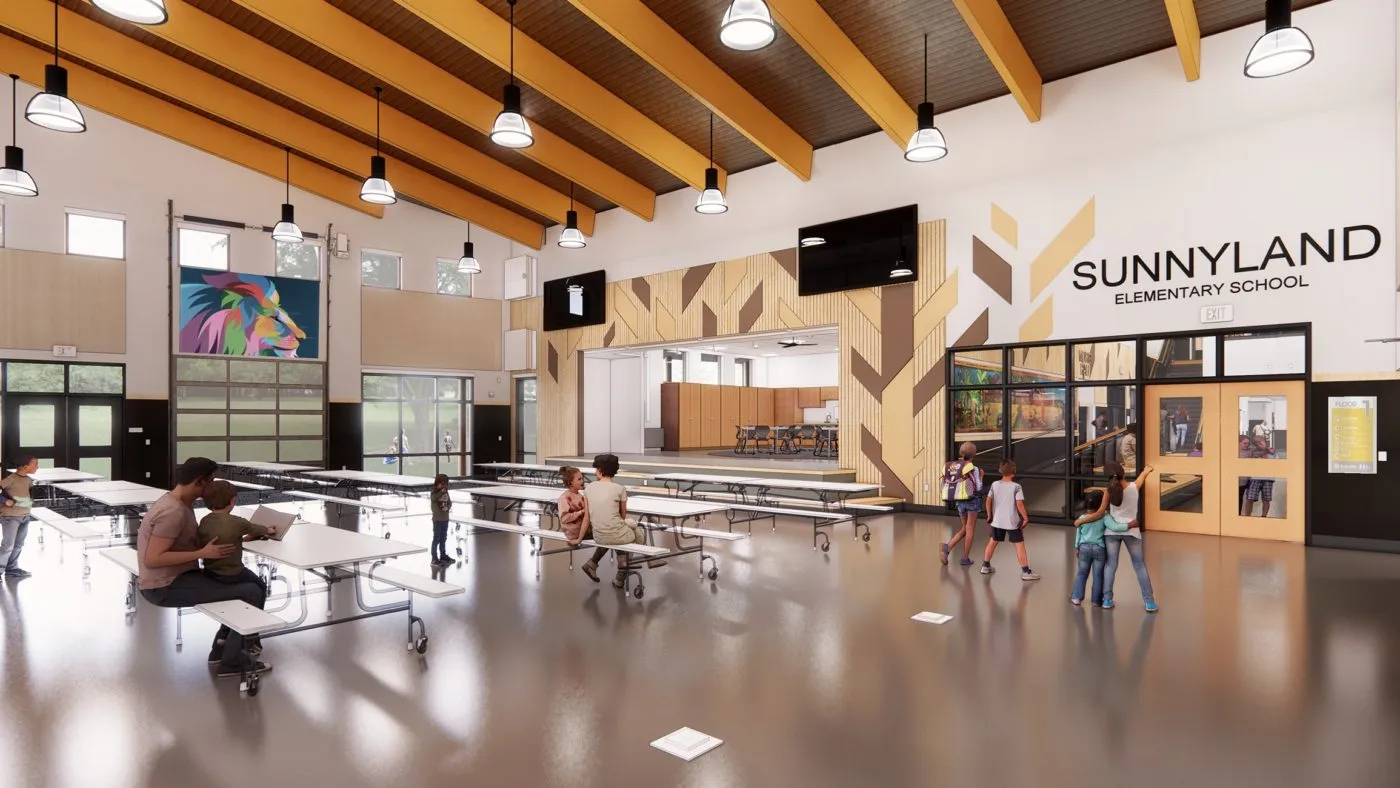
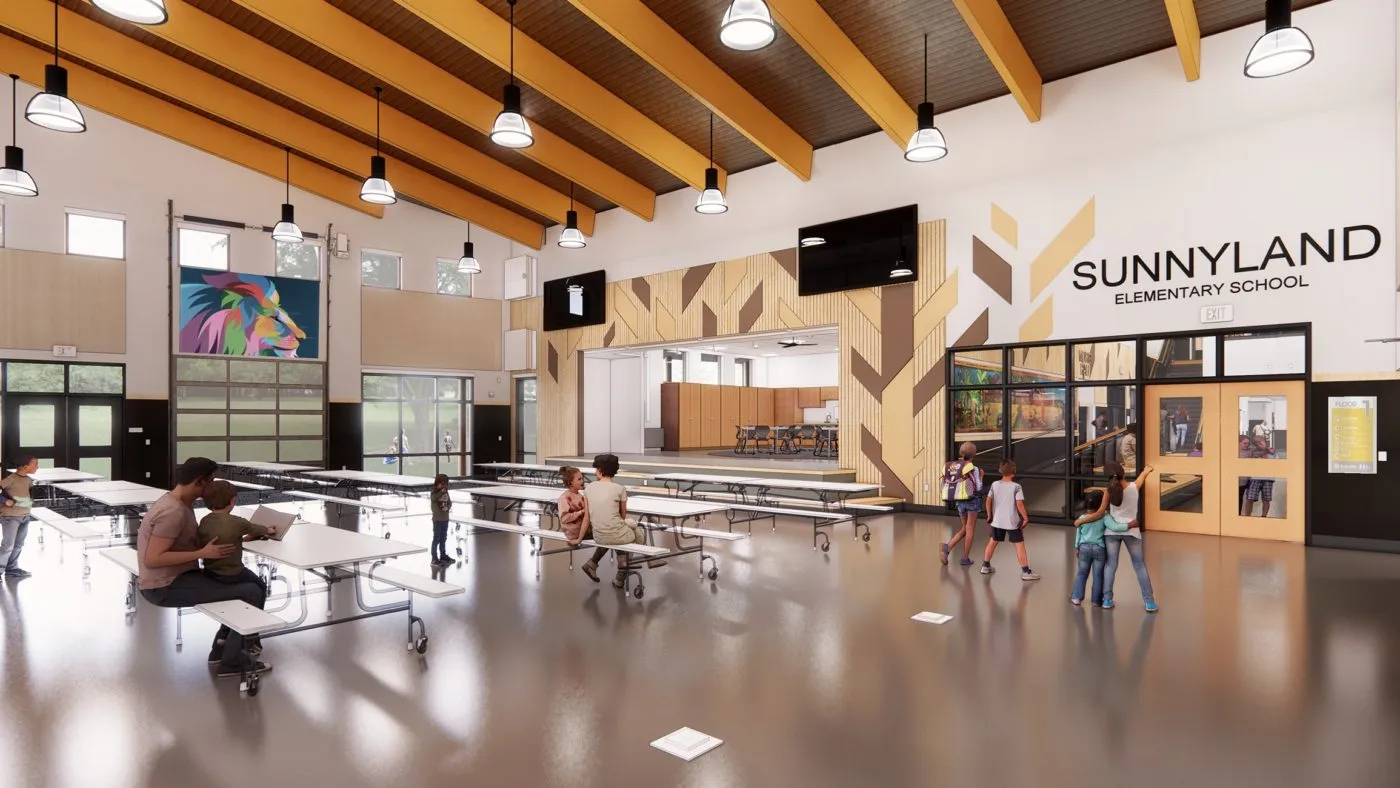
Sunnyland Elementary School Rebuild
Education
Sunnyland Elementary School Rebuild
Education
Education
Electrical
VDC
Bellingham
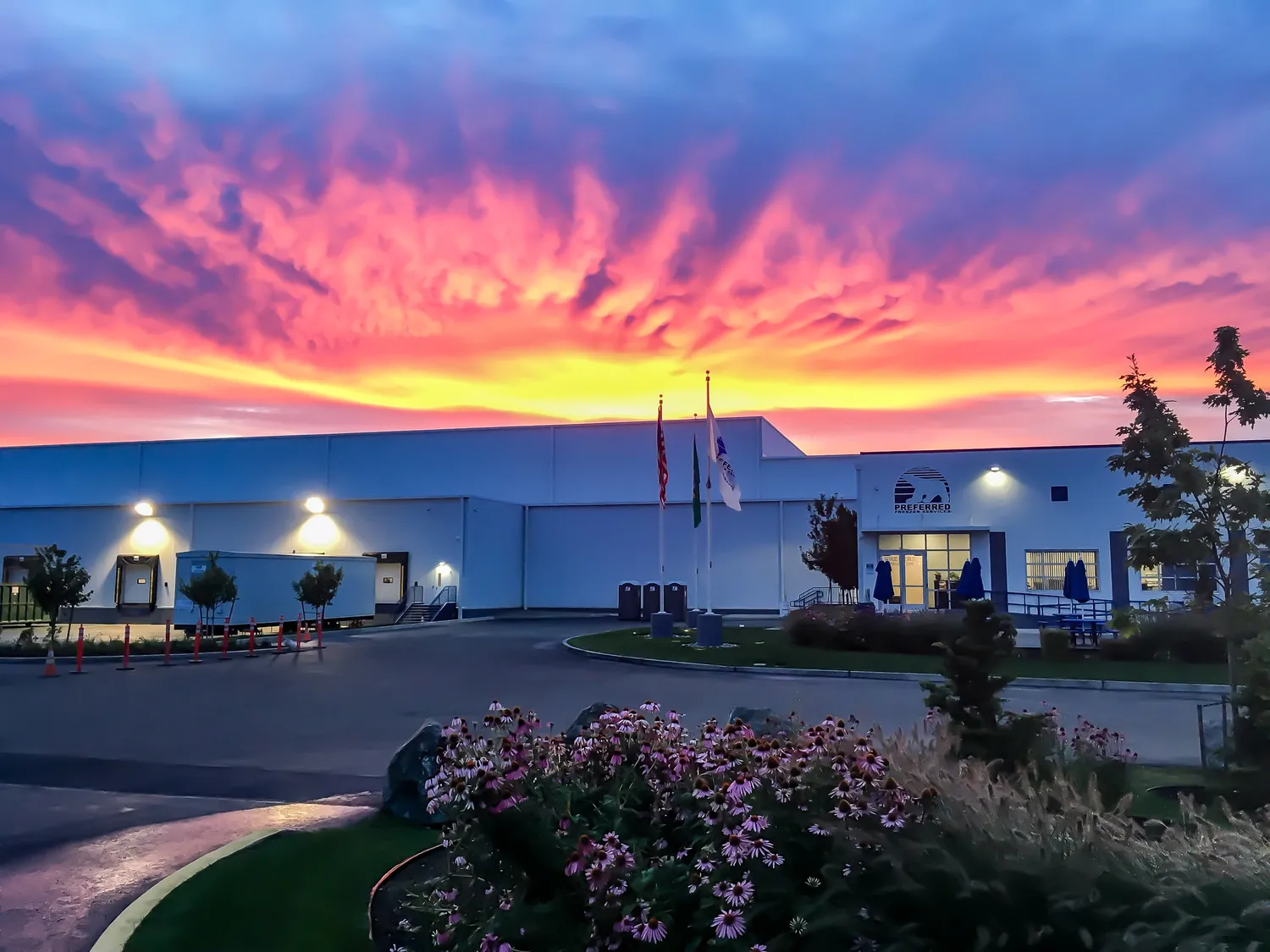
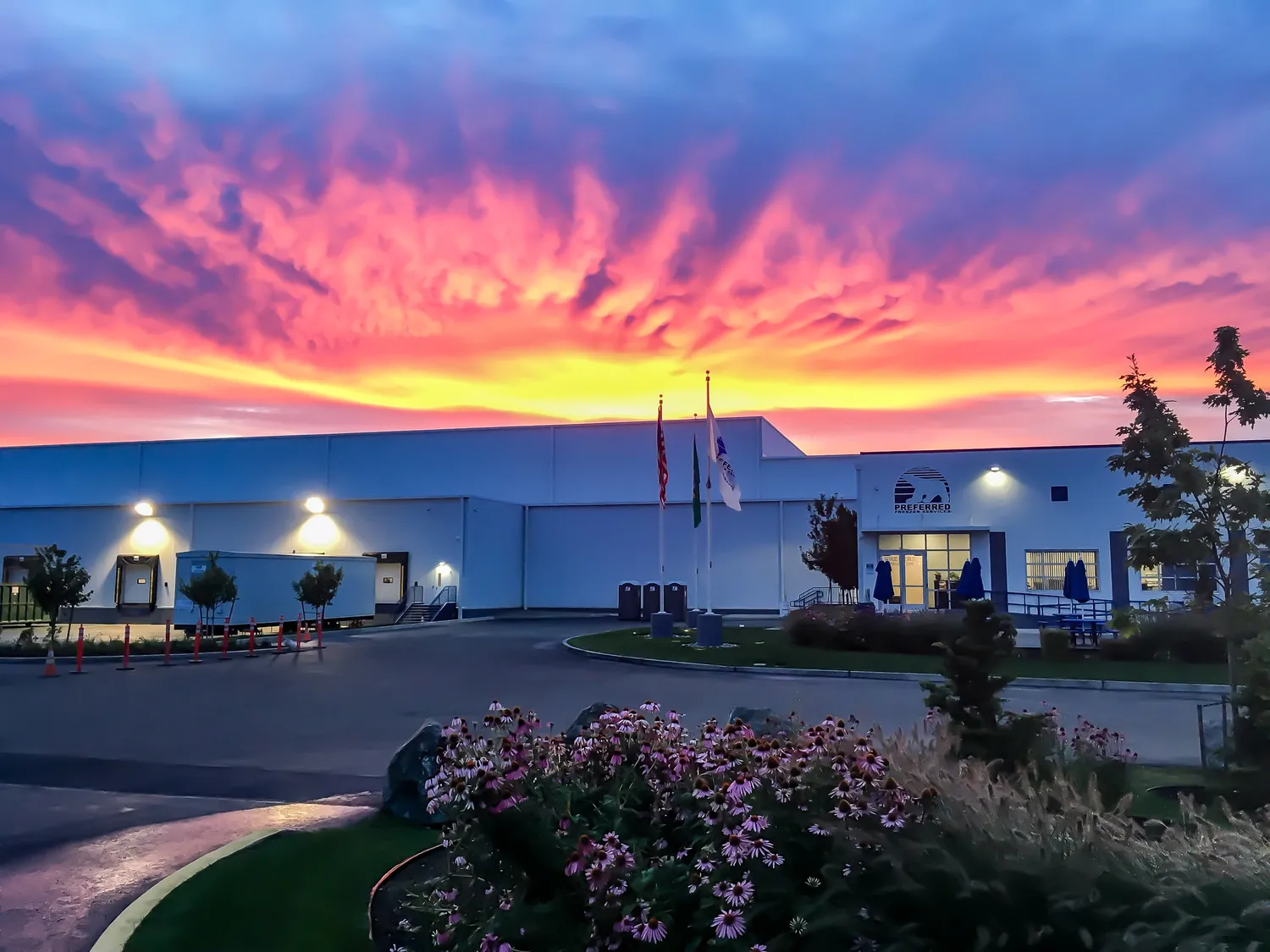
Preferred Freezer Lynden Cold Storage
Industrial & Manufacturing
Preferred Freezer Lynden Cold Storage
Industrial & Manufacturing
Industrial & Manufacturing
Electrical
Preconstruction, Fabrication
Bellingham
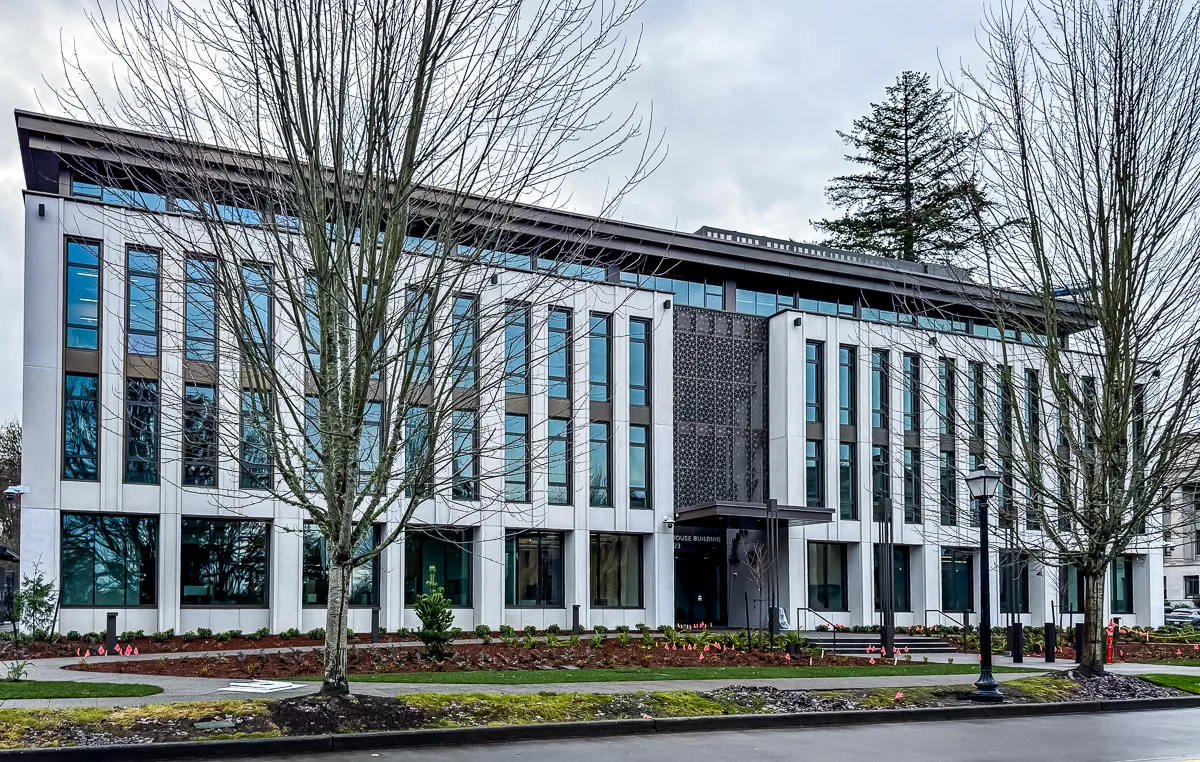
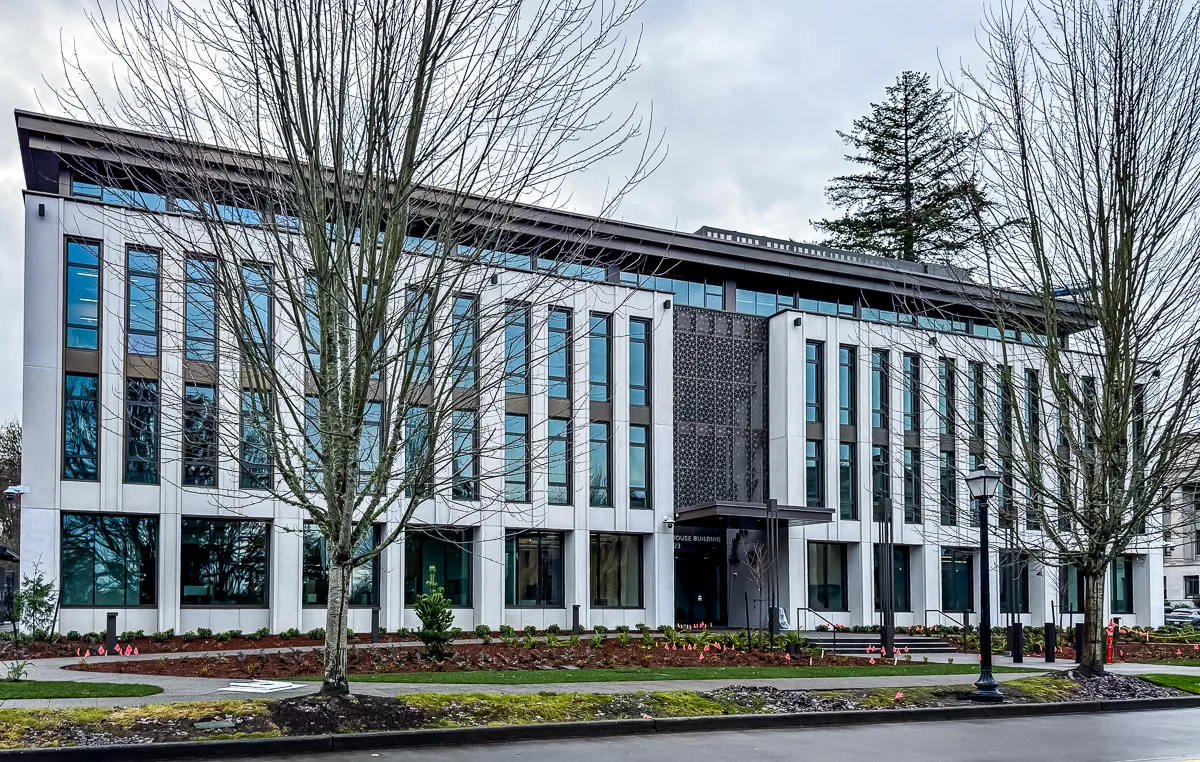
Newhouse Building Replacement
Government
Newhouse Building Replacement
Government
Government
Electrical, Technologies
Fabrication, Sustainability, VDC
Seattle
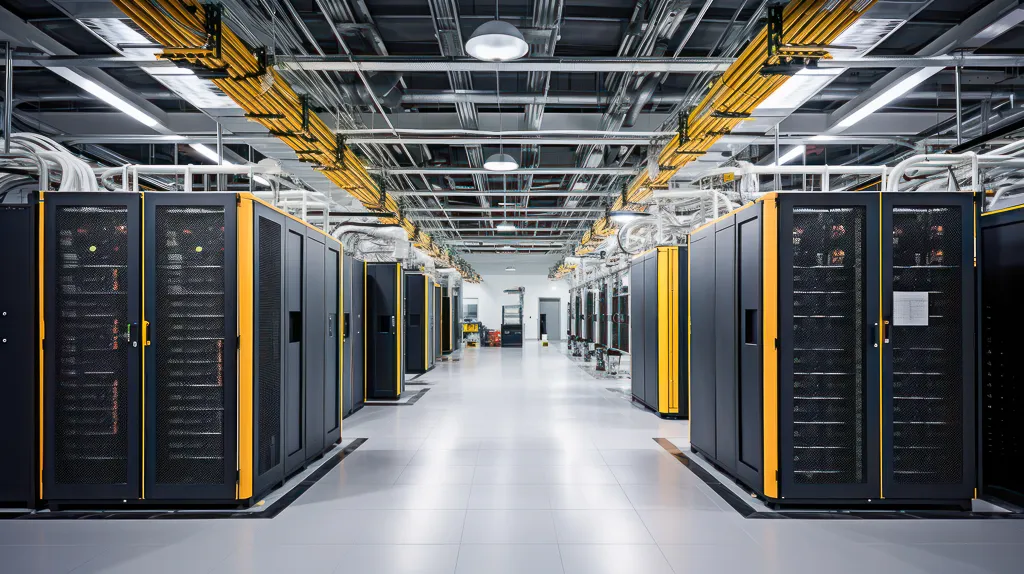
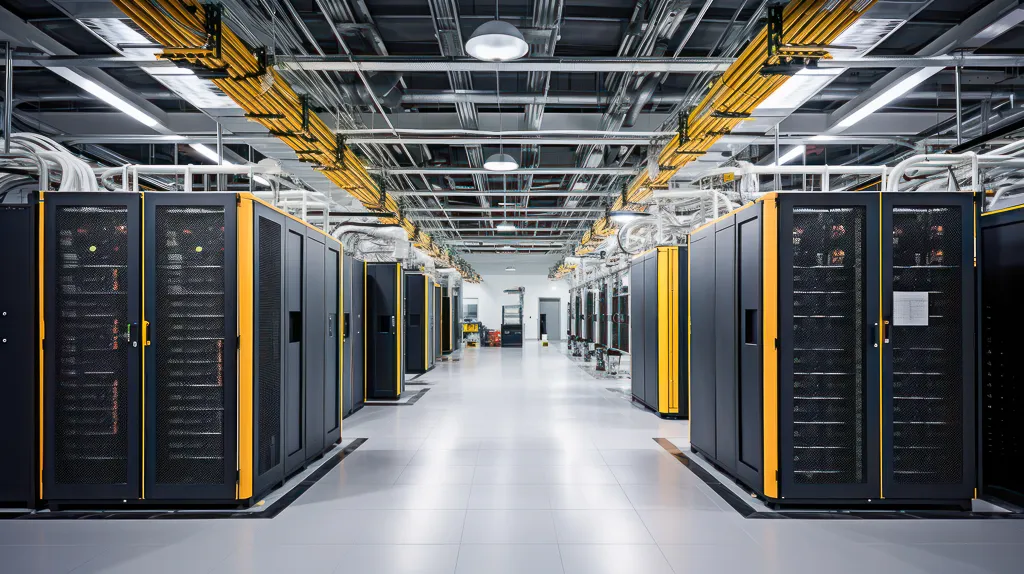
45MW Hyperscale DC - B
Mission Critical
45MW Hyperscale DC - B
Mission Critical
Mission Critical
Electrical
Wenatchee
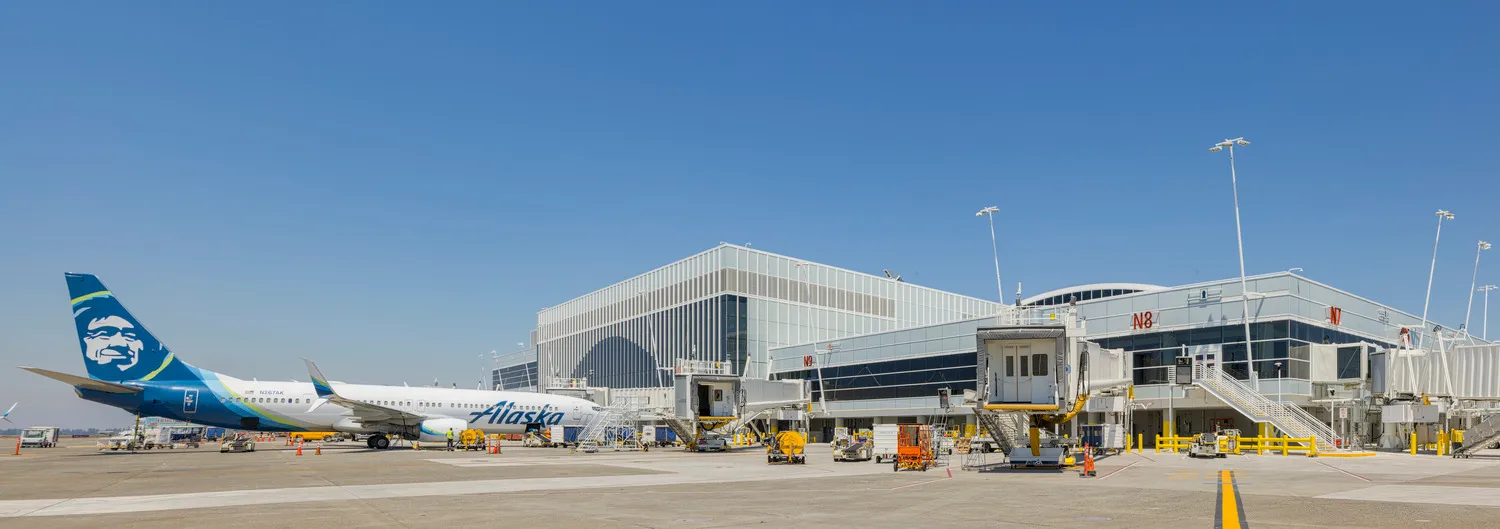
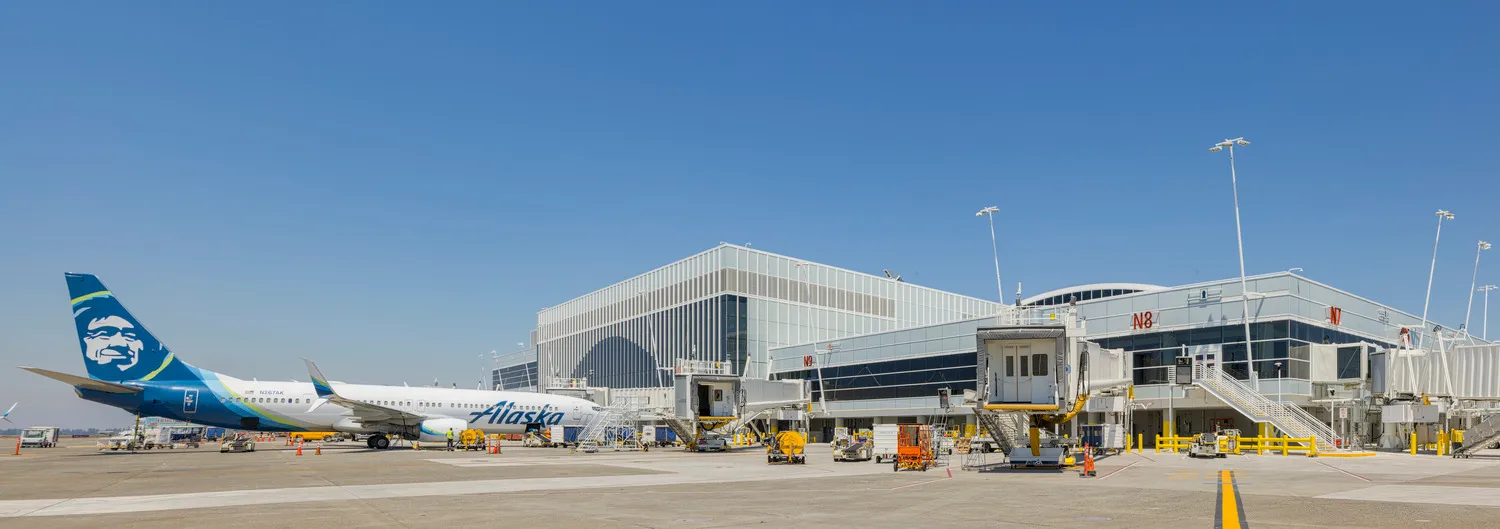
SEA - N Concourse Modernization
Transportation Infrastructure
SEA - N Concourse Modernization
Transportation Infrastructure
Transportation Infrastructure
Electrical
Sustainability, VDC, Fabrication, Alternative Delivery, Diversity
Seattle
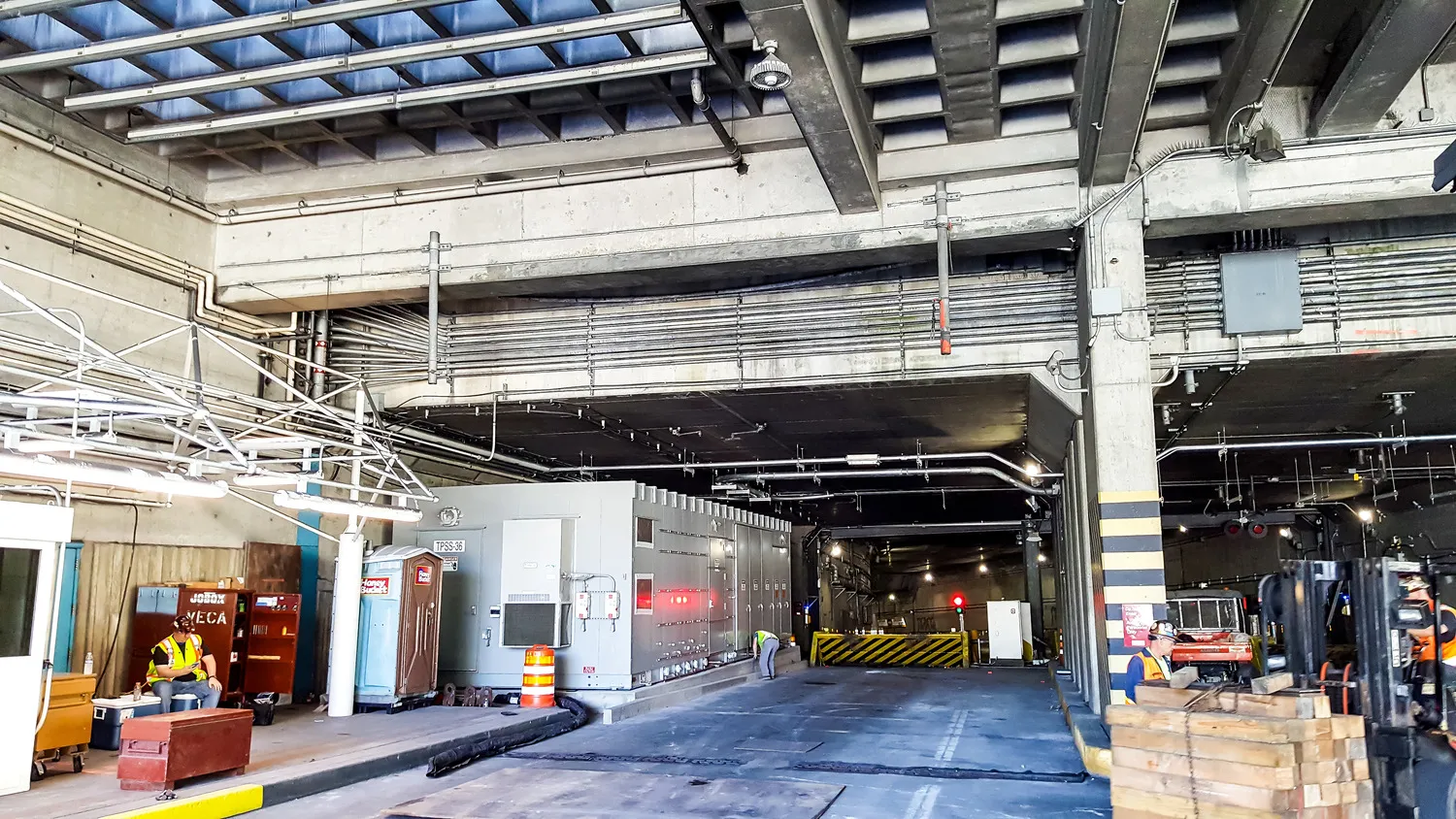
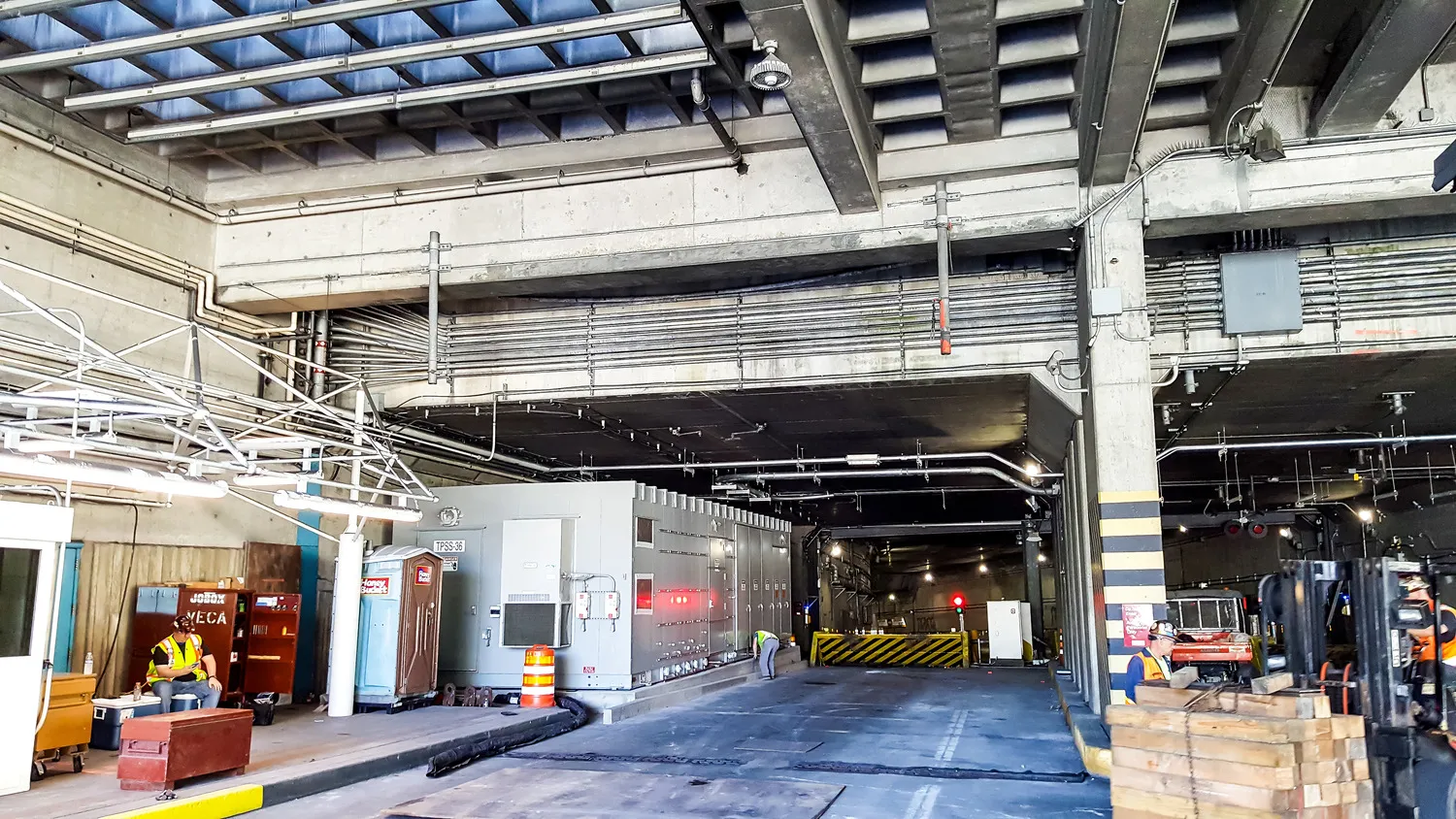
Olive Way (TPSS) Site Development Package
Transportation Infrastructure
Olive Way (TPSS) Site Development Package
Transportation Infrastructure
Transportation Infrastructure
Electrical
Alternative Delivery, VDC, Preconstruction
Seattle
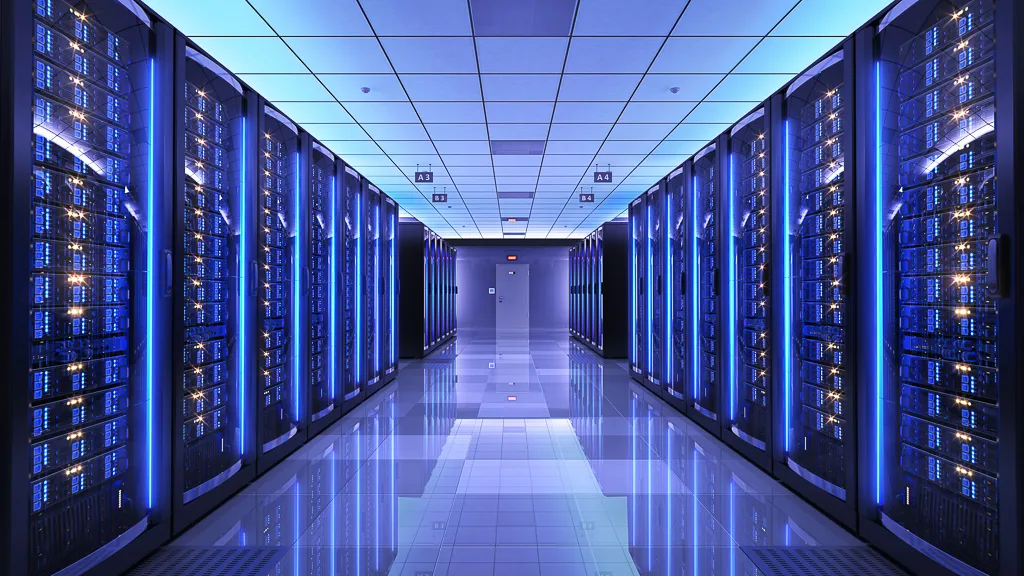
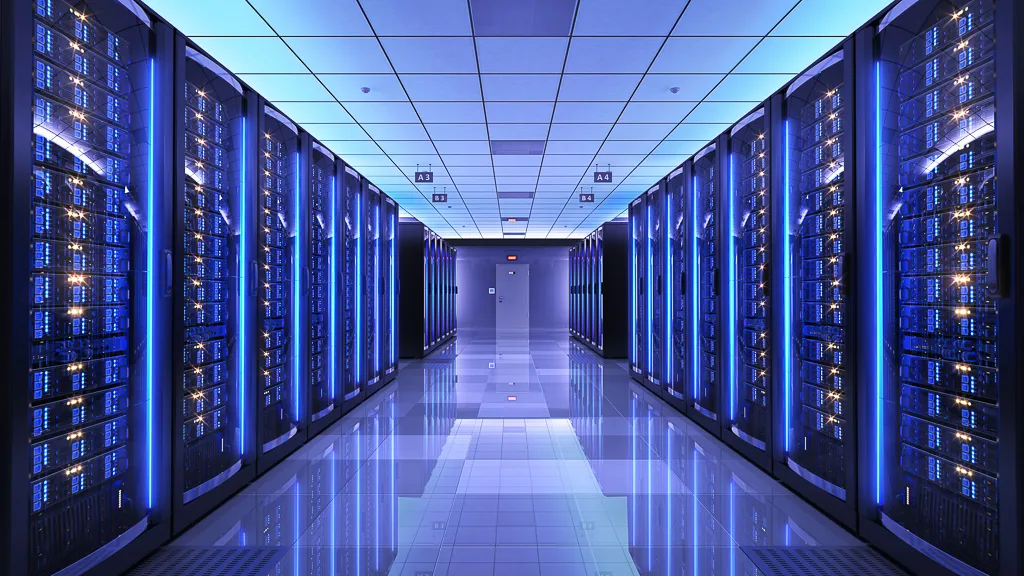
40MW Hyperscale DC
Mission Critical
40MW Hyperscale DC
Mission Critical
Mission Critical
Electrical
Wenatchee
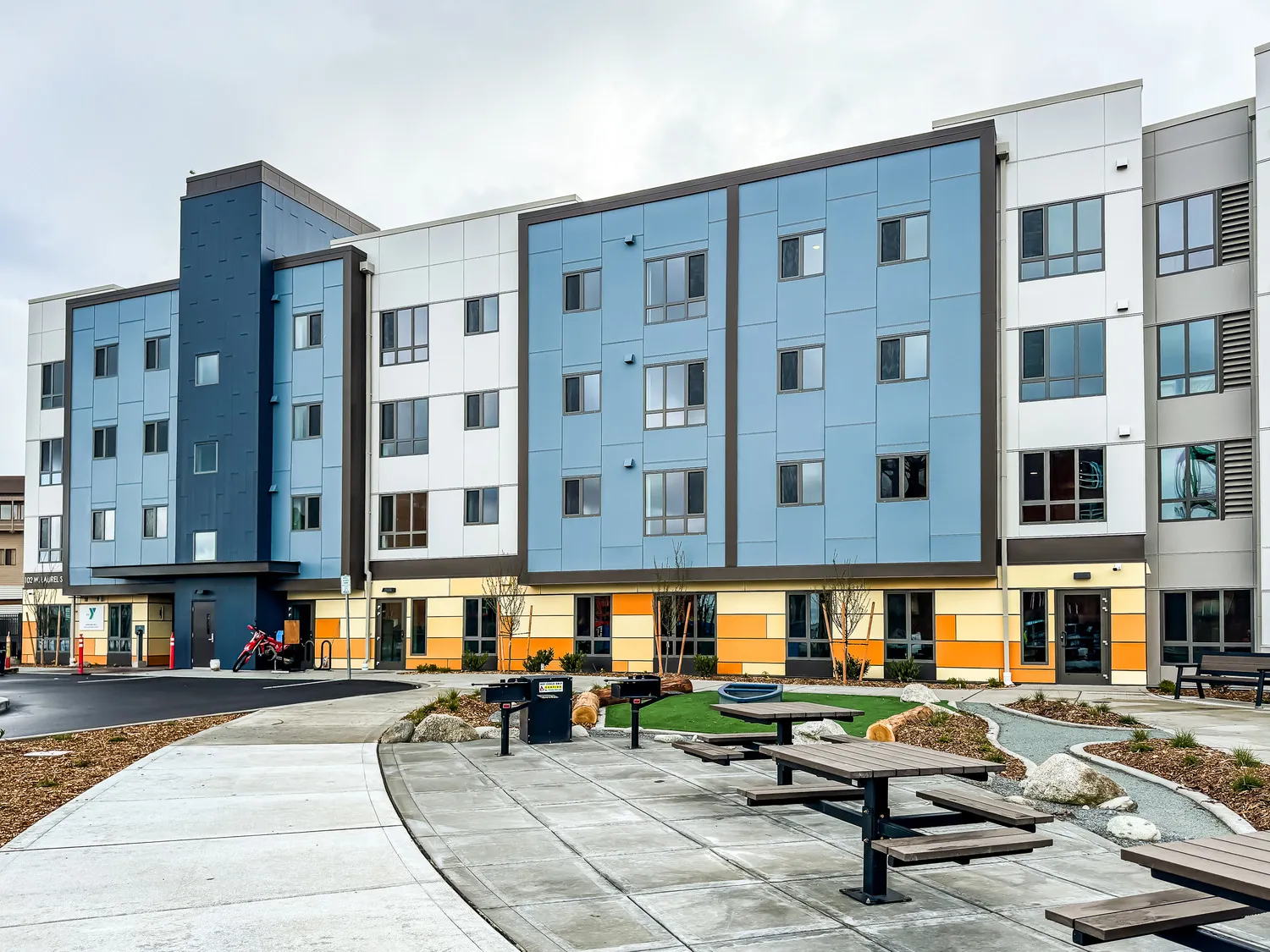
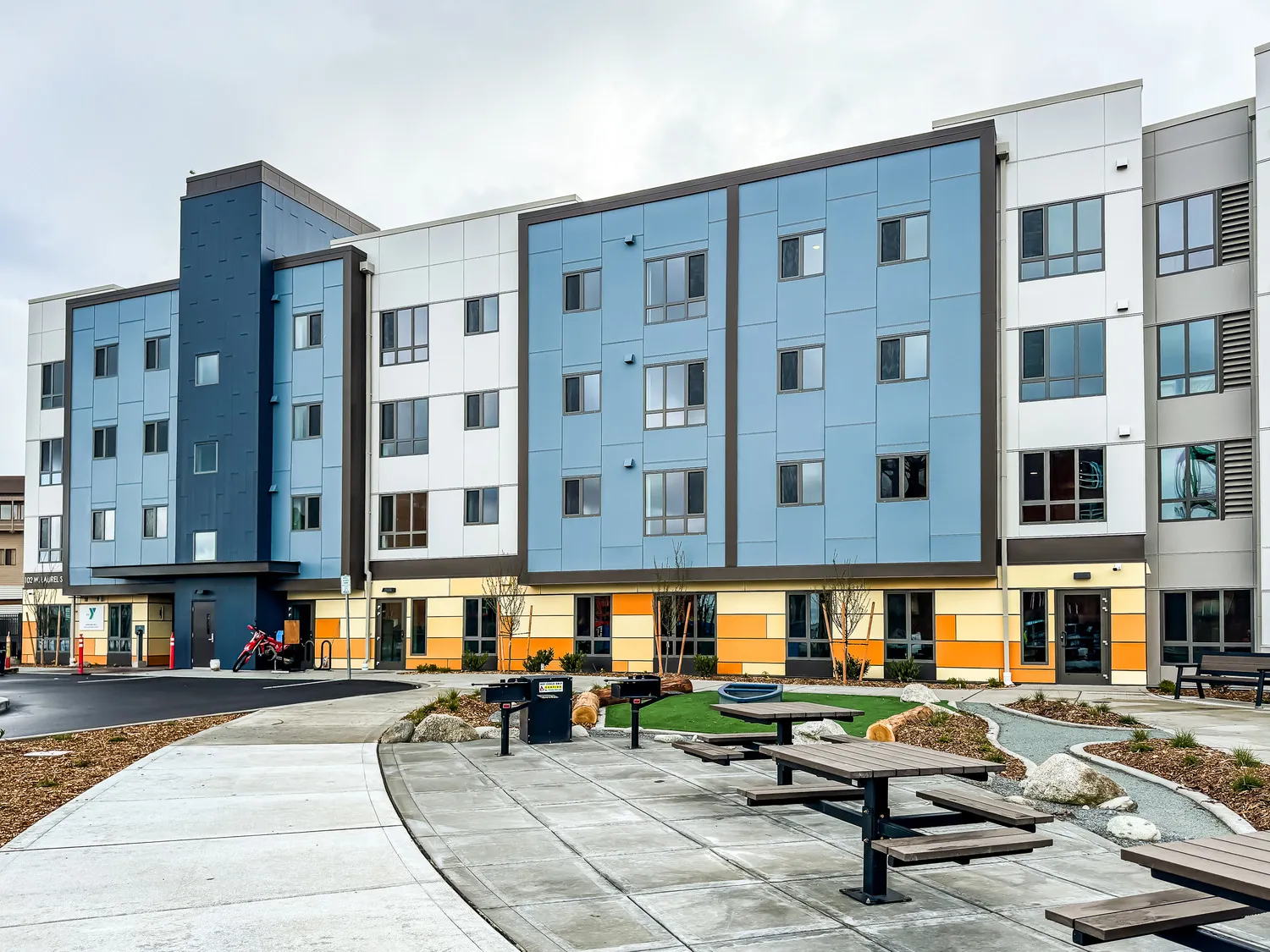
Mercy Millworks
Commercial
Mercy Millworks
Commercial
Commercial
Electrical
Fabrication, Sustainability, Preconstruction
Bellingham
Test Market
Government
Transportation Infrastructure
Life Sciences
Mission Critical
Healthcare
Education
Industrial & Manufacturing
Commercial
Service & Maintenance
Technologies
Electrical
Special Projects
Preconstruction
Sustainability
Diversity
EV Solutions
Panel & Automation
Alternative Delivery
Fabrication
VDC